Maintenance, servicing, Longer periods of non-operation, Faults - causes and solutions – Xylem Z8 ZR8 Z10 ZR10 Z12 ZR12 User Manual
Page 34: 3 shutting down
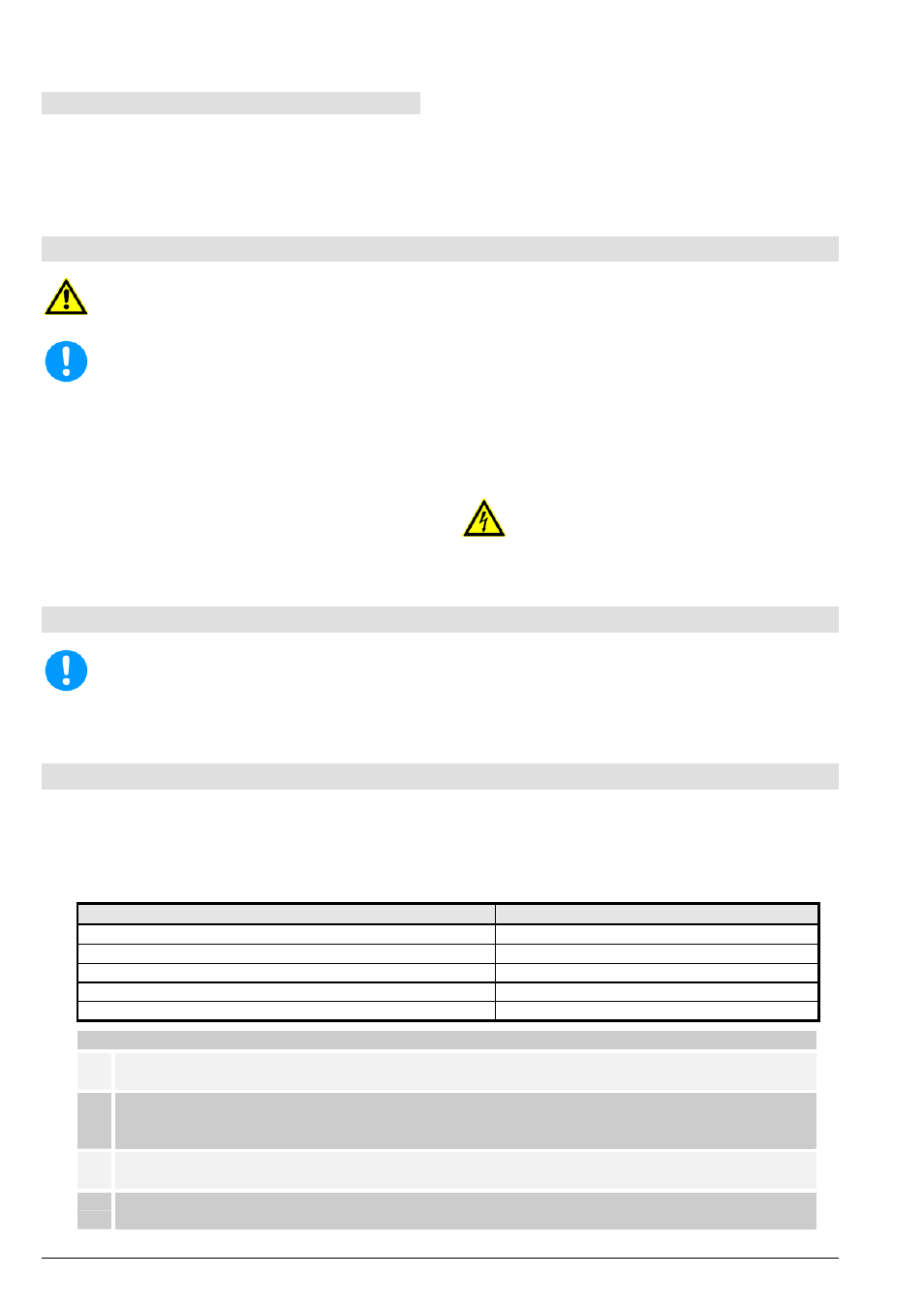
Installation, Operating and Maintenance Instruction
page
34
6.3 Shutting down
Close the valve in discharge pipe right before
(max. 10 seconds) switching off the motor. This is
not necessary if there is a spring-loaded check
valve.
Switch off motor (make sure it runs down quietly).
7. Maintenance, Servicing
Work should only be carried out on the pump or
pump unit when it is not in operation. You must
observe Point 1.4 "Safety instructions".
Maintenance and servicing work must only be
carried out by trained, experienced staff who
are familiar with the contents of these Operating
Instructions, or by the Manufacturer's own
service staff.
The submersible pump requires virtually no
maintenance. Inspection work is limited to the
periodical measuring of insulating resistance (once
every 2 years, recommended once per year when the
motor is cold) as well as regular checking of the
operating voltage, current consumption and the flow
data. We recommend that you record and compare
these data in the "Log Book". The development of this
data can perhaps make it possible to recognize
damage early on thus making it possible to avoid
greater damage or even complete destruction.
Slow reduction of the flow rate at the same discharge
level, with normal or reduced current consumption
indicates increased wear and tear of the pump
components (e.g. through sand). A large increase or
fluctuations in current consumption indicate a
mechanical fault (e.g. increased mechanical friction
due to a defective bearing). The unit should be taken
out of operation immediately to prevent greater
damage.
The electrical devices should be inspected
annually by a specialist to see that they function
properly.
8. Longer periods of non-operation
When starting up, follow the instructions for
starting up for the first time (see Point 6)!
Check insulation resistance of installed units at
monthly intervals and carry out a short trial run to
prevent the pump part getting stuck due to sediments.
The minimum flooding of the unit must be guaranteed
during this process.
9. Faults - Causes and Solutions
The following notes on causes of faults and how to
repair them are intended as an aid to recognising the
problem. The manufacturer's Customer Service
Department is available to help repair faults that the
operator cannot or does not want to repair. For repair
and modification of the pump by the customer pay
attention to the design data of the order confirmation
as well as to point 1.2 - 1.4 of this instruction manual.
If necessary, the written agreement of the
manufacturer must be obtained.
Faults
Code no. for cause and method of repair
Motor protection switches itself off
1, 2, 10
Electricity consumption too high. Releases motor protection. 2, 3, 4, 5, 6, 7, 24
Pump does not start
2, 3, 5, 7, 8, 9, 10
Pump runs but does not transport
11, 12, 13, 14
Output too low
15, 16, 17, 18, 19, 20, 21, 22, 23
Meaning of code number for cause and method of repair
1.
Motor protection switch is wrongly set
• Check setting or replace the motor protection switch
2.
Phase failure
• replace defective safety fuses
• Check pipes for damage
3.
Wrong frequencies or under voltage
• Compare voltage and frequency with data on the rating plate
4.
Rotates in the wrong direction
• Swap over phases of power supply