Magnum Venus Plastech UNIVERSAL PROPORTIONER User Manual
Page 16
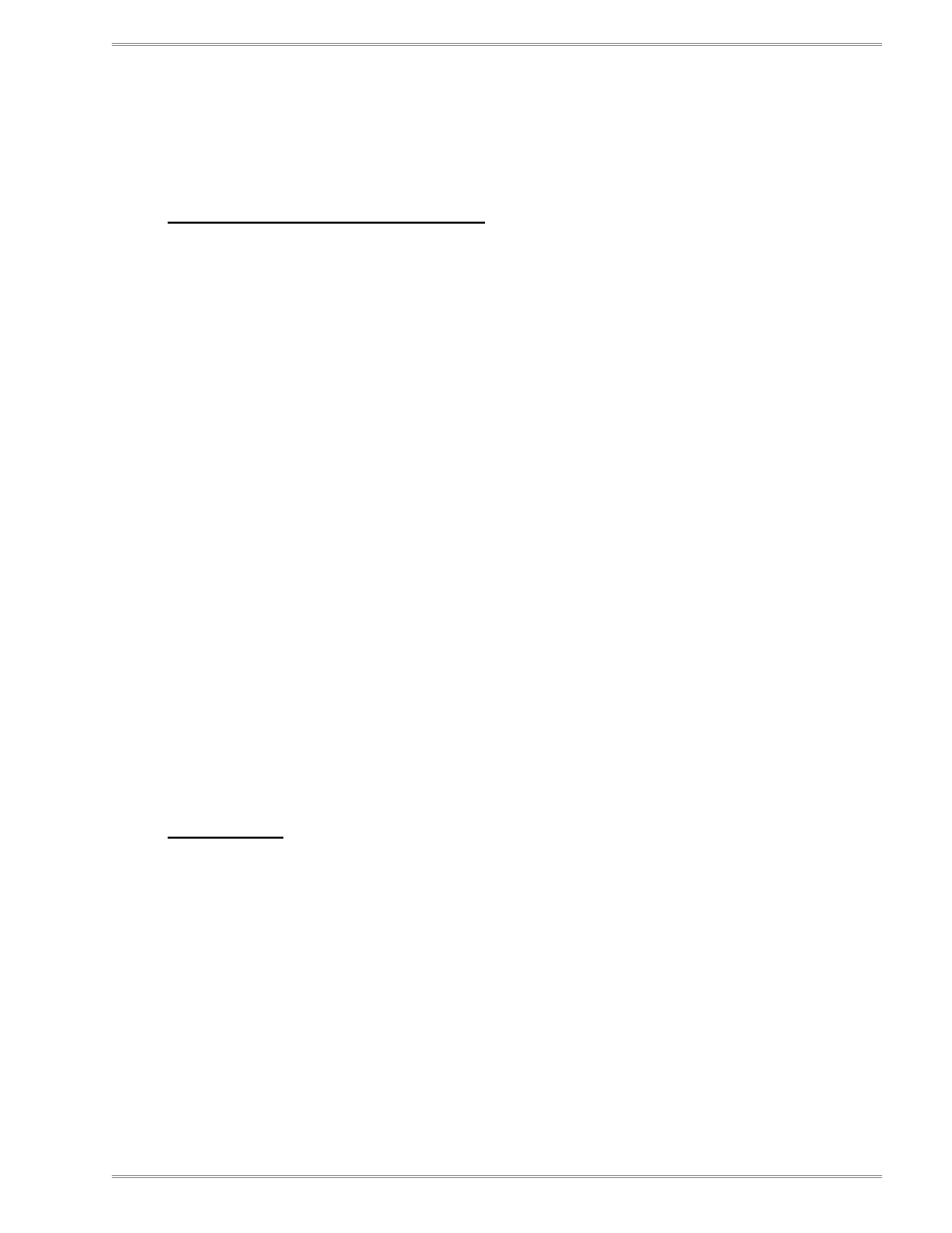
UPLS SYSTEM OVERVIEW
UP-XX-XX-XX
MAGNUM VENUS PLASTECH
REV 1.00
APRIL 2010
PAGE 16
5. To purge the air out of the system, attach the two return hoses from the
recirculation gun to two clean 5-gallon buckets. If the system does not include
reciprocation gun, remove mix chamber, ball and springs from gun block and
attach recirculation block and hoses to gun block. The balls and springs are not
used with the ratio block. Turn gun to the on position and slowly increase pump
pressure until air is purged from hose and pump. Turn gun to off position.
6. Units with recirculation gun block only:
Remove the ratio block from the recirculation gun head and the mix head from
the dispensing gun. Install the ratio block and return hoses to the dispense gun.
Make sure that A & B materials are not reversed when attaching ratio block to
dispense gun head. Attach the two return hoses to two 5-gallon buckets and turn
the dispense gun to on position. Increase pump pressure as needed until a
steady stream of material is being dispensed. The first time a ratio check is ran it
is advisable to run through the dispense gun block. This allows for greater back-
pressure at the pumps because of the longer hose set which creates resistance
or back-pressure. When pressure feeding materials and or higher viscosity
materials this may always be the best way to run ratio checks. Future ratio
checks at the recirculation gun block can be ran but if these checks are
inconsistent refer back to checks from the dispense gun block.
7. When running ratio checks it is vary important to have some back-pressure at the
pumps. Typically, 200 to 300 psi or higher is needed. With thicker resins and or
pressure feeding the system, back pressures of 500 to 600 psi or higher is
advisable for ratio checks. Running the pump at a low flow rate may not achieve
enough back-pressure and will require higher flow rates for consistent ratio
checks. Pay special attention to the stream velocity at the pumps top reversal
when one of the materials is fairly thick and or when pressure feeding too one of
the fluid sections (typically this would be the resin side). If the resin stream has a
much greater velocity drop at the top pump reversal compared to the hardener
fluid stream, higher fluid pressures may be required. Increase pump air pressure
as needed. (Pressure feed systems may need to be increased or decreased to
smooth or diminish the velocity drop. When pressure feeding, the pump up-
stroke normally will be faster then the pump down stroke).
8. Setting ratios:
Loosen the two hex bolts on the top and bottom slide box’s (screw linkage lock
down plates). Use the round handle for the screw adjustment to position the
adjustable fluid section into place. Lightly tighten the upper and lower lock-down
plates hex bolts. Turn gun to on position, turn pump regulator until reaching fluid
pressures described above. Have two 5-gallon containers ready with container
weight logged. Once pressures are met with a steady flow of material, transfer
material hoses to the two containers simultaneously. Turn gun to off position.
Make additional adjustments to the adjustable linkage drive to meet the desired
ratio. Once ratio has been achieved, firmly tighten the upper and lower hex bolts
lockdown plates on the slide box. Please note fluid pressures, temperature and
ratio settings used in ratio check procedure for future reference.