N-100-20 8 pgs new_7, Troubleshooting, Three checks – Cla-Val 100-20 600 Series User Manual
Page 3
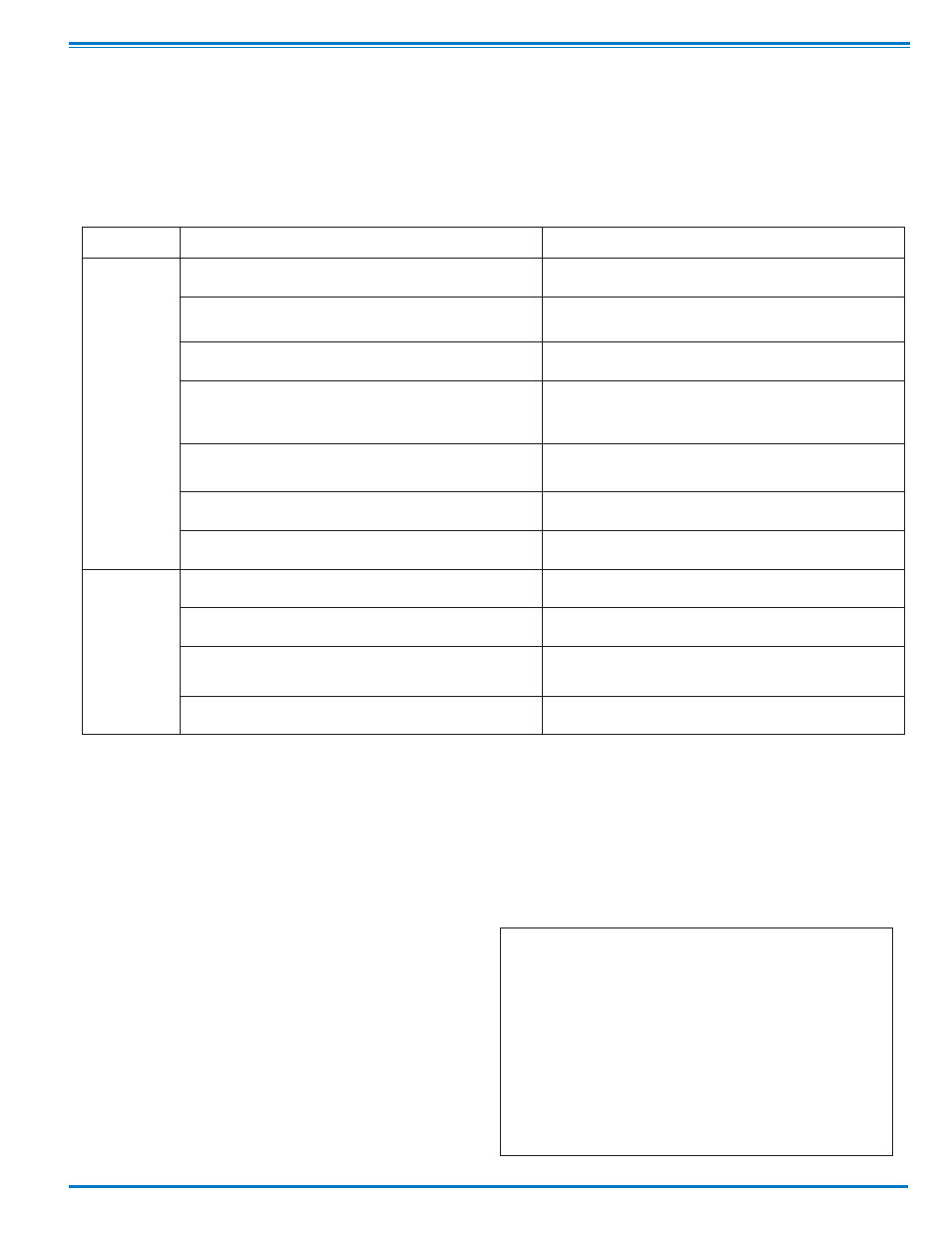
3
Troubleshooting
The following troubleshooting information deals strictly with the
Model 100-20 Hytrol Valve. This assumes that all other compo-
nents of the pilot control system have been checked out and are
in proper working condition. (See appropriate sections in
Technical Manual for complete valve).
Three Checks
The 100-20 Hytrol Valve has only one moving part (the diaphragm
and disc assembly). So, there are only three major types of prob-
lems to be considered.
First: Valve is stuck - that is, the diaphragm assembly is not free
to move through a full stroke either from open to close or vice
versa.
Second: Valve is free to move and can’t close because of a worn
out diaphragm.
Third: Valve leaks even though it is free to move and the
diaphragm isn’t leaking.
After checking out probable causes and remedies, the following three checks can be used to diagnose the nature of the
problem before maintenance is started. They must be done in the order shown.
CAUTION:
Care should be taken when doing the troubleshooting checks on
the 100-20 Hytrol Valve. These checks do require the valve to
open fully. This will either allow a high flow rate through the
valve, or the downstream pressure will quickly increase to the
inlet pressure. In some cases, this can be very harmful. Where
this is the case, and there are no block valves in the system to
protect the downstream piping, it should be realized that the
valve cannot be serviced under pressure. Steps should be
taken to remedy this situation before proceeding any further.
All trouble shooting is possible without removing the valve from the
line or removing the cover. It is highly recommended to permanently
install a Model X101 Valve Position Indicator and three gauges in
unused Hytrol inlet, outlet and cover connections.
SYMPTON
PROBABLE CAUSE
REMEDY
Fails to Close
Closed isolation valves in control system, or in main line.
Open Isolation valves.
Lack of cover chamber pressure.
Check upstream pressure, pilot system, strainer, tubing, valves,
or needle valves for obstruction.
Diaphragm damaged. (See Diaphragm Check.)
Replace diaphragm.
Diaphragm assembly inoperative.
Corrosion or excessive scale build up on valve stem.
(See Freedom of Movement Check)
Clean and polish stem. Inspect and replace any damaged or
badly eroded part.
Mechanical obstruction. Object lodged in valve.
(See Freedom of Movement Check)
Remove obstruction.
Worn disc. (See Tight Sealing Check)
Replace disc.
Badly scored seat. (See Tight Sealing Check)
Replace seat.
Fails to Open
Closed upstream and/or downstream isolation valves in main
line.
Open isolation valves
Insufficient line pressure.
Check upstream pressure. (Minimum 5 psi flowing line
pressure differential.)
Diaphragm assembly inoperative. Corrosion or excessive
buildup on valve stem. (See Freedom of Movement Check)
Clean and polish stem. Inspect and replace any damaged or
badly eroded part.
Diaphragm damaged. (For valves in "reverse flow" only)
Replace diaphragm.