DE-STA-CO Output Overload Clutches Type F, FC, S, C, D, FC-SD, C-SD User Manual
Page 8
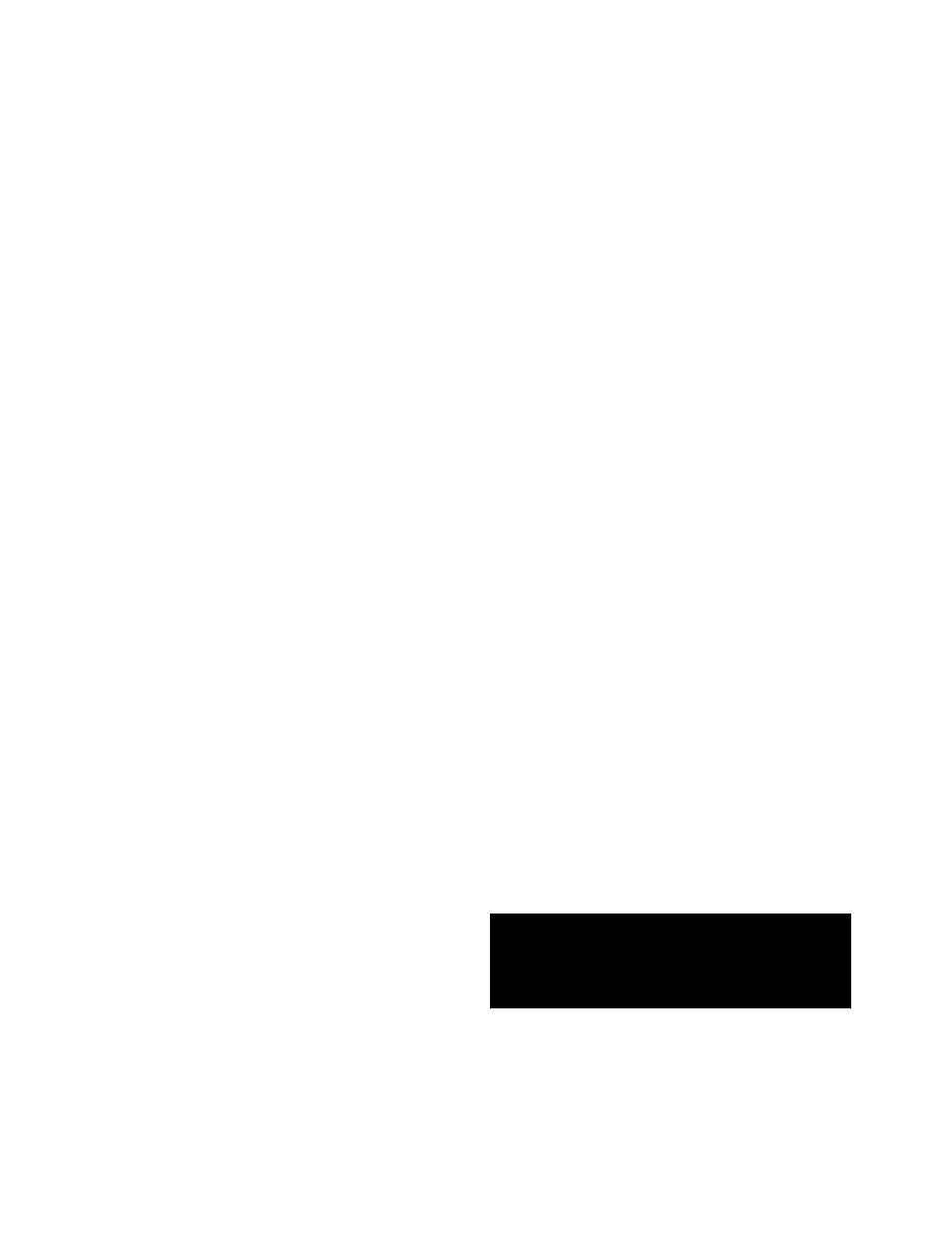
12. Disassemble, deburr and clean all parts.
Remove .010" shim stock.13.
Dowel pin
the DRIVE PLATE to the DIAL PLATE.
Note: Dowel pins are factory installed when
the CLUTCH and DIAL PLATE are supplied
with the INDEX DRIVE.
Warning: Dowels pins must not protrude from
the DRIVE PLATE or DIAL PLATE as they may
lock against the adjacent surtace, making the
clutch inoperative.
14. LIGHTLY lubricate the DRIVE PLATE and
mating surtace of the clutch BODY with
Mobilgrease 77 or equivalent.
15. Assemble complete clutch. Alternately tighten
body mounting screws following the proce-
dures in instruction #10.
16. Assemble the DETECTOR PLATE ➊ on the
clutch BODY and secure both the DETECTOR
PLATE and the PLUNGERS with the detector
mounting screws.
17. Check it DIAL PLATE can be disengaged.
18. Test tor proper torque setting. The clutch
should disengage within 10% to the name-
plate torque rating.
Note: All clutches are torque tested by
CAMCO prior to shipment.
DISASSEMBLY INSTRUCTIONS (TYPE D)
1. Remove DETECTOR MOUNTING screws
which will release the PLUNGER assemblies.
2. Alternately loosen and remove the BODY
mounting screws.
Warning: The plunger assemblies are spring
loaded and under tension. Bodily injury could
result if the plunger assemblies are not re-
leased slowly by the body mounting screws.
3. Remove the clutch BODY.
Note: It may be necessary to tap under the
DIAL PLATE to overcome the friction caused
by the dowel pins that register the body to the
mounting flange.
4. Clean and inspect all parts tor wear.
5. Lubricate per assembly instructions 1, 8,and
14.
WARNING
High humidity, contaminants or wash down
applications may cause rust within the clutch
resulting in operational failure. Lubricate every
six months or more
frequently as the applications
require.
4. Install dowel pins in the INDEX DRIVE
mounting flange to insure proper position-
ing to the clutch BODY.5. Insert BODY
∑
into DRIVE PLATE
∏
and through the
center hole of the DIAL.
Note: Do not assemble SPRINGS, PLUNG-
ERS or DETECTOR PLATE on the BODY.
6. Attach the clutch BODY to the INDEX
DRIVE output mounting flange with the
body mounting screws.
Note: A .002" minimum to .004" maximum
clearance gap must exist between the
DRIVE PLATE and the BODY, around the
full circumference of the clutch.
7. Clearance Procedure (See Fig. 5)
A. Measure dimension "A" (bottom
surface to BODY to bottom
surface
of BODY detent).
B. Measure dimension "B" (top surface
of DRIVE PLATE to top surface of
dutch pilot).
C. Subtract "B" from "A".
D. If less than .002", add shim at surface
"C" (between clutch pilot and
bottom
surface of BODY)
to obtain clearance
gap of .002" to .004".
E. If greater than .004" grind BODY,
(between DRIVE PLATE and DIAL
PLATE) to obtain clearance gap of
.002" to .004".
8. Remove BODY. Insert PLUNGERS
∫
into
SPRINGS
π
and install the assemblies in
the BODY pockets. Test for free movement
of the plungers. Lightly lubricate the body
pockets, springs and plungers with
Mobilgrease 77 or equivalent.
Caution: Do not overlubricate.
Heavy lubrication may prevent clutch
disengagement.
9. Align the PLUNGERS with tapered seats in
the DRIVE PLATE
∏
. Re-install BODY.
10. Rotate the DIAL PLATE to desired position.
Place .010" shim stock between the BODY
and the DRIVE PLATE and alternately
tighten body mounting screws, clamping
the DIAL PLATE. Shim stock should be
placed at 90
°
intervals.
Caution: Do not cock the plunger.
The plungers must retract evenly into the
clutch body.
11. Using the BODY and DRIVE PLATE as a
"JIG," drill and ream the DIAL PLATE dowel
holes. Theholes should not go completely
through the DIAL PLATE. DIAL PLATE
dowel pins should be .125" shorter than
the combined thickness of the DIAL and
DRIVE PLATES.
8