Rotor housing, Electrical, Brakes – Milton CAT PM 200 User Manual
Page 11: Steering, Weights, Conveyor system, Pm-200 specifications
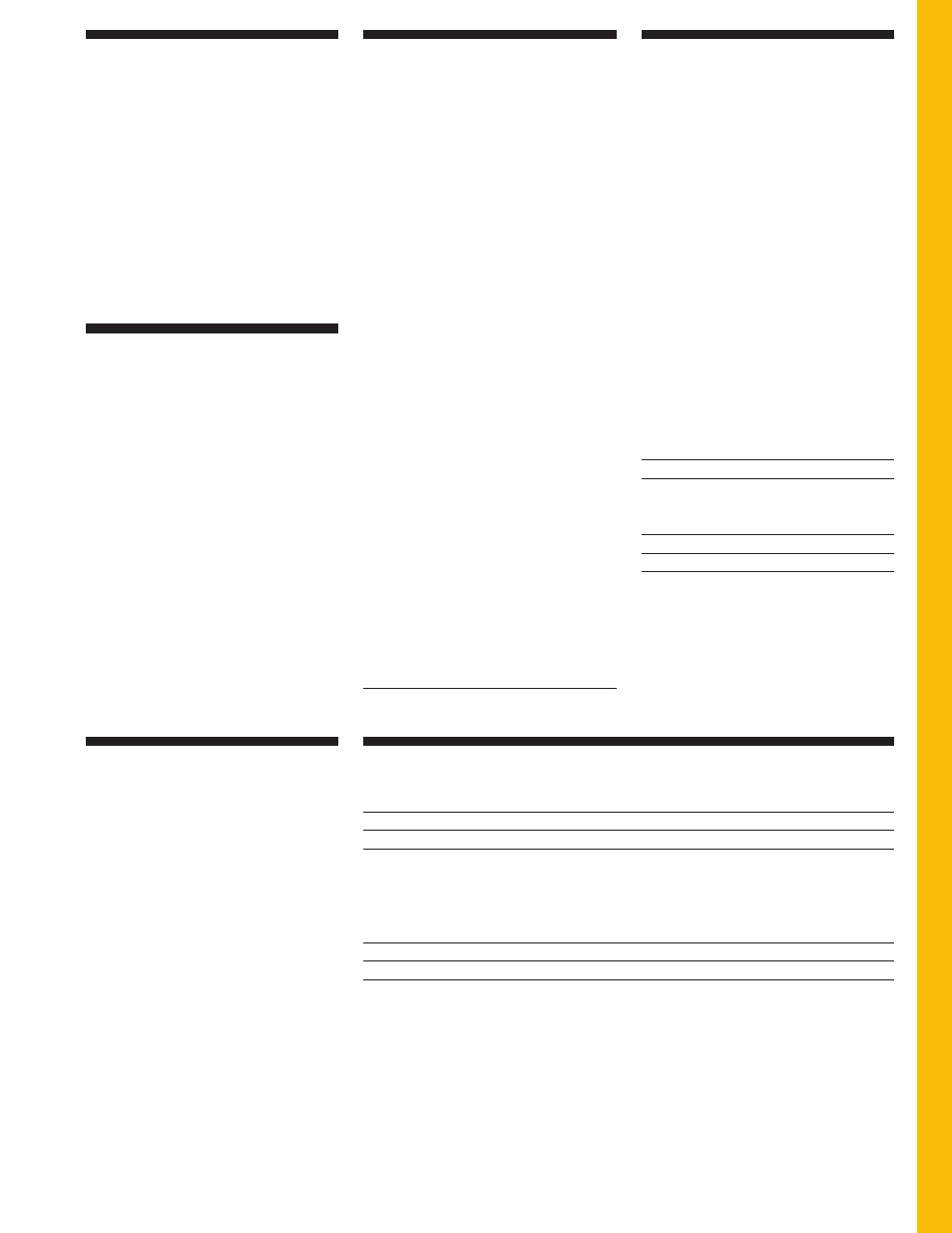
11
Rotor Housing
■
Large discharge opening clears out
the rotor housing fast for increased
production and reduced tool wear.
■
Side plate contact surfaces feature a
wear-resistant ski for reduced wear
and longer service life.
■
Floating moldboard with adjustable
down pressure is standard and
features replaceable cutting edges.
■
Height control for moldboard located
at operator’s station and at two
ground level control stations.
Steering
Hydraulic power-assist steering with
two steering wheels on operator’s
console. Four steering modes with
automatic realignment of rear tracks
through ECM is standard.
Features
■
Double-acting steering cylinders
control the front and rear tracks and
are powered by a pressure-
compensated, piston-type pump.
Constant pressure is assured in the
steering system.
■
Switch on operator’s console
provides four steering modes.
Steering Modes
■
Front steer only—controlled by the
steering wheel from both driving
positions. The ECM automatically
aligns rear tracks to the center
position for straight tracking.
■
Rear steer—controlled by joysticks
on operator’s console and toggle
switches at ground level control
panels. Rear steering is controlled
manually in this steering mode.
■
Crab—front and rear tracks turn
simultaneously in the same direction.
■
Coordinated—front and rear tracks
turn simultaneously in the opposite
direction.
Turning Radius:
Minimum
2.0 m (6' 5")
Brakes
Primary Brake Features
■
Closed-loop hydrostatic drive
provides dynamic braking during
normal operation.
Parking Brake Features
■
Spring-applied/hydraulically-released
multiple disc type brake mounted on
each gear reducer. Brakes are applied
automatically when propel lever is in
the neutral detent position.
■
Secondary brakes are activated by a
button on the operator’s console, loss
of hydraulic pressure in the brake
circuit or when the engine is shut
down.
■
Propel pump is destroked when
parking brake is engaged. Propel
lever must be returned to neutral after
brake is released before machine will
propel.
Conveyor System
■
Collecting conveyor features 32 mm
(1.25") high cleats and is driven by a
high torque hydraulic motor to ensure
maximum production and clearing
out the rotor housing effectively.
■
Variable belt speed control for
collecting and front loading
conveyors controls loading of milled
materials to closely match material
type and amount.
■
Both conveyor belts can be reversed
for quick clean out.
■
Hydraulically folding front loading
conveyor facilitates machine
transportation.
■
Upper aluminum covers on loading
conveyor helps avoid material
spillage and wind blown fine
materials.
Collecting Conveyor
Width
800 mm
31.5"
Speed
300 mpm
985 fpm
Upper Conveyor
Width
800 mm
31.5"
Speed
300 mpm
985 fpm
Swing (from center)
48 degrees
Electrical
The 24-volt electrical system consists
of two maintenance-free Cat batteries.
Electrical wiring is color-coded,
numbered and labeled with component
identifiers. The starting system provides
1365 cold cranking amps (cca). The
system includes a 100-amp alternator.
Weights
Operating Weights
Machine
30 900 kg
68,135 lb
on front tracks
16 100 kg
35,500 lb
on rear tracks
14 800 kg
32,635 lb
Weights shown are approximate and include coolant, lubricants, full fuel tank, full
water tank and a 75 kg (165 lb) operator.
Shipping Weights
Machine
28 000 kg
61,740 lb
on front tracks
12 650 kg
27,895 lb
on rear tracks
15 350 kg
33,845 lb
Weights shown are approximate and include coolant, lubricants, 50% fuel level and
empty water tank.
PM-200 specifications