3 pre-installation precautions, Nstallation, Recautions – Cleveland Motion Controls ULTRA ISC CANTILEVER TRANSDUCER CLTSCM REV AA User Manual
Page 27
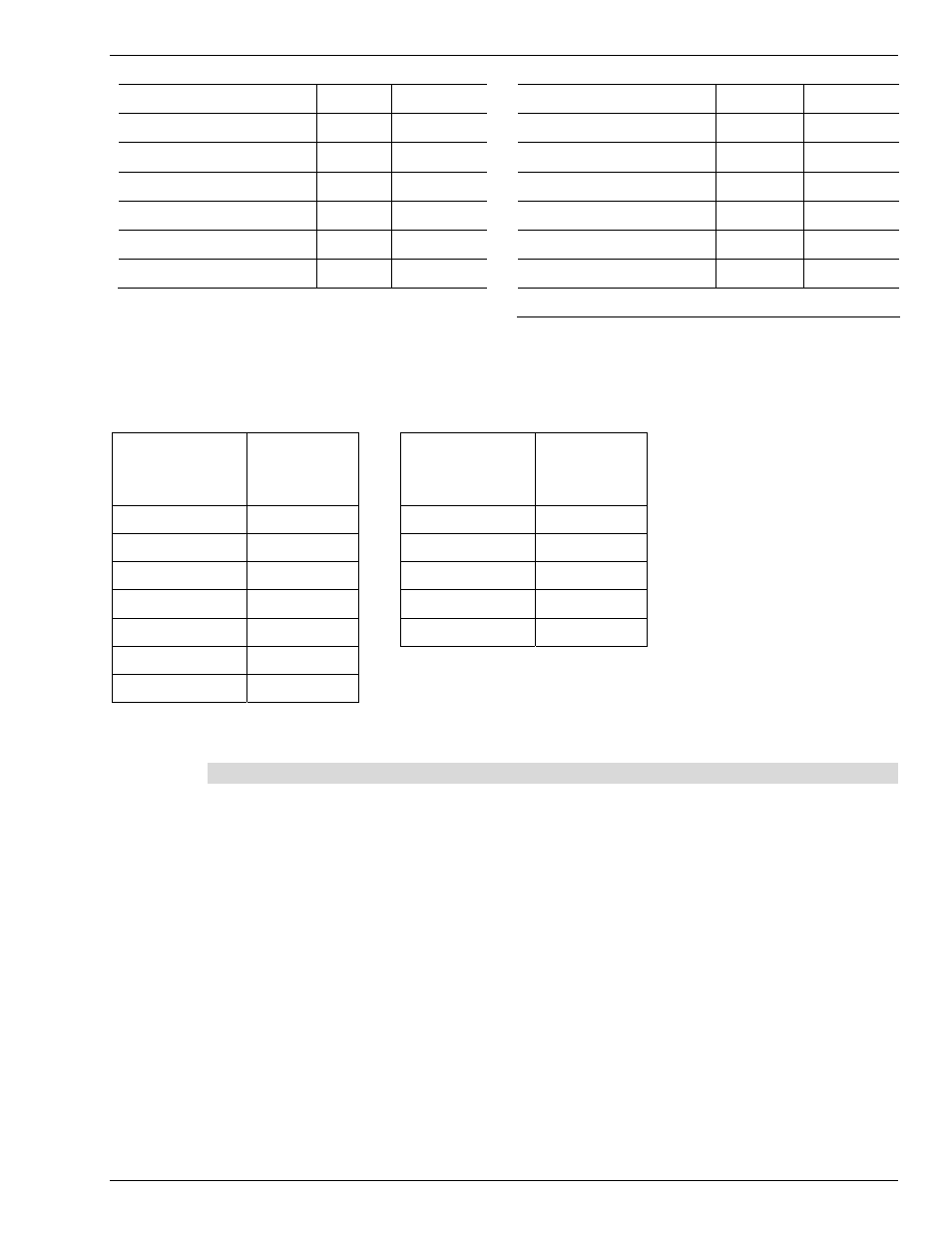
MAN-70445-0
R
EV
AA
U
LTRA
S
ERIES
ISC
C
ANTILEVER
T
RANSDUCER
T
ECHNICAL
M
ANUAL
T
0.58 0.68
U
1.63 1.94
V
1.70 1.02
W
1.75 1.88
X
- -
Y
1/2 1/2
Z (Radius)
1.50 1.70
T
14.7 17.3
U
41.3 49.2
V
25.9 25.9
W
44.5 47.7
X
- -
Y
M-12 M12
Z
38.1 43.2
*Maximum shaft
mm
diameter 30.00
Figure 11 – Mounting Dimensions
ID Recommendations for Cantilever Adapters for Inch or Metric Shaft Diameters
For Shaft
Diameter
(in.)
Cantilever
Adaptor ID
(in.)
½ .5005-.5015
5/8 .6255-.6266
¾ .7506-.7517
1 1.0007-1.0020
1.125 1.1257-1.1271
1.25 1.2508-1.2522
1.5
Table F
For Shaft
Diameter
(mm.)
Cantilever
Adaptor ID
(in.)
17 .6699-.6709
20 .7880-.7890
25 .9848-.9859
30 1.1818-1.1830
35 1.3788-1.3800
Table G
4.3 P
RE
-I
NSTALLATION
P
RECAUTIONS
4.3.1
R
OLL
L
ENGTH
,
M
ASS
,
B
ALANCE
,
N
ATURAL
F
REQUENCY AND
T
RACKING
The cantilever transducer is ideally suited for narrow web applications. Roll length should generally
be limited to 20 Inches. Because the roll is supported only at the transducer end, some inevitable deflection
and loss of perpendicularity can occur. For this reason, rolls should be limited in length and mass so as not
to unnecessarily increase the transducer moment.
Also keep in mind that the beam assembly internal to the transducer affords a particular mechanical
“stiffness” which interacts with a roll’s mass to cause a natural resonant frequency. If the roll spins near the
point of resonance, a destructive un-damped vibration can occur. For this reason, it is always advisable to
check for this possibility, and either decrease the roll mass (by specifying aluminum or composite rolls),
decrease roll RPM (by avoiding small diameter rolls) or by using a higher MWF transducer (affording
higher “stiffness”). At higher RPMs, roll balance becomes increasingly important (refer to Section 4.3.2 for
a discussion).
Web tracking can be adversely affected when the roll “pitches” because of poor transducer mounting,
excessive shaft to transducer bore clearance or shaft bending. It is advisable to consider these issues when
specifying transducer-mounting arrangements, roll shaft diameters and roll mounting techniques.
19