Dynamic torques, Flow, Bray/mccannalok hpbv – dynamic torques – Bray 40_41 User Manual
Page 10: Dynamic torque - terminology
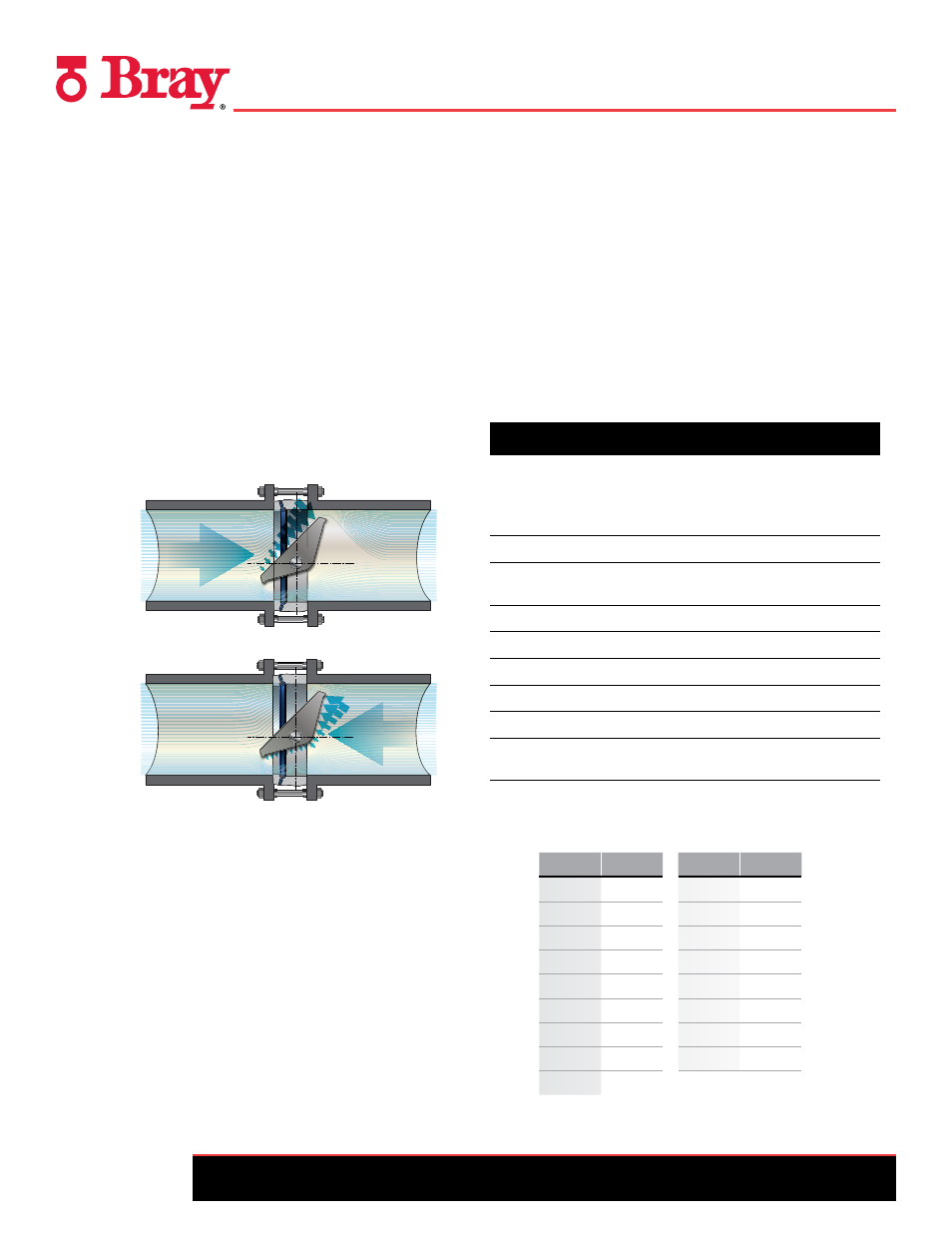
Bray/McCannalok HPBV – Dynamic Torques
All information herein is proprietary and confidential and may not be copied or reproduced without the expressed written consent of BRAY INTERNATIONAL, Inc.
The technical data herein is for general information only. Product suitability should be based solely upon customer’s detailed knowledge and experience with their application.
Dynamic : 10
Dynamic Torques:
When a media flows through a butterfly valve, static pressure
does not act uniformly on the surfaces of the valve disc. Dynamic
torque will cause rotary motion when unchecked by the actuator
or manual operator possibly resulting in opening or closing of the
valve. If the dynamic torque is of a magnitude that is greater than
the bearing and packing friction torque and there is no actuator
in place to maintain disc position, the opening or closing action
could result in injury to operating personnel or an interruption of
the process. Sudden closure (slamming) can cause water hammer
damage in lines carrying liquid.
In high performance butterfly valves which have the disc
offset from the stem and have non-symmetrical disc faces,
dynamic torque acts to close the valve if the valve is installed
with the seat retainer downstream, but can act to close or open
the valve, depending on the position of the disc, if the seat re-
tainer is upstream.
Dynamic torque should be calculated as part of the valve actua-
tor sizing procedure or to determine if hand lever operation is ac-
ceptable. In this regard, the total torque of all service conditions
must be considered.
The total torque when the disc is in the seat consists of:
1. Seating torque
2. Stem packing torque
3. Eccentricity torque
4. Stem bearing torque
The total torque when the disc is in the seat is published as seat-
ing/unseating torque. When the disc is out of the seat, the total
torque consists of dynamic torque, stem packing torque, and stem
bearing torque.
Total torque changes with the disc position. Maximum total
torque can occur at shutoff (disc in the seat), at breakaway (mo-
tion initiation), or at any open disc position where the product
of valve pressure drop and dynamic torque coefficient peaks in
combination with prevailing bearing and packing torque.
Estimating Dynamic Torque
Dynamic torque can be estimated using the following
empirical equations:
Liquid Flow:
Imperial ...... Td (Lb-inches) = Ct D³ p
Metric ......... Td (N-m) = .0001 Ct D³ p
Gas Flow:
Imperial ...... Td (Lb-inches) = Ct D³ Y p
Metric ......... Td (N-m) = .0001 Ct D³ Y p
Dynamic Torque - Terminology
Ct -
dynamic torque coefficient (see graphs and tables on
Pg. 12 for values of Ct.) Positive value of Ct means that
the dynamic torque acts to close the valve and a nega-
tive value of Ct to open the valve.
D -
nominal valve size (inch or mm)
Fk -
ratio of specific heat factor (dimensionless)
Fk = k/1.40 or Fk = 1 for air
k -
ratio of specific heat (dimensionless)
p -
effective pressure drop across the valve (psi or bar)
p1 -
valve inlet pressure (psia or bar abs.)
Td -
dynamic torque (Lb-inches or N-m)
x -
x = p/p1
Y -
gas expansion factor (dimensionless)
Y = 1 – x / (3 Fk xt)
xt -
gas critical pressure ratio (dimensionless)
Values of xt change with disc position and are identi-
cal for seat retainer upstream and downstream.
º Open
xt
º Open
xt
10º
0.46
55°
0.31
15º
0.46
60°
0.28
20º
0.46
65°
0.27
25°
0.45
70°
0.25
30°
0.44
75°
0.24
35°
0.42
80°
0.22
40°
0.39
85°
0.21
45°
0.35
90º
0.19
50°
0.33
Pressure Distribution
FLOW
FLOW
Seat Retainer Upstream
Seat Retainer Downstream