Liquid Controls HAZARDS PRECISION TURBINE FLOWMETERS User Manual
Page 9
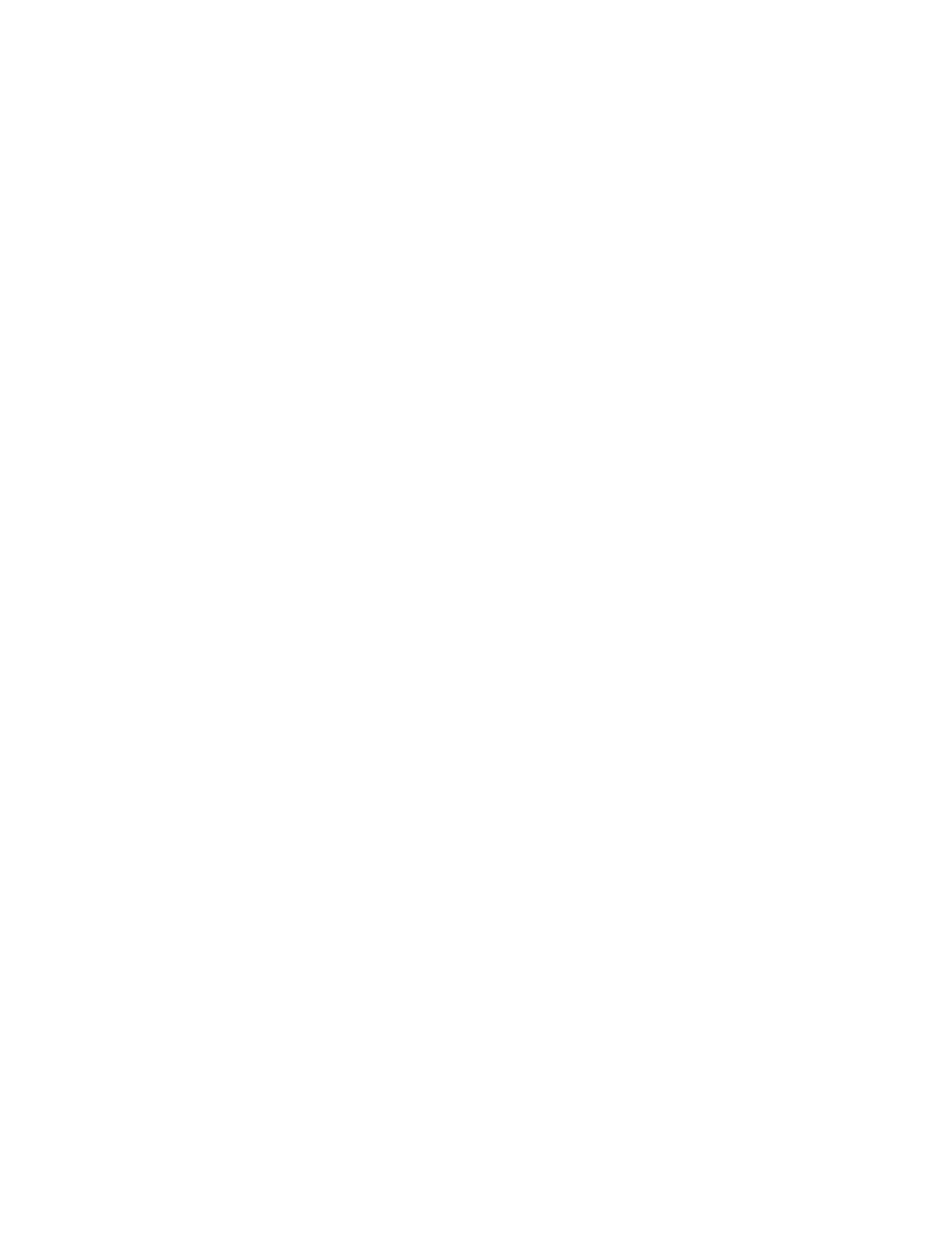
9
MAINTENANCE
Keeping accurate maintenance records can be an excellent tool in determining whether the frequency
of inspection/testing is appropriate for a system. There are always hazards associated with maintenance,
inspection and testing. As such, the involved personnel must be fully trained, take all necessary
precautions, and comply with all local and national legislative requirements.
The customer, owner, operator or partner (whomever performs or contracts to perform the work) is
responsible for the safety if personnel, equipment and the environment before, during and after the
maintenance, inspection or testing.
Prevent pipe strain or stress from occuring when making meter or accessory repairs. Pipe strain and
stress occurs when the pipes are not supported or are not aligned correctly to the Sponsler components.
The weight if the pipes must always be supported independent if the Sponsler components. This means
that the meter and accessories can easily be removed without affecting the pipes or the pipe alignment.
Never leave any of the pipes hanging.
Check with regulatory agency that governs Weights & Measures in your area. Removing or changing
any portion of the Sponsler component may require Weights & Measures recalibration.
Do not mar or scratch any of the precision machine surfaces by prying or sanding parts.
When removing flanges with gaskets, carefully scrap off the flange gaskets. Make sure that the flange
surfaces have been cleaned. Discard the old flange gasket and install a new flange gasket. Never reuse
old flange gaskets.
In service inspection and testing of the meter and accessories is required. Recommended levels of
maintenance and inspection will vary depending on the fluids being metered. General inspection should
be conducted annually at a minimum. This inspection should include an evaluation of the integrity of all
pressure containing and safety related components and seals as well as the component mounting and
integrity the piping. In addition, a hydrostatic testing must be conducted at least once every 5 years at 1.5
times the pressure marked on the unit tag. If using a fluid other than water for the hydro test, it is the end
users responsibility to evaluate the suitability of the liquid with regard to safety of personnel, safety of
compression, material compatibility, weight and density consideration, venting, draining, and disposal.
Even with water. The material compatibility should be considered with all parts in the system as well as
with the final product.
Adjustments
Refer to the product Installation & Operation Manual for instructions on proper adjustments.