Data sheet, Application information – Diodes AM9800 User Manual
Page 8
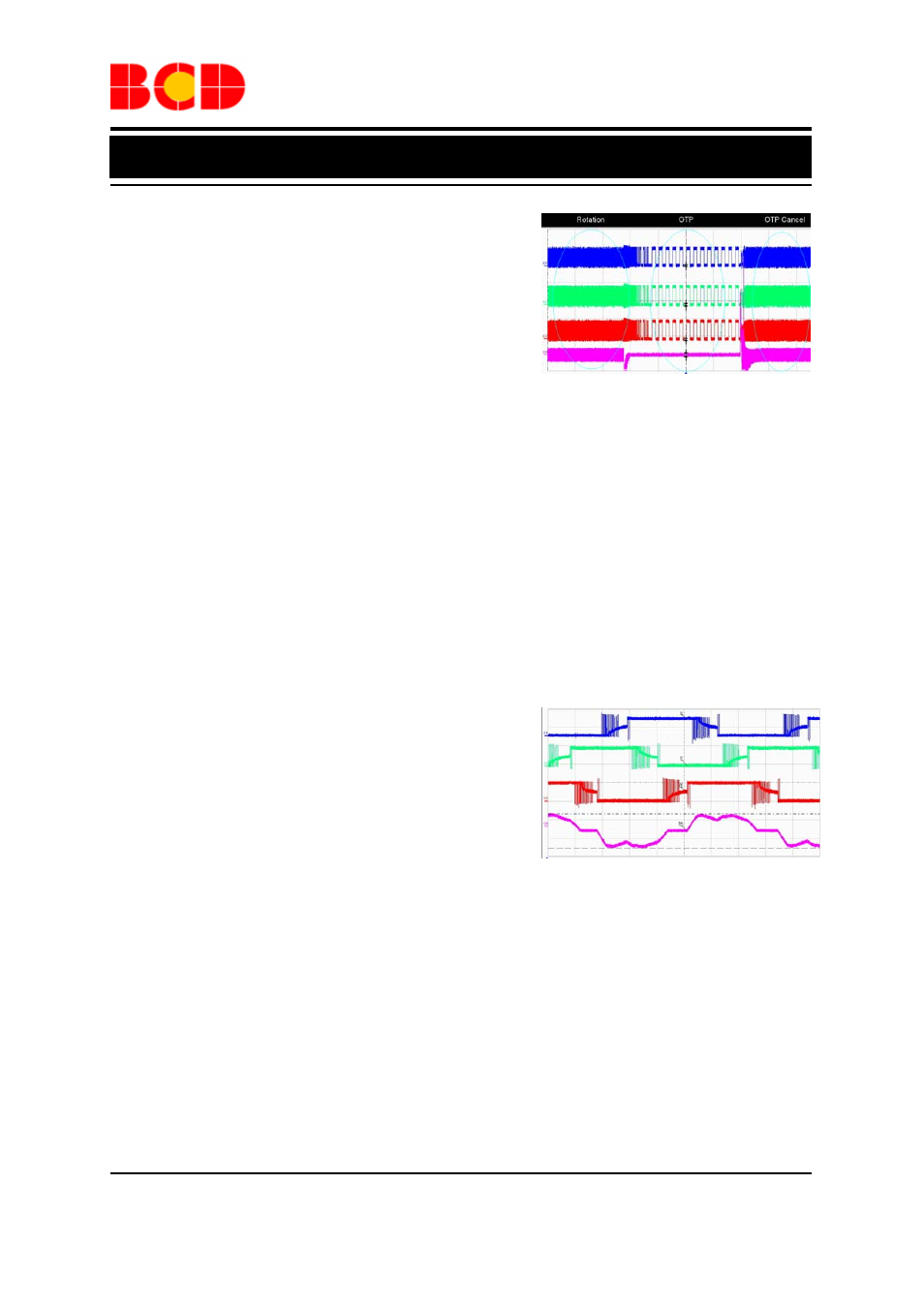
Data Sheet
Three Phase Direct PWM Sensorless Motor Driver AM9800
Sep. 2012 Rev. 1. 0 BCD Semiconductor Manufacturing Limited
8
Application Information
1. Reverse Connection of Power Supply
Connector
Reverse connection of power supply connector may
break IC. Some methods such as inserting a diode
between power supply and VCC terminal can be
taken to avoid the reverse connection destruction.
2. Power Supply Line
Back electromotive force (EMF) causes regenerated
current to the power supply line, so insert a capacitor
(recommended value: 1
µF or larger) as close as
possible to the space between the power supply pin
(VCC pin) and ground pin (SGND pin) for routing
regenerated current.
3. GND Potential and External Components
Ensure that the potential of GND terminal is the
minimum potential in any operating condition.
External components connected to the ground must
be connected with lines that are as short as possible
and external components connected between IC pins
must be placed as close to the pins as possible.
4. Mounting Failures
In the process of attaching IC to the printed board,
more attention must be paid to the direction and
location of the IC, since mounting failures may also
break IC. In addition, destruction is also possible
when the circuit is shorted by foreign substance
between outputs or between output and power supply
or between output and GND.
5. Thermal Shutdown Circuit
Considering the power dissipation under actual
operating condition, the thermal design must be
applied with sufficient margin.
AM9800 features thermal shutdown (TSD) circuit
(protection temperature is 175
°C typical and
hysteresis width is 25
°C typical). When the chip
temperature reaches the TSD circuit temperature, the
output terminal becomes an open state. TSD circuit is
designed simply for the purpose of intercepting IC
from overheating. Make sure that the IC should not
be used again after this circuit operating. Figure 9
shows a fan rotates normally first and then enter into
OTP mode since the chip temperature reaches 175
°C.
Finally the chip temperature decreases below 150
°C,
then OTP mode is canceled and the fan rotates
normally again.
Figure 9. OTP Function
6. F/R Function
A high level input causes the current to flow into the
motor in the order of U, V, and W and a low level
input in the order of U, W, and V. When the motor is
used with the F/R pin open, the built-in resistor
enables the F/R pin to GND. Changing the order of
current application turns the motor to rotate in the
opposite direction. Switching H/L of F/R (pin 9)
terminal should not be done during the motor rotation.
It should be done once the motor stops. F/R terminal
should be connected to VCC or GND for reducing
PWM noise. Figure 10 shows a rotating fan’s
waveform at forward mode (F/R pin is connected to
SGND pin).
Figure 10. Rotation Mode Waveform (Forward Mode)
7. PWM Mode
The output transistor is on when a high-level voltage
is input to the PWM pin (pin 11), and is off when a
low-level voltage is input. PWM controls the speed
of the motor by inputting the pulse in accordance
with the duty cycle to the PWM pin. When the motor
is operated with the PWM pin open, the built-in
resistor enables the PWM pin to change to high-level
voltage and the motor speed rises to full speed. When
the PWM pin is fixed at low-level voltage, the motor
decelerates, and after the motor stops, it enters
“Power Saving Mode”. Figure 11 shows a rotating
fan’s waveform at PWM Mode.
V
UO
5V/div
V
VO
5V/div
V
WO
5V/div
I
WO
100mA/div
Time 1s/div
V
UO
5V/div
V
VO
5V/div
V
WO
5V/div
I
WO
200mA/div
Time 1ms/div