Sf s, Eb n m s – Elmo Rietschle V-VL 10/25/40/80/100 User Manual
Page 7
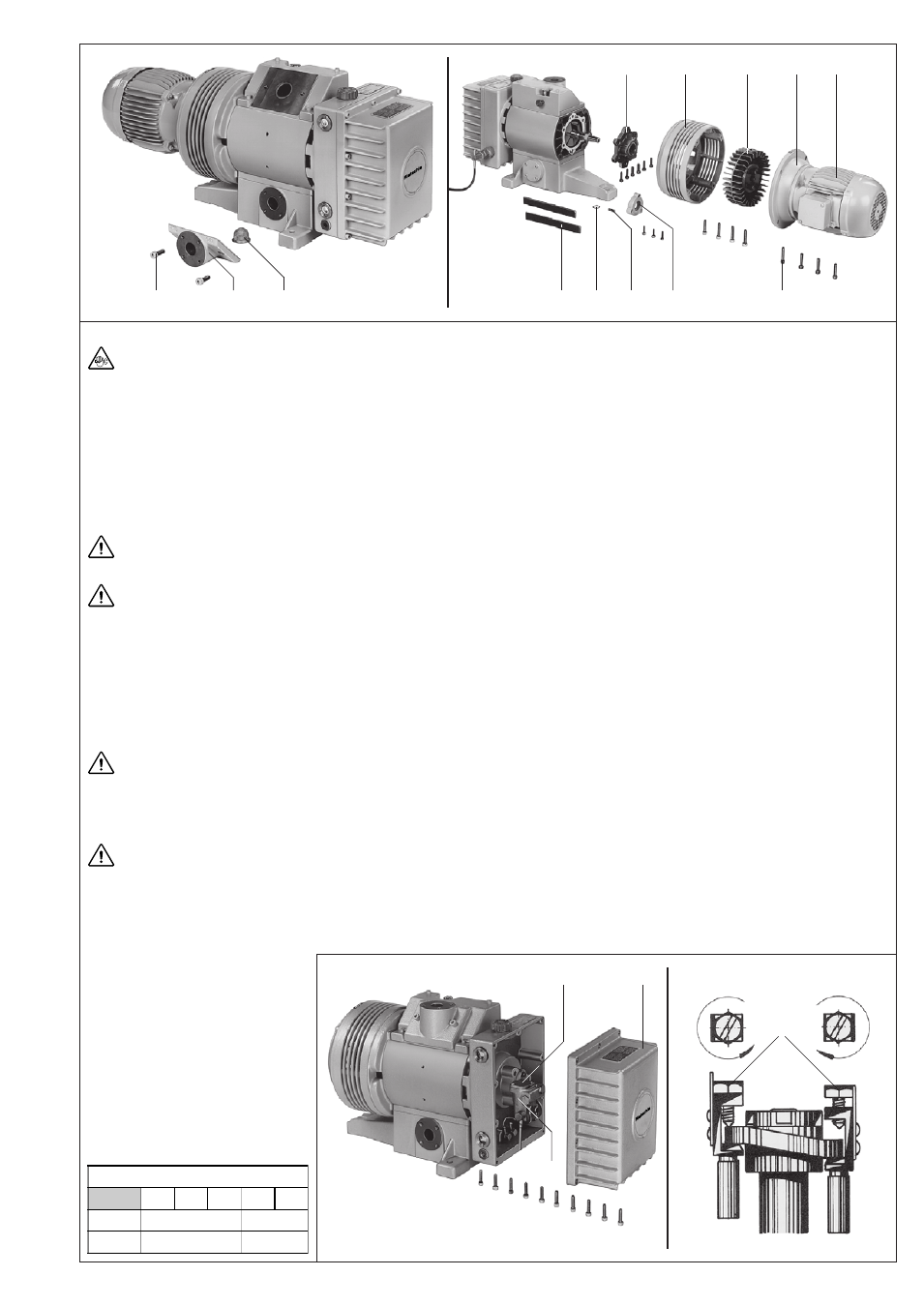
ᕨ
ᕧ
Y
L
1
L
L
2
ᕥ
ᕦ
S
f
s
1
d
l
1
l
2
e
b
n
m
s
5
v
1
v
VL
10
25
40
80
100
50 Hz
0,034
0,069
60 Hz
0,041
0,083
Oil consumption in l/hr
Reduction of oil
Increase of oil
Maintenance and Servicing
When maintaining these units and having such situations where personnel could be hurt by moving parts or by live electrical parts
the pump must be isolated by totally disconnecting the electrical supply. It is imperative that the unit cannot be re-started during
the maintenance operation.
Hazardous substances must be removed before servicing. Maintenance personnel should be informed regarding the presence of
anything harmful and also be informed about all relevant safety regulations before carrying out any work.
1. Lubrication (pictures
ᕡ and ᕢ)
All VL pumps are fresh oil lubricated and therefore the oil level should be checked every 50 operating hours at the oil sight glasses (I). If the oil level
is visible in the lower sight glass, or if it is below this level, then oil should be refilled at the oil filler port (H). It is not necessary to check the oil if
an oil level switch (V) is fitted. A level switch will automatically stop the pump as soon as the minimum level is reached.
The viscosity must correspond to ISO-VG 100 according to DIN 51 519.
We recommend the following oil brands: Bechem VBL 100, BP Energol RC 100, Esso rotary oil 100, Mobil vacuum pump oil heavy, Shell Tellus
oil C 100 and Aral Motanol HK 100 or equivalent oils from other manufacturers (see oil type plate (M)).
If the oil brand is changed, the old oil must be drained completely from the oil tank.
Old and used oil must be disposed of corresponding with the relevant health, safety and environmental laws.
2. Air filtration (picture
ᕥ)
The capacity of the pump can be reduced if the air inlet filters are not maintained correctly.
The mesh filter (f) and additional separators (Z
1
/ Z
2
) must be emptied and cleaned regularly depending upon the amount of contamination or the
filter inserts must be replaced completely.
Unscrew the screws (s
1
). Remove angle flange (S) with gasket. Remove mesh filter (f) and clean by blowing out with compressed air or replace.
Re-assemble in reverse order.
3. Changing blades (pictures
ᕦ and ᕩ)
The blades (6 pieces) can be changed as follows:
Unscrew the screws (s
5
) on the motor flange (n). Pull off the motor (m) together with the motor side coupling half (q). Remove the circlip (l
1
), pull
off the coupling (q
1
) and fan (v) complete from the pumpshaft. Remove the fan cover (v
1
). Remove key (l
2
) out of the key-way. Remove bearing
cover (e) and housing cover (b) with gaskets. Remove the blades (d) and check.
Blades (6 pieces) must be changed completely.
Oil blades slightly before assembly. Blades should move easily in rotor slots.
Re-assemble in reverse order.
4. Oil metering pump (pictures
ᕢ, ᕧ and ᕨ)
The oil metering pump is preset to the required output, at the factory.
This rate can only be changed on request to our Company.
If however it is neccessary to change this rate on request, it can be achieved as follows:
Unscrew oil tank (Y) with gasket (only on the model with built-in oil metering pump). Unscrew oil pump cover (L
1
). The rate can only be changed
by turning the regulating screw (L
2
). Reduce oil counter-clockwise, increase oil clockwise. The capacity will be changed about
1
/
6
per revolution.