Electronic actuated rate of flow control valve, Model – Cla-Val 340-02/3640-02 User Manual
Page 5
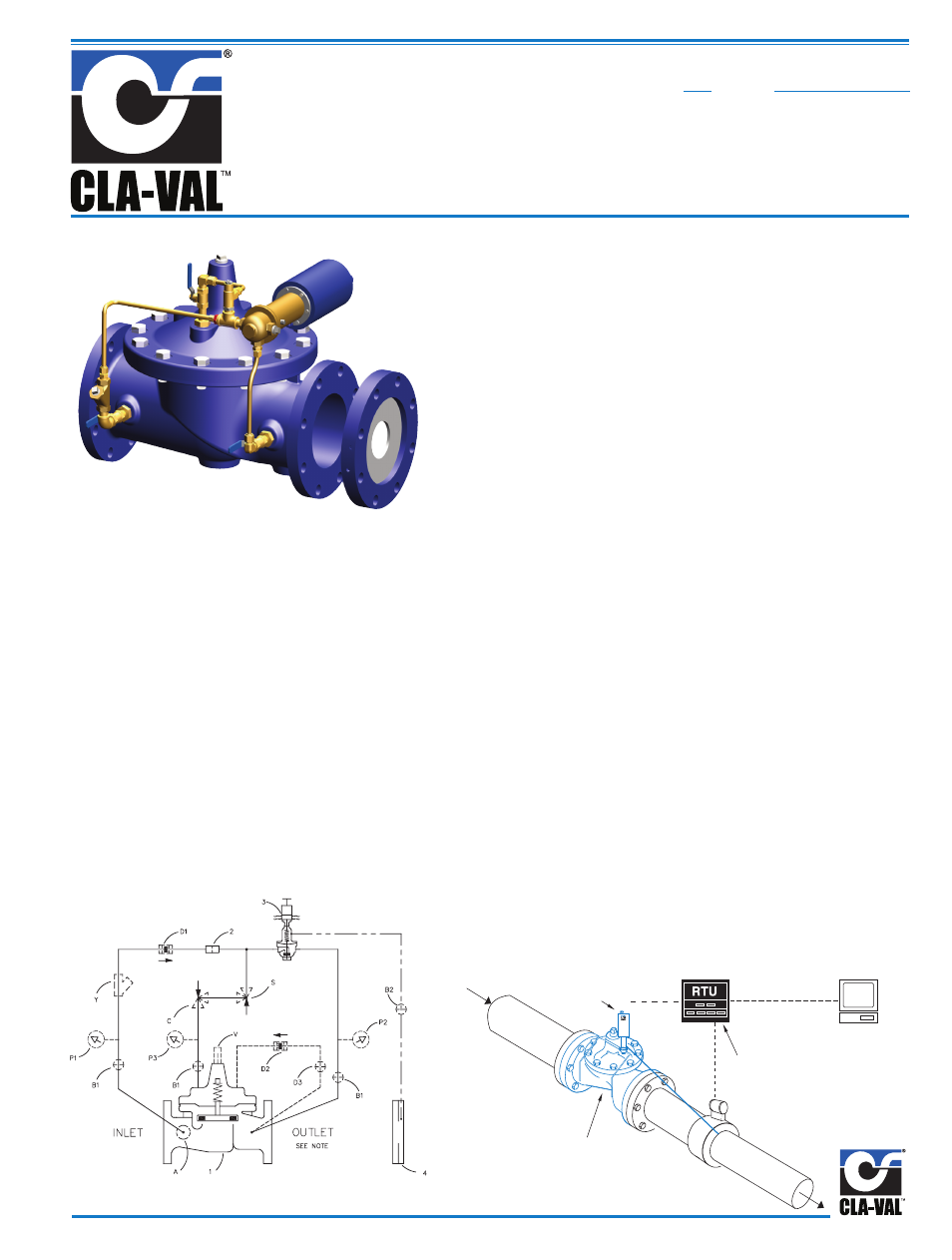
Electronic Actuated
Rate of Flow Control Valve
Remote
Set-Point
SCADA
Computer
Remote Telemetry Unit
(Customer Supplied)
Standard Flow Sensing
Orifice Plate Assembly
and Optional
Customer Supplied
Transmitter
CLA-VAL
340 Series
Electronic Actuated
Rate of Flow Valve
with CDHS-33 Pilot Control
Flow
CLA-VAL
CDHS-33
Control
•
Simplified Remote Valve Set-Point Control
•
12 to 24 VDC Input Power
•
Isolated Input
•
Reverse Polarity Protection
•
Reliable Hydraulic Operation
•
IP-68 (Submersible)
The Cla-Val Model 340-02/3640-02 Electronic Actuated Rate of Flow Control
Valve combines the precise control of field proven Cla-Val hydraulic pilots and
simple remote valve control. The Model 340-02/3640-02 valve controls flow by
limiting flow to a preselected maximum rate (within a four to one ratio), regardless
of changing line pressure. It is a hydraulically operated, pilot controlled,
diaphragm actuated control valve. The valve uses a CDHS-33 actuated pilot con-
trol, consisting of a hydraulic pilot and integral controller that accepts a remote set-
point command input and makes set-point adjustments to the pilot.
The recommended control method is simple remote set point change from an
RTU (Remote Telemetry Unit) to the CDHS-33 where the 4-20 mA command
signal is ranged to specific flow range of orifice plate and hydraulic pilot control
components. Very accurate control can be achieved when span does not
exceed 4:1 turndown. Since the CDHS-33 is pre-ranged to full spring range,
some on-site calibration may be necessary when this control method is used.
Free downloadable software is available from Cla-Val website for this purpose.
The CDHS-33 can also accommodate control systems where the RTU com-
pares flow rate transmitter signal to the remote set point command signal. The
RTU adjusts the CDHS-33 with 4-20 mA command signal containing an ade-
quate deadband to prevent actuator dithering after the two signals agree.
Internal continuous electronic monitoring of actuator position results in virtually
instantaneous position change with no backlash or dithering when control sig-
nal is changed. In the event of a power or control input failure, the CDHS-33
pilot remains in hydraulic control virtually assuring system stability under chang-
ing conditions. If check feature (“D”) is added, and pressure reversal occurs,
the valve closes to prevent return flow.
Typical Applications
The valve is designed to be used with supervisor control systems (SCADA),
having an isolated remote analog set-point output and a process variable
flow transmitter input. It is also an effective solution for lowering costs asso-
ciated with “confined space” requirements by eliminating the need for entry
into valve structure for set-point adjustments and system information.
Additional pilot controls, hydraulic and/or electronic, can be easily added to
perform multiple control functions to fit exact system requirements.
340-02
MODEL
(Full Internal Port)
3640-02
(Reduced Internal Port)
Schematic Diagram
Item Description
1
Hytrol (Main Valve)
2
X58C Restriction Fitting
3
CDHS-33 Electronic Differential Control
4
X52E Orifice Plate Assembly
Optional Features
Item Description
A
X46A Flow Clean Strainer
B
CK2 (Isolation Valve)
C
CV Flow Control (Closing)
D
Check Valves with Isolation Valve
P
X141 Pressure Gauge
S
CV Flow Control (Opening)
V
X101 Valve Position Indicator
Y
X43 "Y" Strainer