Component selection, Layout considerations – Diodes ZXGD3102 User Manual
Page 9
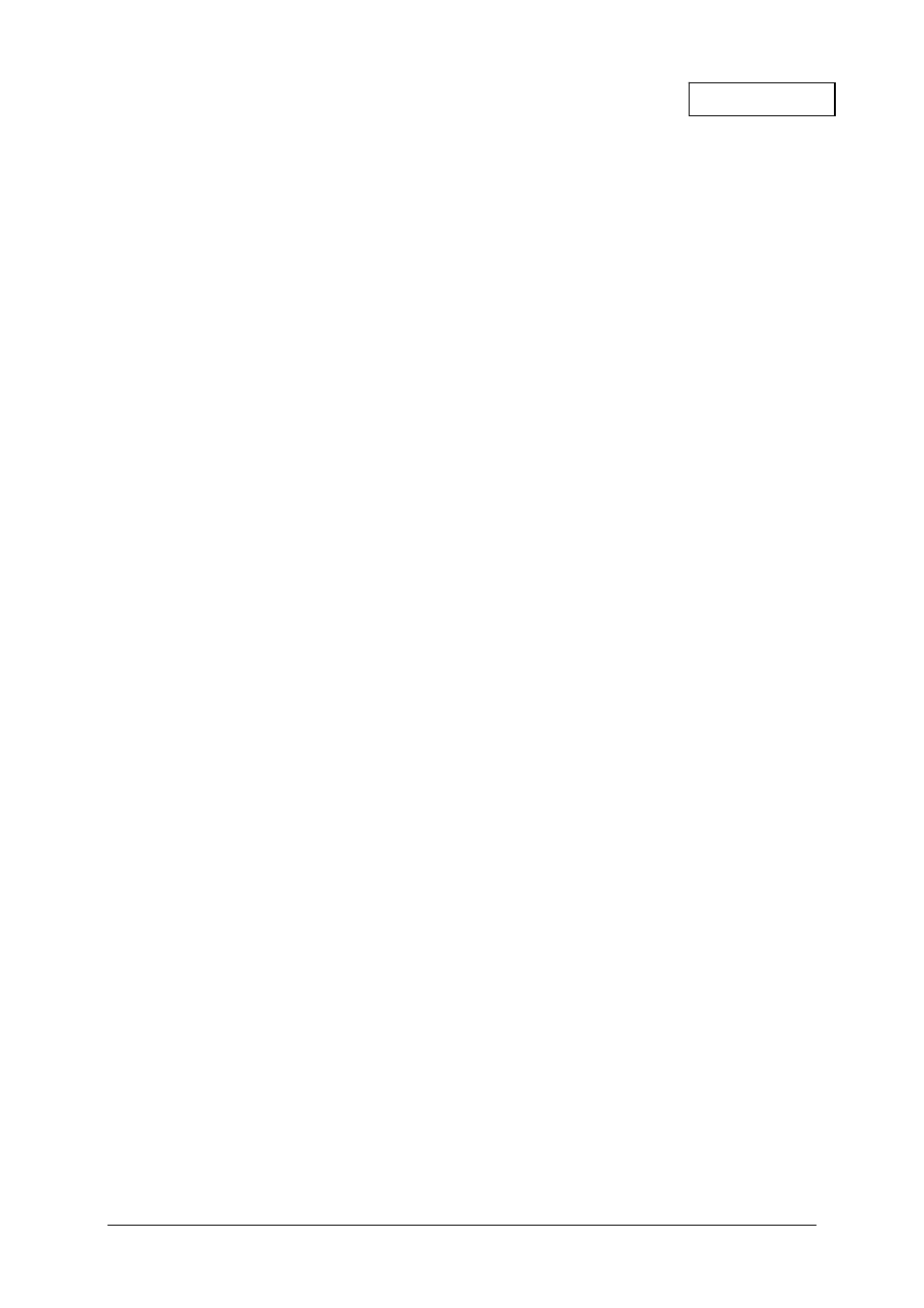
Issue 4, May 2009
9
©Diodes Incorporated 2008
ZXGD3102T8
Component Selection
It is advisable to decouple the ZXGD3102 closely to V
CC
and ground due to the possibility of high peak
gate currents, as indicated by C1 in Figure 4. In applications where the input voltage is higher than
12V, it is recommended to use a Zener diode, ZD1 as shown in the Typical Application Circuit on page
1, and in Figure 2, in order to limit the V
CC
supply voltage to the ZXGD3102 and also to limit the
maximum voltage applied to the gate of the MOSFET. A suitable value for the Zener is 10V.
The proper selection of external resistors R
REF
and R
BIAS
is important to the optimum device operation.
Select a value for resistor R
REF
to give a reference current, I
REF
, of ~2.4mA. The value of R
BIAS
must
then be selected to give a bias current, I
BIAS
, of approximately 1.2 times I
REF
. This set the turn-off
threshold voltage V
T
of the controller to ‘-24mV’ at V
CC
=10V.
R
REF
= (V
CC
-0.7V)/ 0.0024
R
BIAS
= (V
CC
-0.7V)/ 0.0028
Alternatively, R
REF
and R
BIAS
can be chosen to be equal to set the turn-off threshold voltage V
T
to ‘-
29mV’ at V
CC
=10V. This also reduces the IC current consumption when the gate voltage is off.
External gate resistor to GATEH pin is optional. It can be inserted to control the turn-on gate rise time
which may help with in-rush current protection, EMI issues or power dissipation within the part. The
addition of C
BIAS
controls the switch-on delay of the MOSFET, and ensures stability. A suitable value
is 1nF.
Layout considerations
The Gate pins should be as close to the MOSFET gate as possible. Also the ground return loop
should be as short as possible. The decoupling capacitor should be close to the V
CC
and Ground pin,
and should be a X7R type. Trace widths should be maximized in the high current path through the
MOSFET and ground return in order to minimize the effects of circuit inductance and resistance.
For best thermal performance, the PCB heat path from pins 5 and 6 needs attention. The area of
copper connected to pins 5 and 6 should be maximised.