Chapter 5-system installation – Magnum Venus Plastech UNIVERSAL PROPORTIONER User Manual
Page 15
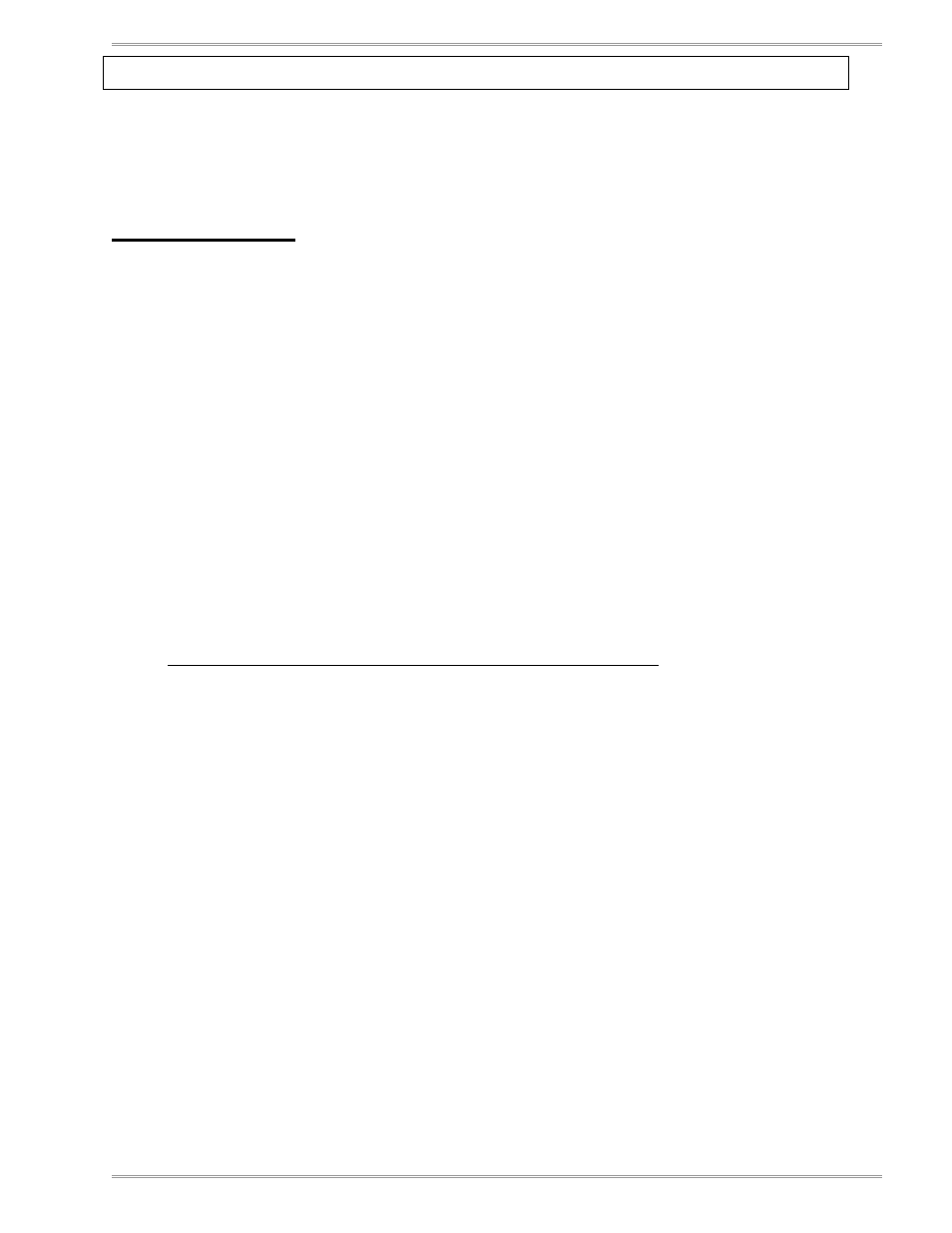
UPLS SYSTEM OVERVIEW
UP-XX-XX-XX
MAGNUM VENUS PLASTECH
REV 1.00
APRIL 2010
PAGE 15
CHAPTER 5-System Installation
Installation time is agreed upon in final quotation. Any additional time requested will be
at a charge. The customer is responsible to have all materials, tools and employees to
be trained ready upon MVP representative’s arrival.
SYSTEM START-UP:
Inspect system for any shipping damage. Check all air and fluid hose connections and
tighten as needed.
Always wear safety glasses around pressurized equipment.
1. Connect air supply to air manifold and open the inlet air ball valve. Tighten the
gun valve rod packing nuts on both dispense and recirculation gun blocks. Turn
on and off quickly 10 to 15 times to assure gun block seals are seated (see gun
manual if needed). Turn one of the two gun blocks to on position and slowly turn
pump regulator up until the pump begins to cycle. Check for any air leaks and
turn gun to off position.
2. Pour supplied throat seal oil into the pump packing nut reservoir half to two-thirds
full. Lightly tighten the pump packing nuts. A hex wrench (Allen wrench)
inserted into the holes of the packing nut works well. Do not over tighten, this
may create friction affecting a smooth cycle rate and reduce packing life.
3. If system includes high pressure flush system disregard #3)
Check that the flush tank regulator is at zero. Lift the flush tank relief valve
(round ring on top of lid) up and lock in open position. Remove the tank lid and
fill container no more then 2/3 full. Avoid splashing solvent on lid o-ring. Install
lid back onto tank and position relief valve stem in down position. Set flush tank
pressure at 40 psi. Turn 3-way ball valve located on hose set close to the
dispensing gun toward the yellow hose. Push one of the two flush buttons on the
side of the gun block with gun block over a bucket to collect solvent. Once a
clean solvent stream appears, stop and then push the second flush valve. Go to
air manifold and set the air purge regulator to around 20 psi. Position the 3-way
ball valve handle pointing to the clear hose which is the flush air purge. Push
both flush valve buttons on gun block. Always position the 3-way ball valve back
to the neutral position after flush/air purge is complete. Once resin system is run
through the mixers, higher flush and air purge pressures may be needed. Do not
exceed more then 70 psi on ether air purge or solvent regulators.
4. Supply materials A & B to the equipment using pick-up wand and hose, gravity
feed container and or pressure feed system. If using pressure feed pumps, use
minimal air pressure to start running the pumps. Further adjustments will be
needed once system is primed and flow rates set.