Bray 92_93 Series FLO User Manual
Page 8
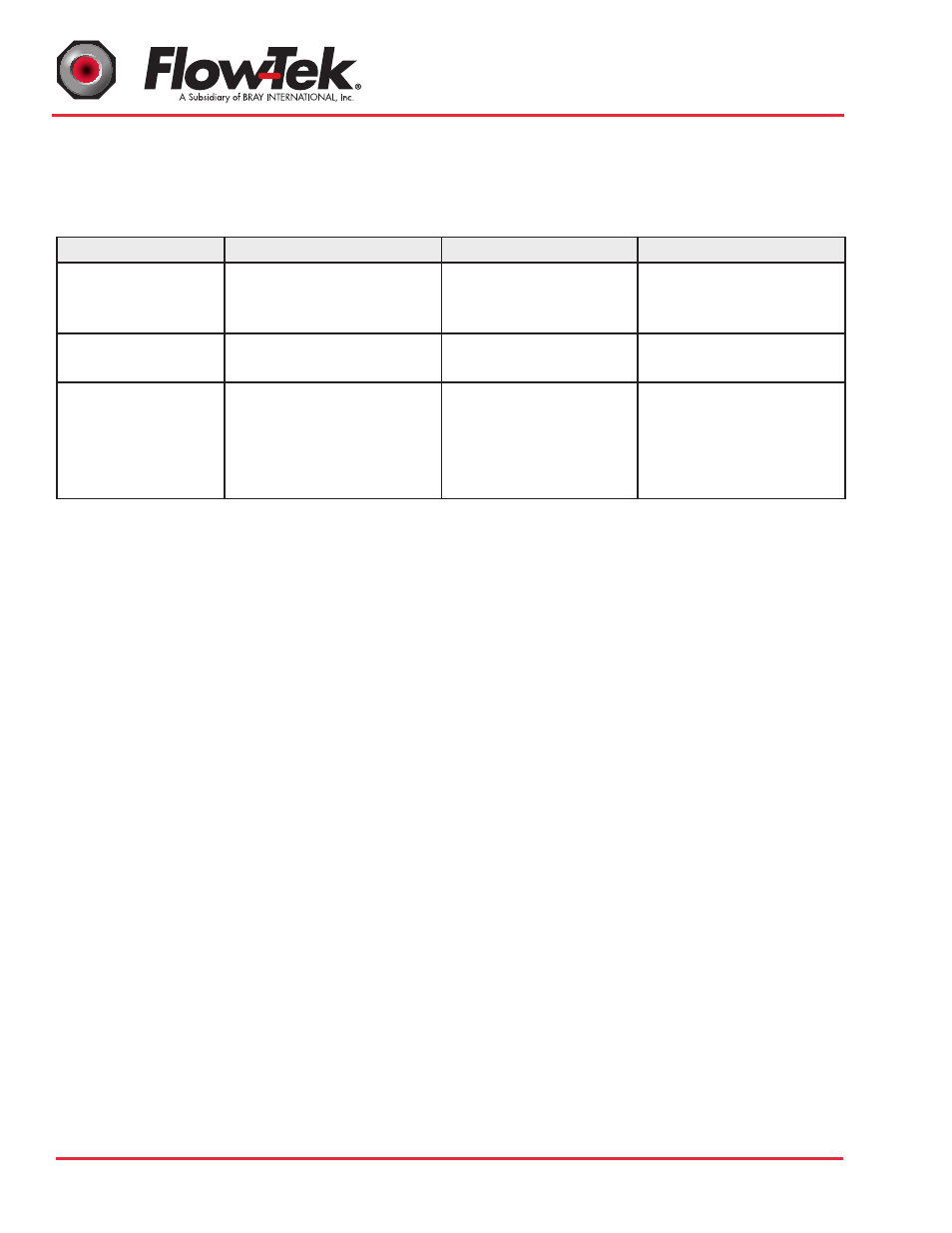
6
All information herein is proprietary and confidential and may not be copied or reproduced without the expressed written consent of BRAY INTERNATIONAL, Inc.
The technical data herein is for general information only. Product suitability should be based solely upon customer’s detailed knowledge and experience with their application.
Series 92-93 Pneumatic Actuator
Operations and Maintenance Instructions
Assembly
To identify component names and shapes, refer
to the Exploded View of the actuator shown on
Figure 4, pg. 11. The numbers in parentheses ( ) refer
to the numbered bubbles in Figure 3. Easiest assem-
bly will result from lubricating all bearings and seals
as they are installed. The lubricant should be a high
pressure or extreme pressure petroleum grease with a
lithium based thickener which meets the NLGI grade
2. Grease which meets this specification should be
available from any automotive supply store.
Pinion (3)
- Install bearing rings (6 & 7) and o-rings
(18 & 19) in their appropriate grooves. Insert the
pinion through the large hole in the center of the
body (1). With the pinion part of the way into the
body, slide the cam (23) over the pinion being careful
to align the punch mark on the cam with the punch
mark(s) on the pinion. For normal installation and
rotation (Fail Close), align the single marks. For
Fail Open operation described in Method 2 above,
align the single mark on the cam with the two marks
on the pinion. For Fail Open operation described in
Method 3 above, align the single marks. Next, install
the spacer (24) above the cam. Then insert the pinion
through the hole at the top of the body and secure it
with the washer (9) and retaining ring (8).
Travel Stop Screws (13)
- Slip the o-ring (14) over
the flat end of the screw until it is 5-7 threads from
the end. Thread the screw into the hole in the body,
flat end first. Repeat these steps for the second
screw. Thread the lock nuts (12) onto the screws
and tighten the nuts against the body. This will seal
the threads for testing. It is not necessary to set the
travel stops at this time, as they may have to be reset
when the actuator is installed on the valve.
Pistons (2)
- Install the bearing pad (10) on the
back of the rack and the o-ring (16) and guide ring
(11) in their appropriate piston grooves. The o-ring
goes in the groove nearest the rack. With the ports
on the actuator body toward you, turn the pinion
so that the slot is approximately 45° to the right of
perpendicular with the long side of the body. Grasp
the pistons in the spring pockets so that the piston
in the right hand has the bearing pad toward you
and the piston in the left hand has the bearing pad
away from you. Slide the pistons into the body so
that they both engage the teeth on the pinion at the
same time. Apply enough steady force to compress
the o-ring into the body bore. At this point, you may
continue pushing or use a wrench on the top of the
pinion to pull the pistons into the body.
Symptom
Probable Cause
Check
Remedy
Loss of Power
Low air supply pressure, or
damaged O-rings
Air supply pressure at
actuator, leakage across
O-rings
Boost air supply pres-
sure, repair air supply line
leaks, replace O-rings
Binding between
valve and actuator
Misalignment of coupling Alignment
Realign coupling
Valve “pops” out of
seat and slams open
Valve torque too high,
actuator sized too small, or
insufficient air supply flow
Valve torque, actuator
sizing calculations, size
of air supply lines and/
or solenoid valve
Repair valve, use proper
size actuator, use larger
air supply lines and/or so-
lenoid valve with higher
flow
Troubleshooting
Table 1 shows several common symptoms and their remedies.