Sample pressure and flow – Analytical Industries GPR-1500 A Series Trace PPM Oxygen Analyzer User Manual
Page 7
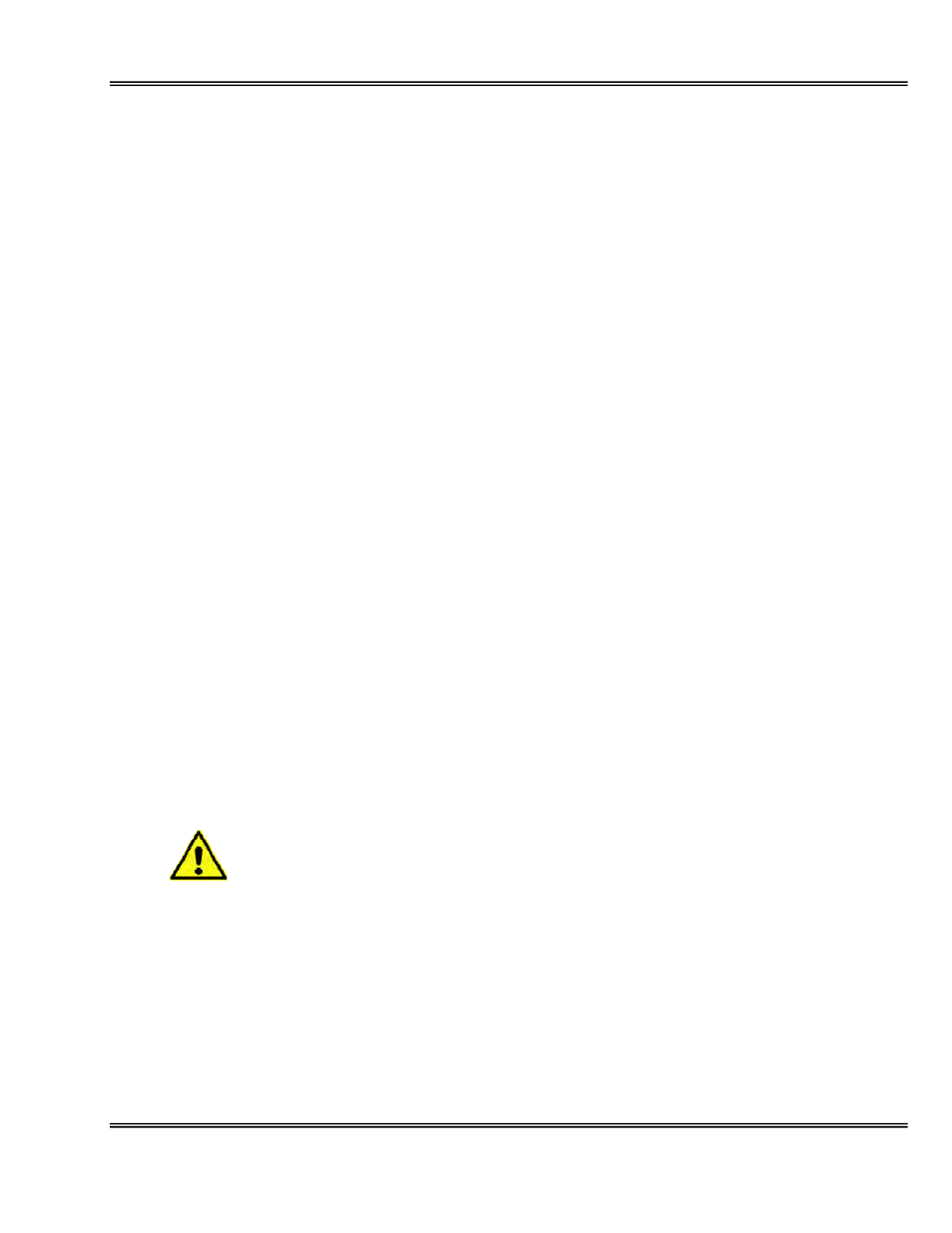
Advanced Instruments, Inc
7
Materials: Assemble the necessary zero, sample and span gases and optional components such as valves,
coalescing or particulate filters, and pumps as dictated by the application. Stainless steel tubing is essential
for maintaining the integrity of the gas stream for low % or PPM O
2
level analysis.
Operating Temperature: The sample must be sufficiently cooled before it enters the analyzer and any
optional components. A coiled 10 foot length of ¼” stainless steel tubing is sufficient for cooling sample
gases as high as 1,800 ºF to ambient. The recommended operating temperature is below 35 ºC. However,
the analyzer may be operated at temperature up to 45 ºC on an intermittent basis but the user is expected to
accept a reduction in expected sensor life –as a rule of thumb, for every degree ºC increase in temperature
(above 25 ºC), the sensor life is reduced by approximately 2.5%.
Heat: Situate and store the analyzer away from direct sources of heat.
Liquid and Object Entry: The analyzer should not be immersed in any liquid. Care should be taken so that
liquids are not spilled into and objects do not fall into the inside of the analyzer.
Handling: Do not use force when using the switches, knobs or other mechanical components. Before
moving your analyzer be sure to disconnect the wiring/power cord and any cables connected to the output
terminals of the analyzer.
Sample Pressure and Flow
All electrochemical oxygen sensors respond to partial pressure changes in oxygen. The sensors are equally
capable of analyzing the oxygen content of a flowing sample gas stream or monitoring the oxygen
concentration in ambient air (such as a confined space in a control room or an open area around a landfill or
bio-pond). The following is applicable to analyzers equipped with fuel cell type oxygen sensors.
Analyzers designed for in-situ ambient or area monitoring has no real sample inlet and vent. The sensor is
exposed directly to the sample gas and it is intended to operate at atmospheric pressure. The analyzer has
a built-in pressure sensor and the sensor output is automatically compensated for any atmospheric pressure
changes.
Inlet Pressure
: For the analyzers designed to measure oxygen in a flowing gas stream, the inlet
sample pressure must be regulated between 5-30 psig. Although the rating of the SS tubing and tube
fittings/valves itself is considerably higher (more than 100 psig), a sample pressure of 5-30 psig is
recommended for ease of control of sample flow.
The analyzer equipped with a sample system has designated SAMPLE and VENT ports. Connect SAMPLE
gas to SAMPLE and the vent to the VENT ports only.
Caution: If the analyzer is equipped with an optional H2S scrubber, sample inlet pressure must
not exceed 30 psig.
Outlet Pressure
: In applications where sample pressure is positive, the sample must be vented to an
exhaust pipe at a pressure less than the inlet pressure so that the sample gas can flow through the sensor
housing. Ideally, the sample must be vented to atmospheric pressure.
Note: The sensor may be used at a slight positive pressure (e.g., when sample is vented to a common
exhaust where the pressure might be higher than 1 atmosphere). However, the pressure at the sensor must
be maintained at all times including during the span calibration. This may be accomplished by using a back-
pressure regulator at vent line of the analyzer. Caution: A sudden change in pressure at the sensor may
result in the sensor electrolyte leakage.
Flow rates of 1-5 SCFH cause no appreciable change in the oxygen reading. However, flow rates above 5
SCFH may generate a slight backpressure on the sensor resulting in erroneous oxygen readings.