Special piping situations, Electrical connections, Operation – Finish Thompson GP11 SERIES User Manual
Page 2: Seals
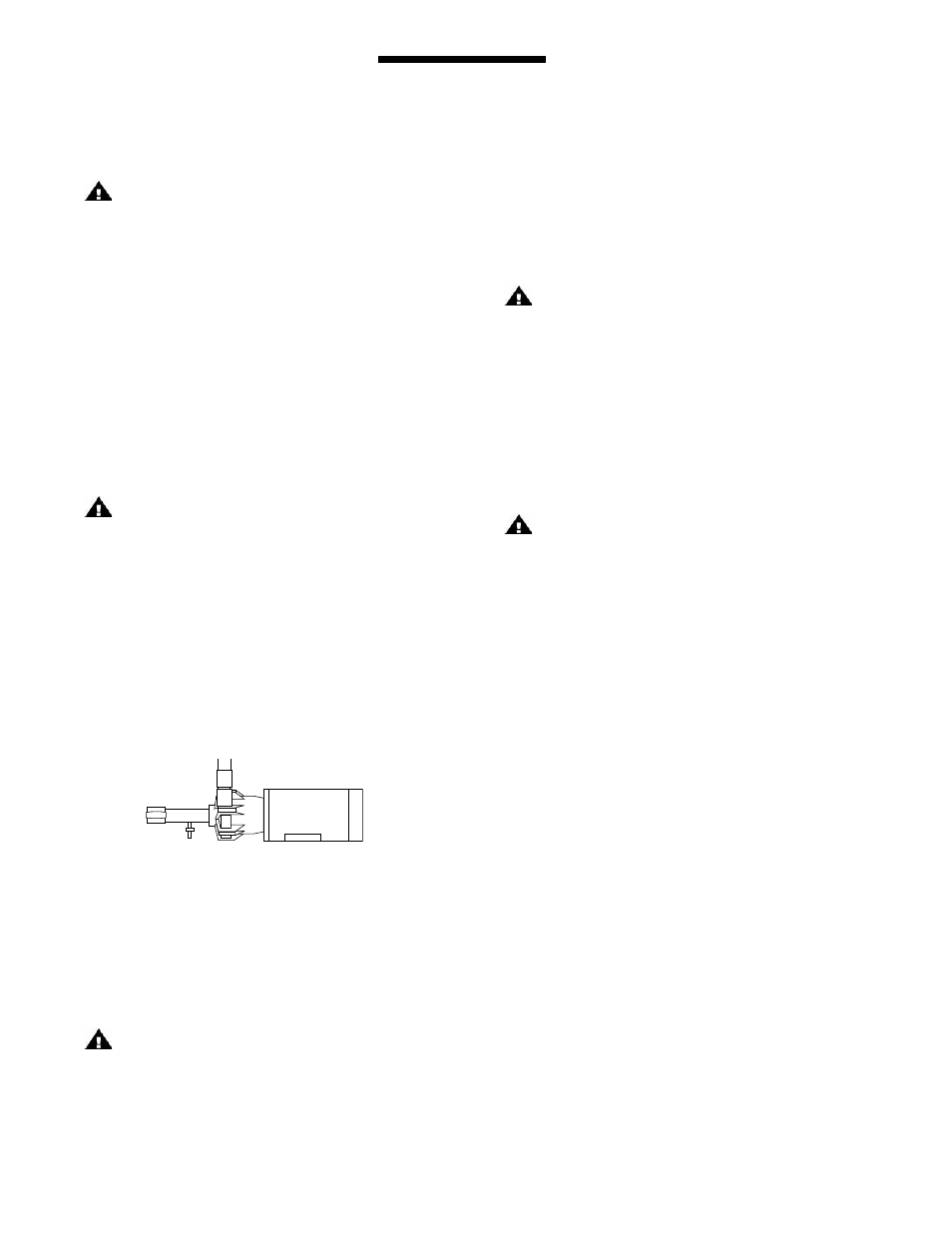
• For pumps with bellows or multi-spring seals, supply
one to two gallons water flow per hour at 1 - 2 psi.
• For pumps with a double seal, supply one to two
gallons per hour water flow at 5 - 10 psi ABoVE the
discharge pressure of the pump.
CAUtioNs:
1. Never run a pump equipped with a cooling collar
without a proper water supply. Doing so will result in
damage to the pump. Use of a flow switch is
recommended.
2. Do not over-pressurize the cooling collar’s water
supply. Doing so can result in damage to pump
components.
SpEcIAL pIpINg SITuATIONS
sUCtioN liFt
1. install a priming chamber on the feed side of the pump or
appropriate piping on the discharge for priming the pump.
2. install a foot valve on the bottom of the suction piping to
maintain a prime to the pump.
CAUtioN: suction prime must be maintained at all
times. running the pump dry will cause damage to pump
components. to protect the pump if prime is lost, use a
pressure switch on the discharge, a vacuum switch on the
suction, or a motor minder to monitor motor current draw.
PUmPiNg liqUiDs WhiCh mAy soliDiFy or
CrystAllizE
Add a flush system to the pump’s piping to prevent accumula-
tion of material inside the pump. install water inlet and outlet
valves as shown in Figure 2. refer to the “operation” section of
these instructions for the flush procedure.
ELEcTrIcAL cONNEcTIONS
1. Perform the motor wiring according to NEC requirements
and local electrical codes.
2. Wire the motor for counter clockwise rotation when facing
the face of the motor .
CAUtioN: Before starting the pump, momentarily
“jog” the motor while looking through the suction of the
pump to determine if the motor is wired for the correct rota-
tion. refer to the directional arrow on the pump.
OpErATION
FlooDED sUCtioN systEms
1. Fully open the suction and discharge valves.
2. if a cooling collar is used, turn on the cooling water.
3. start the pump and verify liquid is flowing. if there is no
liquid flow, refer to the “troubleshooting” section of these
instructions.
4. Adjust the flow rate and pressure by regulating the dis-
charge valve.
CAUtioN: Never attempt to adjust the liquid flow with
the suction valve. limiting the suction will result in dam-
age to pump components.
sUCtioN liFt systEms
1. Fully open suction and discharge valves.
2. if a cooling collar is used, turn on the cooling water.
3. Prime the pump by filling the priming chamber. Allow time
for any trapped air in the suction piping to escape.
4. start the pump. Adjust the flow rate and pressure by
reguating the discharge valve.
CAUtioN: Never attempt to adjust the liquid flow with
the suction valve. limiting the suction will result in dam-
age to pump components.
FlUsh systEms
1. Fully close the suction and discharge valves.
2. Connect the water supply to the water inlet valve and con-
nect a drain hose to water outlet valve.
3. turn on the water supply and open the inlet and outlet
valves. Flush the system until the pump has been cleared
of any material buildup (approximately 5 minutes).
4. Close the inlet and outlet valves and turn off water supply.
SEALS
sEAl rEmoVAl AND iNsPECtioN
1. Disconnect the piping and electrical power from the pump.
2. Disassemble the pump from the motor adapter.
a. remove the six hex-head cap screws from the
impeller housing. the impeller housing will loosen if
gently tapped at the discharge outlet.
b. remove the protective shroud from the motor adapter.
c. While preventing the motor shaft from moving (insert
a screwdriver into the motor’s fan), unscrew the
impeller from the motor shaft. remove the impeller,
seal, cooling collar (if applicable) and housing cover
as one assembly from the motor shaft.
NotE: For pumps using a 56C/145tC or motor adapter,
leave the shaft adapter secured to the motor shaft.
Figure 2
2