2 roll balance, 3 critical roll speed, 4 avoiding damage to the transducer – Cleveland Motion Controls ULTRA ISC CANTILEVER TRANSDUCER CLTSCM REV AA User Manual
Page 28
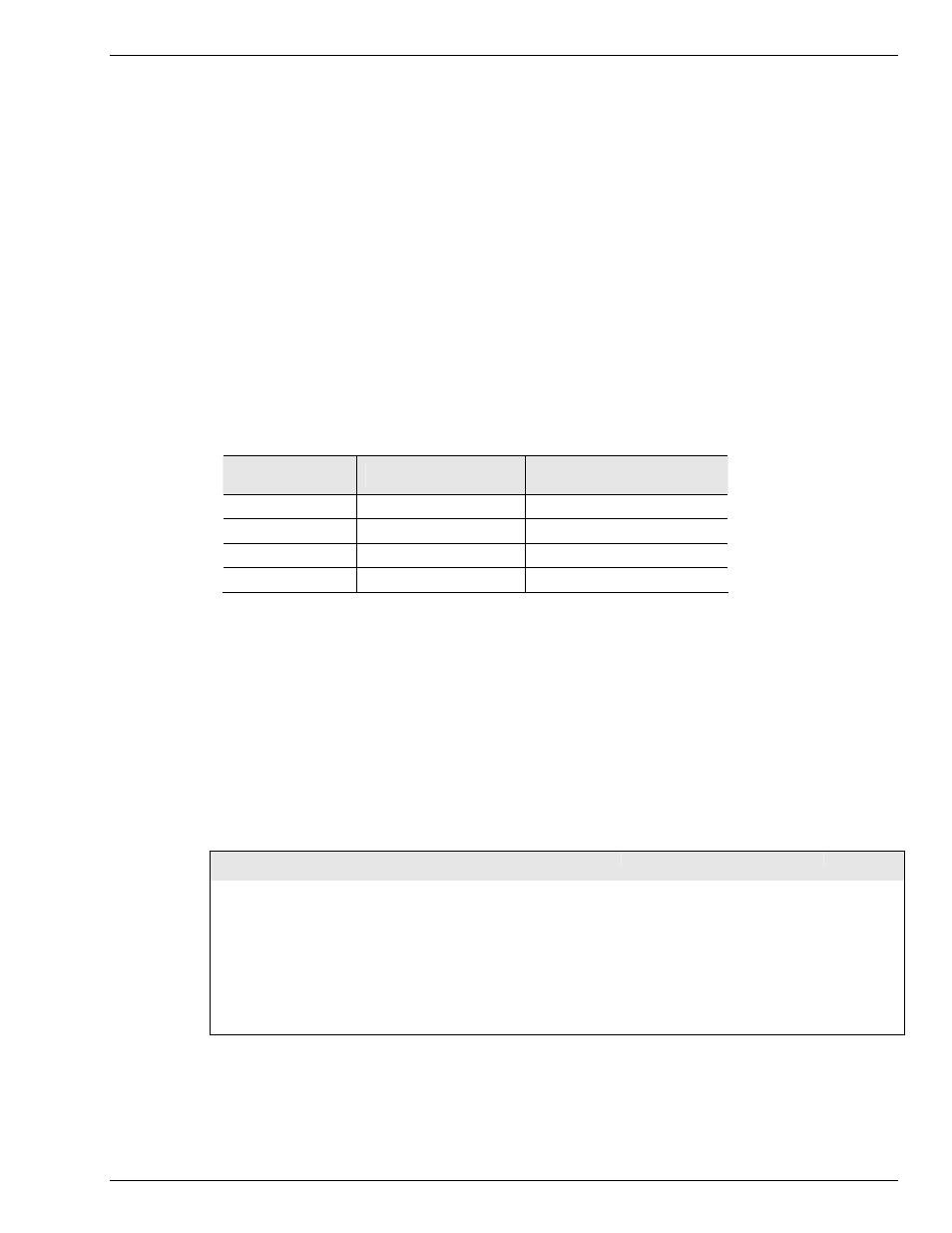
U
LTRA
S
ERIES
ISC
C
ANTILEVER
T
RANSDUCER
T
ECHNICAL
M
ANUAL
MAN-70445-0
R
EV
AA
4.3.2R
OLL
B
ALANCE
The sensing roll must be adequately balanced. Understand that the balance of the sensing roll will be more
demanding than that typically needed in general rotating machinery. The goal goes beyond just limiting the
force to which bearings will be subjected, but rather to minimize the generation of an unintended noise
component in the transducer tension signal. The centrifugal force caused by imbalance can be estimated
using the following formula:
F = (1.77 x 10
-6
) x W x R x (RPM)
2
Where:
F = centrifugal force (in units of lb-f)
W = weight imbalance (in units of ounces)
R = radius of displacement, distance of imbalance weight from roll axis of rotation (in inches)
RPM = Revolution per minute
The force increase is equal to the square of the RPM, or in other words, doubling the RPM causes four
times the imbalance force. If the roll has a high length-to-diameter ratio, two-plane (dynamic) balancing is
recommended. Balancing is particularly needed where higher RPMs and lower web forces are involved.
To illustrate how much imbalance induced “noise” could be generated, the following table shows the force
disturbance for various ISO balance grades for an illustrative case of a 10 pound roll rotating at 2000 RPM.
Balance Grade
(ISO 1940/1)
Residual Imbalance
Resultant Force due to
Residual Imbalance
G16
1.25 oz-in
+/- 9 lb-f at 33 Hz
G6.3
0.5 oz-in
+/- 3.5 lb-f at 33 Hz
G2.5
0.2 oz-in
+/- 1.4 lb-f at 33 Hz
G1
0.08 oz-in
+/- 0.6 lb-f at 33 Hz
4.3.3C
RITICAL
R
OLL
S
PEED
Even with a balanced roll, a vibration can be set up in a stationary shaft. If this vibration (in cycles per
minute) occurs at the harmonic frequency of the shaft, the transducers can be damaged.)
Rotating equipment should never be designed to be operated near critical speeds that risk exciting natural
modes of oscillation. Keep in mind that there can be multiple modes, and various components can each
have an individual set of natural resonant frequencies.
Aside from the critical speed of the roll itself, the basic mass of the roll assembly and the “stiffness” of the
transducer beam interact to exhibit a fundamental frequency.
The columns “Roll Weight” and “RPM with Margin” provide illustration of typical limits for roll mass and
roll RPM for each of the major transducer ratings.
Transducer
MWFs
Stiffness ( lb/in)
Roll weight
Hz
RPM
RPM w margin
Ratio
5
8.33E+02
5
40.4 2422
1800
0.743161
10
1.67E+03
10
40.4 2422
1800
0.743161
25
4.17E+03
15
52.1 3127
2400
0.767533
50
8.33E+03
30
52.1 3127
2400
0.767533
100
1.67E+04
40
63.8 3830
2800
0.731136
100
1.67E+04
50
57.1 3425
2600
0.759047
250
4.17E+04
60
82.4 4944
3600
0.728146
500
8.33E+04
100
90.3 5416
3900
0.720095
4.3.4A
VOIDING
D
AMAGE
T
O THE
T
RANSDUCER
To avoid damaging the transducers, refrain from repetitive overloading above the maximum working force
or severe overloading.
20