Chapter 3-materials information – Magnum Venus Plastech UNIVERSAL PROPORTIONER User Manual
Page 11
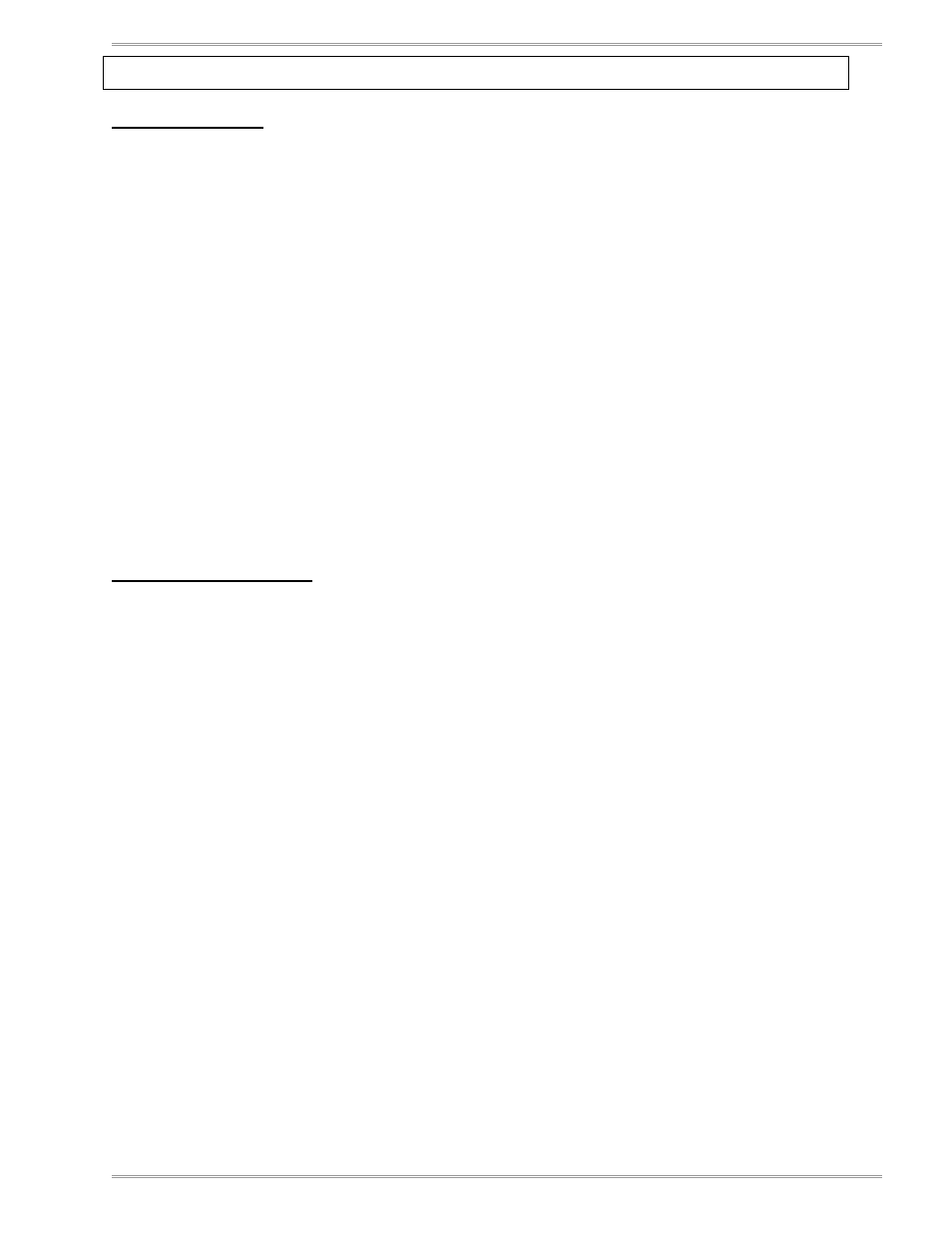
UPLS SYSTEM OVERVIEW
UP-XX-XX-XX
MAGNUM VENUS PLASTECH
REV 1.00
APRIL 2010
PAGE 11
CHAPTER 3-Materials Information
MATERIAL FEED
Depending on fluid sections used, the viscosity and flow rates required will dictate the
type of feed system required. The Universal Proportioner has no standard feed system
in the base unit system and the recommended configuration is determined during the
material qualifying stage before quotation. The material feed options, containers,
transfer (pressure feed) pumps and hose with connectors will vary depending customer
application and requirements.
These include”
1. Pick-up wand assemblies, for lower viscosity and lower flow rates.
2. Gravity feed, for medium viscosity materials depending on flow rates. MVP
options include a wide range of Polyethylene bottom outlet containers. In some
cases, the material manufacture containers can be set-up on drum cradles.
3. Pressure feed, for high viscosity and high flow rates. When pressure feeding to a
ball check pump, the outlet pressure needs to be 8 to 10 times greater then the
inlet pressure. With higher viscosity materials, it may require higher outlet
pressures for proper metering. Please consult with your MVP representative to
assure best performance.
MATERIAL HANDLING
The most common materials used in the Universal Proportioner are Epoxy and
Urethane resin systems. These materials need to be protected from the environment or
they may be affected resulting in improper cure and or possibly effect the performance
of the equipment. A vary common approach with Urethanes is to use a dry Nitrogen
blanket over the surface of the materials before unit shut-down ending the work shift.
This will minimize water absorption of the A & B materials with the Isocyanate even
more critical in avoiding crystal formation.
Not as commonly known however are the effects associated with Epoxy resins. Many
Epoxy resins have storage and process temperatures that need to be met. At lower
temperatures, solids may start to form in the material. These solids can effect metering
of the equipment resulting in off ratio dispensing. The solids will go back into
suspension when heated to a certain temperature depending on the materials.
Many Epoxy amine hardeners are also subject to contamination by moisture and
Carbon dioxide. Most often, this is referred to as surface blushing or sweating which is
oily appearance in area’s of a cured laminate. With some amines, the absorption of
moisture and Carbon dioxide may result in whitish solids at the surface of the
containers. Again, depending on how severe this condition become may affect the
performance of the equipment metering. Almost all data sheets will only call out to keep
containers tightly sealed after use. This is not always a practical solution in a
production environment. As with Urethane resins, a dry Nitrogen blanket over the
surface of the materials is strongly recommended.