Flow check control, Cla-val – Cla-Val 210-03/610-03 User Manual
Page 33
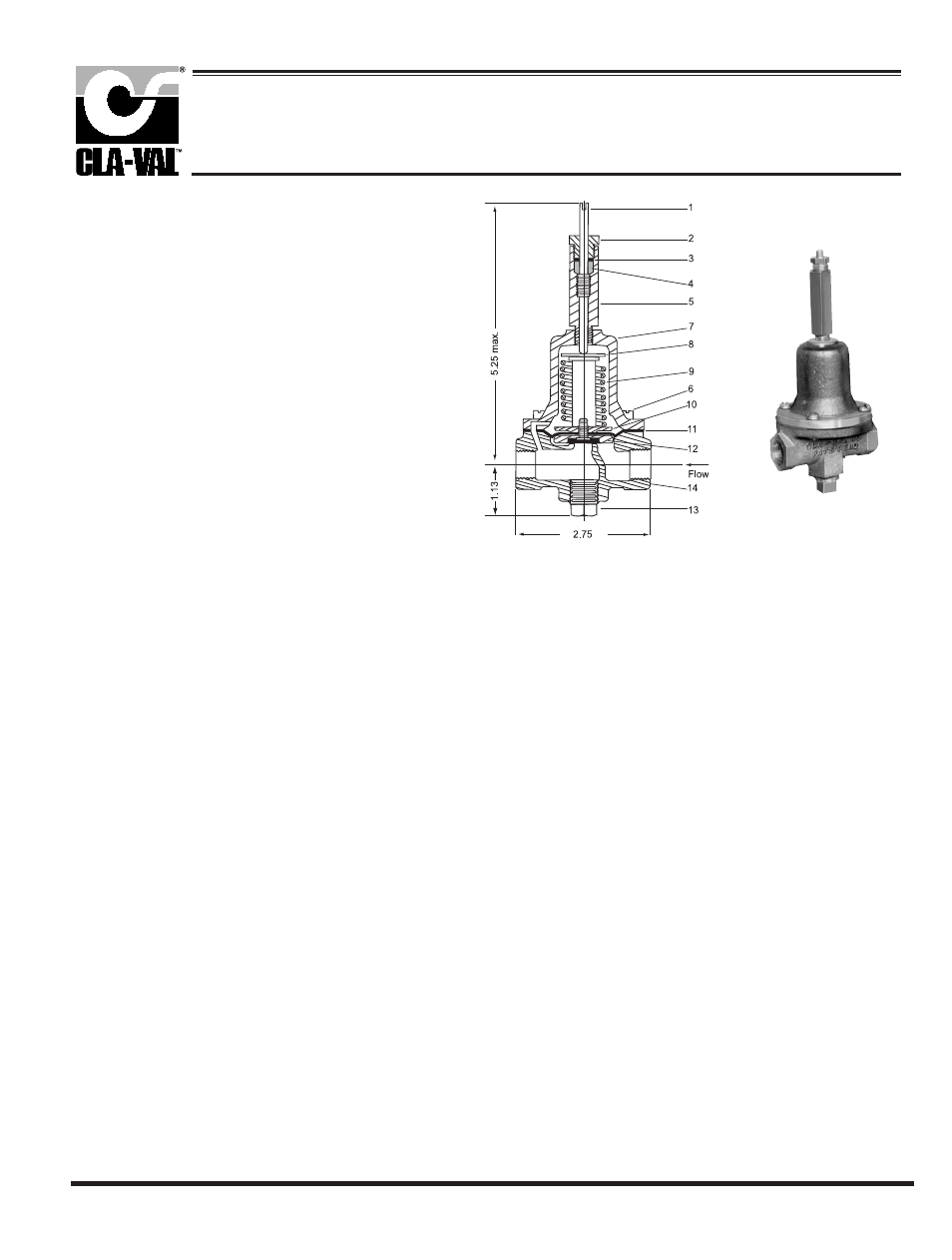
CLA-VAL
Copyright Cla-Val 2009 Printed in USA Specifications subject to change without notice.
P.O. Box 1325
• Newport Beach, CA 92659-0325 • Phone: 949-722-4800 • Fax: 949-548-5441 • E-mail: [email protected] • Website cla-val.com
©
INSTALLATION / OPERATION / MAINTENANCE
Flow Check Control
CVC
MODEL
N-CVC (R-4/09)
DESCRIPTION
The Flow Check is an adjustable hydraulically operat-
ed, diaphragm actuated, control. It opens for flow
when a preset differential pressure exists across the
control. The valve closes against a pressure reversal.
OPERATION
The Flow Check Control is normally closed. When the
hydraulic forces at the inlet exceeds the combined
hydraulic and spring force the valve opens for flow.
When a pressure reversal occurs the hydraulic plus
spring force prevents reversal of flow.
ADJUSTMENT (Range 1 to 15 feet of water)
To increase the differential to open the control, turn the
adjusting screw clockwise. To decrease the differential
to open the control, turn the adjusting screw counter-
clockwise.
INSTALLATION
Install the control cover up with the adjustment screw
at the top. Allow clearance for adjustment screw.
Place control in the line, noting the direction of flow. A
flow arrow on the body casting clearly indicates direc-
tion.
DISASSEMBLY
Valve does not need to be removed from line to
service.
1. Remove 4 10-32 machine screws on cover.
2. Remove cover with adjustment assembly
attached.
3. Remove spring and spring seat.
4. Remove diaphragm assembly.
To disassemble diaphragm assembly:
1. Unscrew diaphragm washer from disc retainer
assembly.
2. Remove diaphragm.
INSPECTION
Check diaphragm for damage due to wear or breaks.
Check disc in disc retainer for damage, imbedded parti-
cles, breaks, scoring. Check valve seat for damage,
wear, scoring. Check all parts for damage, corrosion,
erosion, mineral buildup. Clean all parts thoroughly.
1. Place the diaphragm assembly on the valve body
with the rubber disc insert down (next to seat).
2. Hole through casting into outlet end of body must be
aligned with extra hole in diaphragm.
3. Place spring on diaphragm washer in center.
4. Place spring seat washer on top of spring.
5. Place cover on diaphragm.
NOTE: Extra hole in cover must align with extra hole
through diaphragm and through body casting into outlet.
Valve will not operate if hole outlet does not intercon-
nect to cover chamber.
6. replace and tighten 4 13-32 machine screws.
REASSEMBLY
Reassembly is the reverse order of disassembly.
NOTE: The diaphragm, disc retainer and diaphragm
washer must be tight. Tighten by hand. Attempt to turn
the diaphragm between washers. If unable to turn,
assembly is secured.
TEST PROCEDURE
Apply pressure to outlet end with inlet open to atmos-
phere, control will close tight.
If Leakage occurs check for:
1. Damaged diaphragm, or refer to 2 in reassembly
instruction.
2. Loose diaphragm assembly.
3. Damaged seat in body.
4. Damaged disc in disc retainer.
Apply pressure to inlet - outlet open to atmosphere.
NOTE: Variable pressure of 1 to 15 foot head of water
should be used.
1. Turn adjustment screw in until it bottoms (do not
force).
2. Back off 3 1/2 turns.
3. Control will open with approximately 15 foot head.
4. Turn adjusting screw counter clockwise to obtain
lower settings.