Pump Solutions Group Neptune Polymaster Liquid Polymer Blend & Feed System User Manual
Page 20
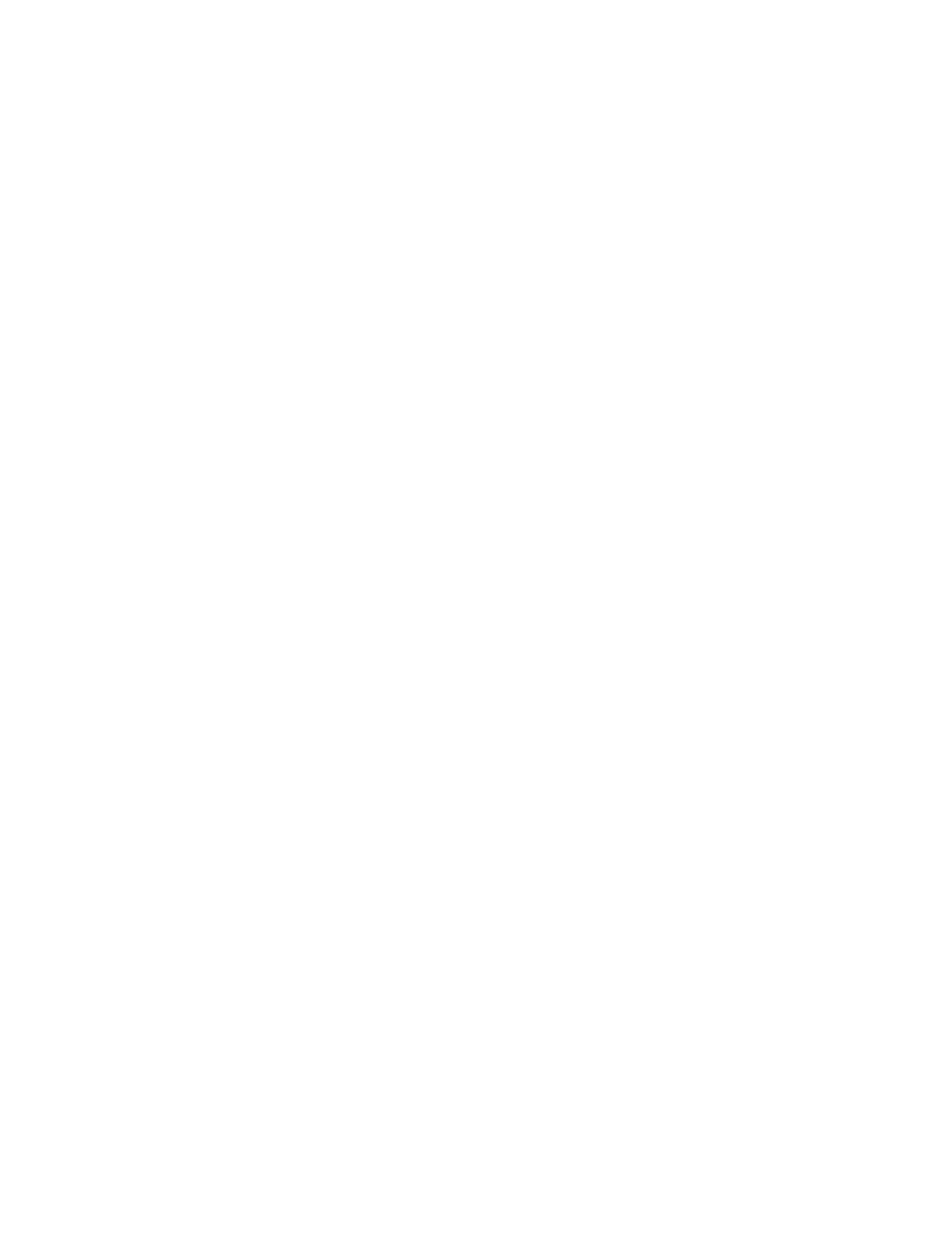
15
MAINTENANCE
1. Inspect for polymer or water leakage at the components.
A. If joint leakage is observed, tighten carefully. Most joints are plastic (i.e. PVC, Delrin, acrylic) and
over-tightening will lead to breakage.
B. If component leakage is observed, replace the defective part. Contact Neptune for part replacement.
2. Inspect light and switches for proper operation.
A. If a light or switch is inoperative, replace the defective part.
3. Re-calibrate the pump.
A. If the brand or type of polymer is changed or if the pump flow rates appear to be different than originally
calibrated, recalibrate and update the calibration graph. Inform the system operator so proper system
performance will be achieved.
4. Lubrication - No lubrication required other than may be called for in the pump instruction manual.
5. Flush After Each Use
A. The Polymaster should be flushed before shutdown. To flush, turn off the polymer feed pump or set the
stroke speed to “0” using the controls on the face of the pump. Now, only dilution water is flowing
through the system. Allow the water to run for 10 minutes, while the Gatlin is turning, to completely
flush-out the system. Do not flush the chemical feed pump or feed pump suction and discharge lines
with water as water will mix with the polymer in the line and may solidify or gel. See long terms
storage instructions on page 10 for details on flushing pump head and lines.
6.
Check the Polymer line strainer and water line strainer for debris with every new drum of polymer.
7. Follow manufacturer’s recommendation for routine maintenance of the chemical metering pump.