Applications information – Rainbow Electronics MAX16831 User Manual
Page 14
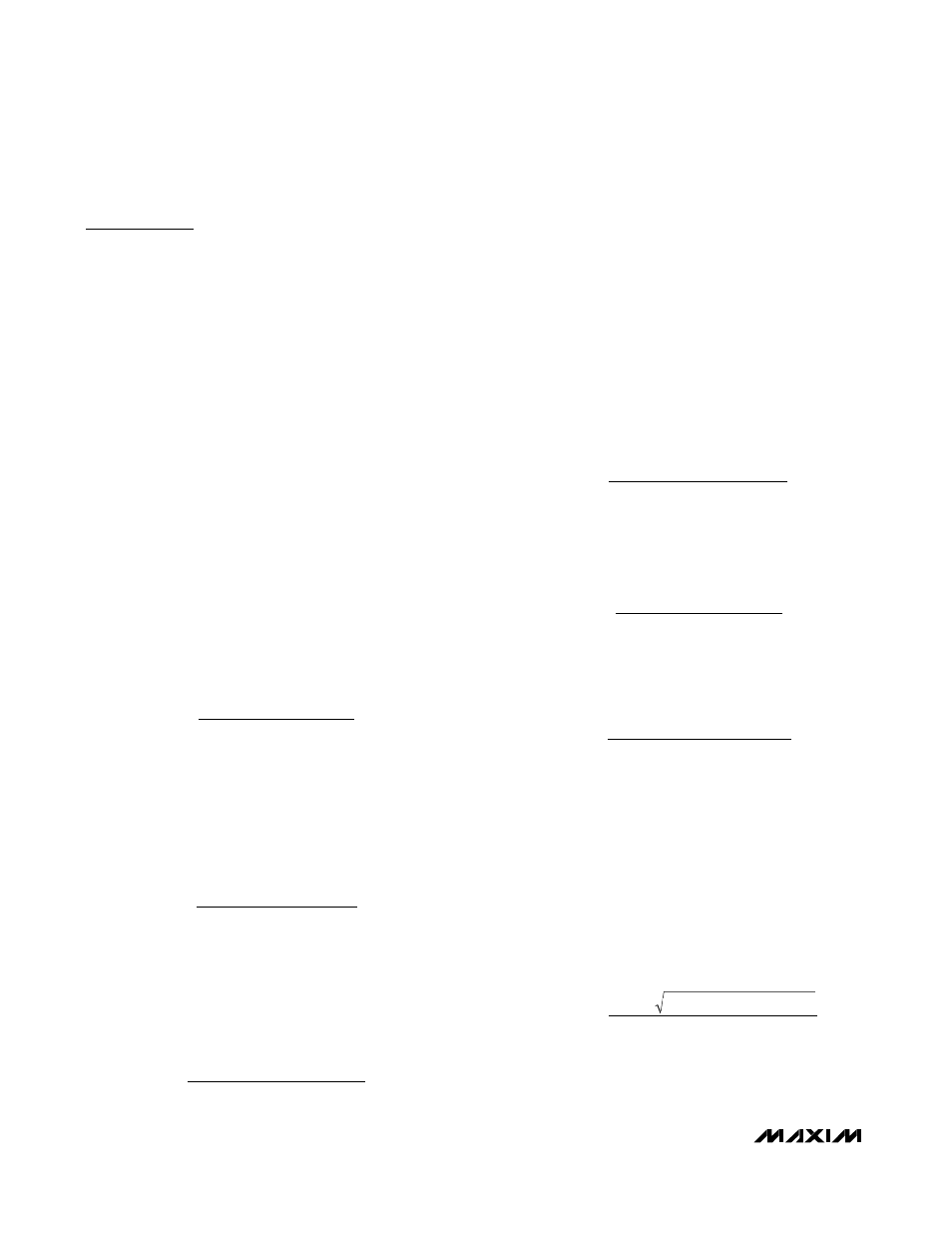
MAX16831
Applications Information
Inductor Selection
The minimum required inductance is a function of oper-
ating frequency, input-to-output voltage differential, and
the peak-to-peak inductor current (
∆I
L
). Higher
∆I
L
allows for a lower inductor value while a lower
∆I
L
requires a higher inductor value. A lower inductor value
minimizes size and cost, improves large-signal tran-
sient response but reduces efficiency due to higher
peak currents and higher peak-to-peak output ripple
voltage for the same output capacitance. On the other
hand, higher inductance increases efficiency by reduc-
ing the ripple current,
∆I
L
. However, resistive losses
due to extra turns can exceed the benefit gained from
lower ripple current levels, especially when the induc-
tance is increased without also allowing for larger
inductor dimensions. A good compromise is to choose
∆I
L
equal to 30% of the full load current. The inductor
saturating current is also important to avoid runaway
current during the output overload and continuous
short circuit. Select the I
SAT
to be higher than the maxi-
mum peak current limit.
Buck configuration: In a buck configuration, the aver-
age inductor current does not vary with the input. The
worst-case peak current occurs at a high input voltage.
In this case, the inductance L for continuous conduc-
tion mode is given by:
where V
INMAX
is the maximum input voltage, f
SW
is the
switching frequency, and V
OUT
is the output voltage.
Boost configuration: In the boost converter, the average
inductor current varies with line and the maximum aver-
age current occurs at low line. For the boost converter,
the average inductor current is equal to the input cur-
rent. In this case, the inductance L is calculated as:
where V
INMIN
is the minimum input voltage, V
OUT
is the
output voltage, and f
SW
is the switching frequency.
Buck-boost configuration: In a buck-boost converter,
the average inductor current is equal to the sum of the
input current and the load current. In this case, the
inductance L is:
where V
INMIN
is the minimum input voltage, V
OUT
is the
output voltage, and f
SW
is the switching frequency.
Output Capacitor
The function of the output capacitor is to reduce the
output ripple to acceptable levels. The ESR, ESL, and
the bulk capacitance of the output capacitor contribute
to the output ripple. In most of the applications, the out-
put ESR and ESL effects can be dramatically reduced
by using low-ESR ceramic capacitors. To reduce the
ESL effects, connect multiple ceramic capacitors in
parallel to achieve the required bulk capacitance.
In a buck configuration, the output capacitance, C
F
, is
calculated using the following equation:
where ∆V
R
is the maximum allowable output ripple.
In a boost configuration, the output capacitance, C
F
, is
calculated as:
where I
OUT
is the output current.
In a buck-boost configuration, the output capacitance,
C
F
, is calculated as:
where V
OUT
is the voltage across the load and I
OUT
is
the output current. Connect the output capacitor(s)
from the output to ground in a buck-boost configuration
(not across the load as for other configurations).
Input Capacitor
An input capacitor connected between UVEN and
ground must be used when configuring the MAX16831
as a buck converter. Use a low-ESR input capacitor
that can handle the maximum input RMS ripple current.
Calculate the maximum allowable RMS ripple using the
following equation:
In most of the cases, an additional electrolytic capaci-
tor should be added to prevent input oscillations due to
line impedances.
I
I
V
V
V
V
IN RMS
OUT
OUT
INMIN
OUT
INMIN
(
)
(
)
=
Ч
Ч
-
C
V
I
V
V
V
f
F
OUT
OUT
R
OUT
INMIN
SW
≥
Ч
Ч
Ч
+
Ч
2
∆
(
)
C
V
V
I
V
V
f
F
OUT
INMIN
OUT
R
OUT
SW
≥
Ч Ч
Ч
Ч
(
)
-
2
∆
C
V
V
V
V
L V
f
F
INMAX
OUT
OUT
R
INMAX
SW
≥
Ч
Ч Ч Ч
Ч
(
)
-
∆
2
2
L
V
V
V
V
f
I
OUT
INMIN
OUT
INMIN
SW
L
=
Ч
+
Ч
Ч
(
)
∆
L
V
V
V
V
f
I
INMIN
OUT
INMIN
OUT
SW
L
=
Ч
Ч
Ч
(
)
-
∆
L
V
V
V
V
f
I
OUT
INMAX
OUT
INMAX
SW
L
=
Ч
Ч
Ч
(
)
-
∆
High-Voltage, High-Power LED Driver with
Analog and PWM Dimming Control
14
______________________________________________________________________________________