Burkert Type 8056 User Manual
Page 33
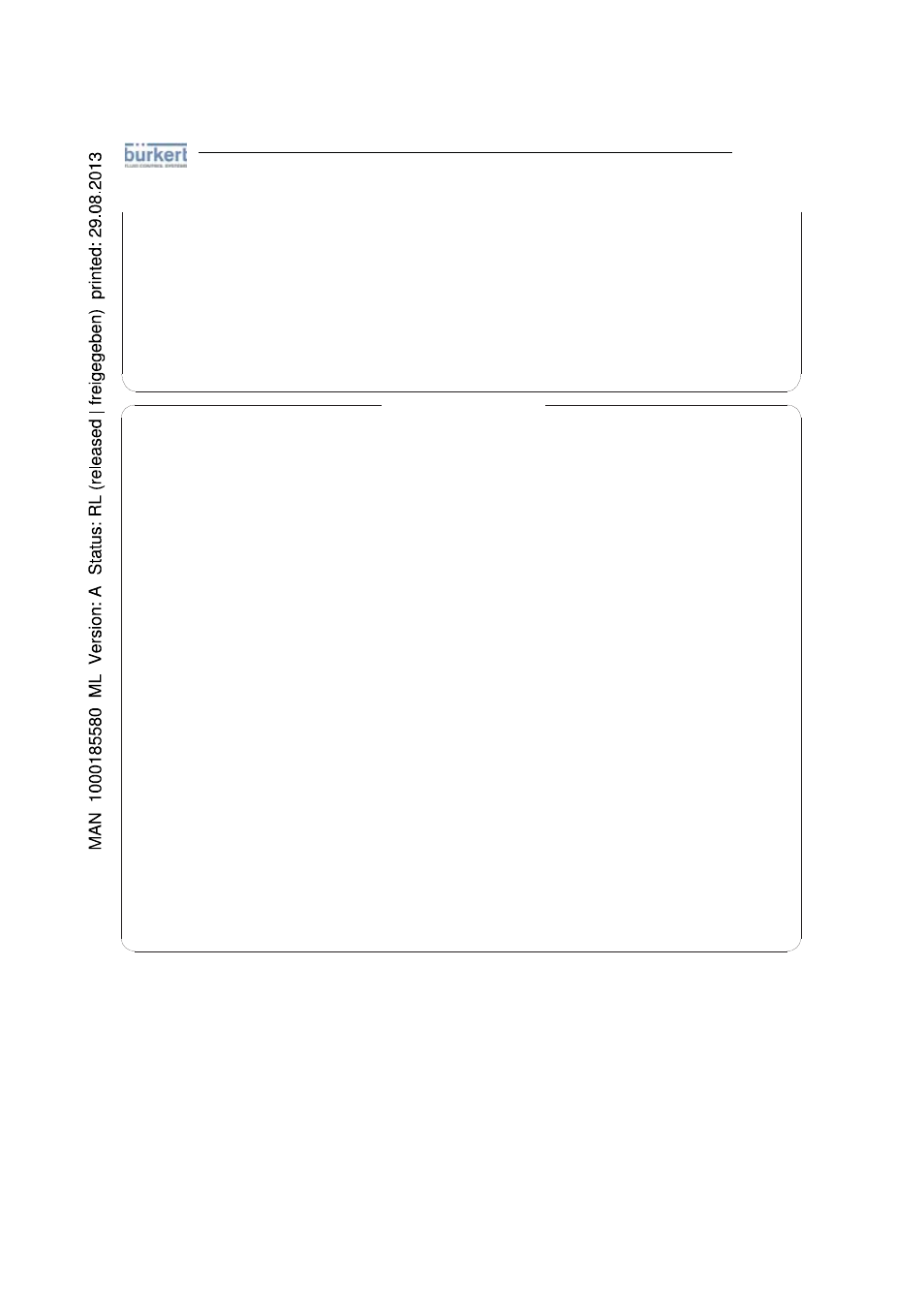
SE 56
33
(POS. 3.5) Automatic scale change enable
[Autorange=ON/OFF]
Enables the automatic change of scale. The meter may have two different working ranges in order to
suit to the variable process conditions. In order to get the best results out of this function it is
important range N.2 (Fs2) if enabled is bigger than N.1 (Fs1). When the flow rate increases and
reaches the 100% of the full scale 1, then the meter automatically switches to scale 2. When the flow
rate decreases again reaching a value on scale 2 equal to the 90% of full scale N.1, then the active
scale is 1 again. Allowed values for this parameter: ON/OFF. Note: the autorange does not allow
using the manual change of range (pos. 5.8)
MENU 4 - ALARMS
(POS. 4.6) Current output value in case of failure
[mA V.fault =% XXX]
The output current signal can be specified by the user in case of failure of either, empty pipe, coils
interrupted, or ADC error. The signal current is set as a percentage (0 to 120%) of the 0/4-20mA
current. 120% corresponds to 24mA and does not depend on the selected range (0-20/4-20mA).
The NAMUR NE43 recommendation asks for a alarms signalling value for the current output lower
than 3.6mA (<18%) or bigger than 21mA (>105%). It would then be preferable to set the value of
this function at the 10%, so that the current value in case of the a.m. cases would be 2 mA, allowing
the following diagnostics:
current < 2mA - 5%: line interrupted, power supply failure or faulty transmitter;
2mA -5% d current d 2mA + 5%: hardware alarm;
4mA d current d 20mA: normal working range;
20mA < current d 22mA: out of range, measure above 100% f.s.
Note: To set this parameter to zero disables the alarm
(POS. 4.7) Frequency output value in case of failure
[Hz V.fault=%XXX]
To set the frequency value assigned to the on/off output in one or more of the following failure cases:
Empty pipe; Coils interrupted; ADC error
Allowable range is from 0 to 125% of the frequency full scale value.
Although there are no specific rules regulating cases such as these, it would be convenient to use the
failure information as follows:
0% Hz d frequency d 100% f.s.: normal working range;
100% f.s. < frequency d 110% f.s.: overflow, measure above the 100% of the f.s.;
115% f.s. d frequency d 125% f.s.: hardware alarm condition.
(POS. 4.8) Batch safety timer
[Timeout =s XX.X]
With this function is possible to set a maximum time for the batch ; over this time will be generate
an alarm.
This function is useful when you need control one or both of the following conditions:
batch valve open and flow rate is zero
batch valve closed and flow rate different to zero
When this alarm is activate, the batch operation and power supply to the value is halted. The allowed
values of function are from 0 (disable) to 25.5 seconds and is active only if one or more of the batch
functions are enabled.