Bell & Gossett S14141B 70X Multiple Pump Pressure Booster Systems User Manual
Page 6
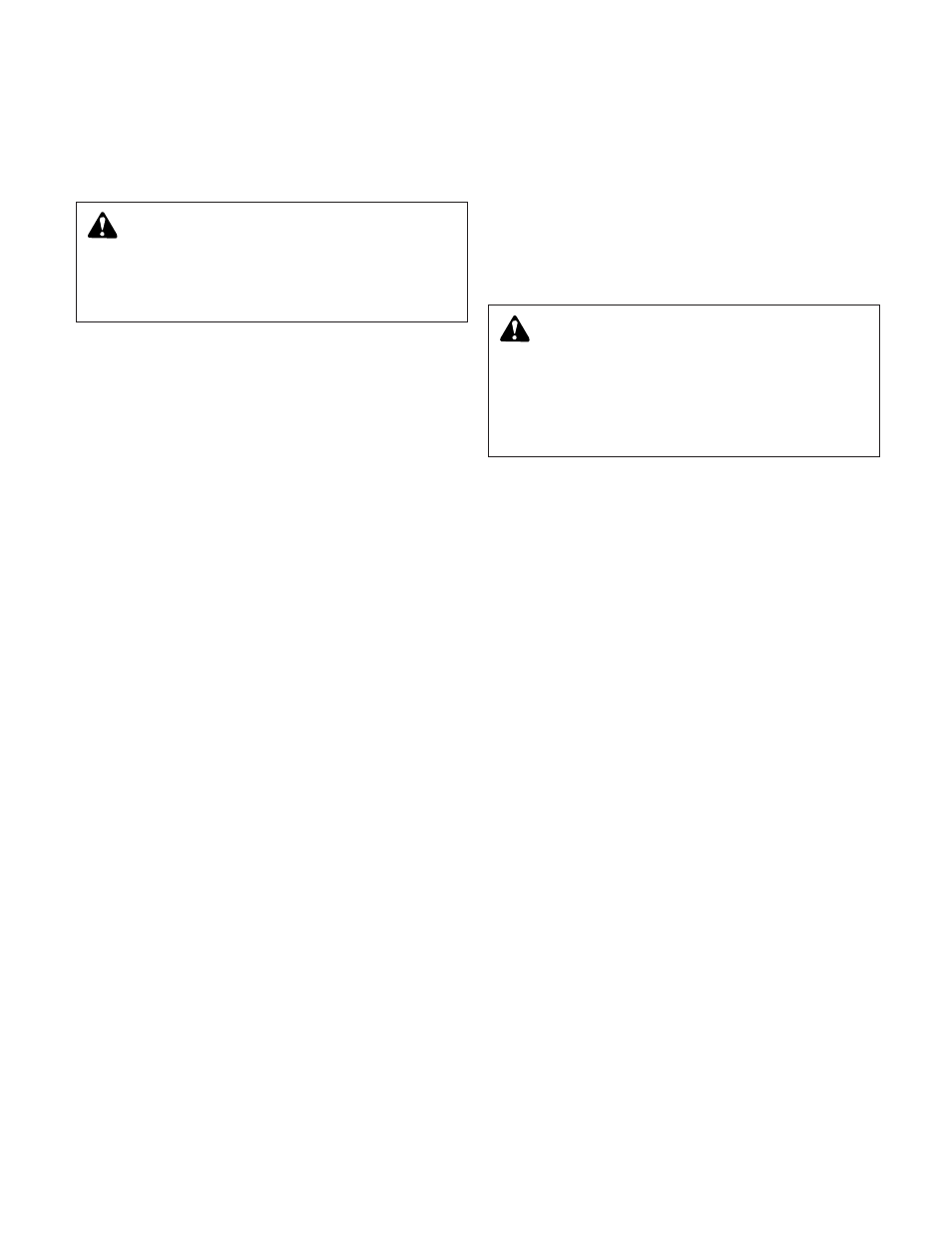
2.5.2
After hydrotesting, drain plugs are removed, to
facilitate system drainage, placed in a cloth bag
and secured to the unit. Drain plugs shall be rein-
stalled prior to filling the system with fluid. Inspect
all unit piping connections. Joints may also
become loose during transit due to vibration and
shock. All joints are to be checked for tightness.
Flanged joints should be checked for proper torque
of all flange bolts prior to filling the system with fluid.
2.5.3
Make all necessary system piping connections. Be
aware that connecting dissimilar metals to the
headers can lead to corrosion damage due to gal-
vanic corrosion. The rate of corrosion is dependant
on various factors some of which are; the potential
between the dissimilar metals, electrolyte conduc-
tivity, geometry and area of the metals. Dielectric
connections are recommended between dissimilar
metals at the header connection. Be sure to elimi-
nate any pipe strain on the unit. Support all pipes
independently by use of pipe hangers near the unit.
DO NOT ATTEMPT TO FORCE THE SUCTION OR
DISCHARGE LINES INTO POSITION. Refer to
assembly drawing for customer piping connections.
2.5.4
The maximum suction pressure shall not exceed
150 psi. Dead head pressure plus suction pressure
shall not exceed 175 psi.
2.5.5
As a rule, ordinary wire or band hangers are not
adequate to maintain alignment. It is very impor-
tant to provide a strong, rigid support for the suc-
tion line. A saddle hanger is recommended.
2.5.6
For critical installations, equipment for absorbing
expansion and vibration should be installed at the
inlet and outlet connections of the unit.
2.5.7
Eccentric increasers can be used in the suction pipe
line when increasing the pipe size, with straight
sides of increaser on top to eliminate air pockets.
2.5.8
On an open system with a suction lift, a foot valve
of equal or greater area than the pump suction is
recommended. Prevent clogging by using a strainer
at the suction inlet next to the foot valve. The
strainer should have an area three times that of the
suction pipe. Provisions must be made to prime
the pump suction piping on start up. Do not start
the pump unless all suction piping is full of water.
2.6 MISCELLANOUS CONNECTIONS
2.6.1
Hydro-Pneumatic Tank (optional): The tank is sup-
plied mounted on a separate base for ease of han-
dling, unit installation and space considerations.
Mount the tank adjacent to the unit. A union con-
nection is provided to allow quick connection to
the unit. The tank is intended to maintain system
pressure due to minor system leaks and periods of
low demand.
2.6.2
Pre-charge the Hydro Pneumatic tank prior to fill-
ing the system. The tank should be air charged to
the pump restart pressure minus 1 psi. If the tank
is located above the booster, the precharge pres-
sure is calculated by pump restart pressure minus
tank elevation above pressure booster (psi) minus
1 psi.
2.6.3
For tanks supplied by others, refer to appendix E
for tank installation.
2.7 LUBRICATION
2.7.1
Before starting, all pumps and motors should be
checked for proper lubrication.
2.8 WIRING
2.8.1
Refer to the controller instruction manual for elec-
trical connection, set-up and troubleshooting.
2.9 POWER WIRING
2.9.1
The Control Panel is designed to operate at a spe-
cific voltage as indicated on the control panel
nameplate. Verify proper transformer primary
wiring per the job-specific wiring diagram. Check
power leads in accordance with wiring diagram
enclosed in control cabinet. The voltage tolerance
is +10%/-10%.
2.10 ANALOG SIGNAL WIRING
2.10.1 If installing the panel on an existing system, twisted
pair shielded cable (#22 AWG, Belden type 8762,
Alpha #2411 or equal) should be installed for the
DC control wiring. The shield must be terminated
in the control panel. Do not connect the shield at
the other end of the cable! Insulate the shield so
that no electrical connection is made at the other
end of the cable. A twisted pair of #22 AWG con-
ductors (Belden 8442 or equal) can be used in
place of shielded cable. The cable length must be
limited to 3000 feet for #22 AWG wire.
2.11 PRESSURE TRANSMITTER WIRING
(4-20 mA Analog Signals)
2.11.1 (Optional) A pressure transmitter, if supplied with
the booster unit, is installed at the discharge
header. Otherwise, a pressure transmitter is sup-
plied loose. It is recommended that the sensor be
installed in the zone furthest away or at the most
critical zone. Refer to wiring diagram for exact ter-
minal locations.
DANGER: Electrical shock hazard. Inspect all
electrical connections prior to powering the unit.
Wiring connections must be made by a qualified electrician
in accordance with all applicable codes, ordinances, and
good practices.
FAILURE TO FOLLOW THESE INSTRUCTIONS COULD
RESULT IN SERIOUS PERSONAL INJURY, DEATH,
AND/OR PROPERTY DAMAGE.
6
CAUTION: Failure to reinstall drain plugs, check all
joints for tightness and flange bolts for proper torque
could result in leaks and/or flooding.
FAILURE TO FOLLOW THESE INSTRUCTIONS COULD
RESULT IN PROPERTY DAMAGE AND/OR MODERATE
PERSONAL INJURY.