Grade and slope control, Conveyor system, Hydraulic system – Milton CAT PM 201 User Manual
Page 13: Service refill capacities, Water spray system, Electrical, Frame
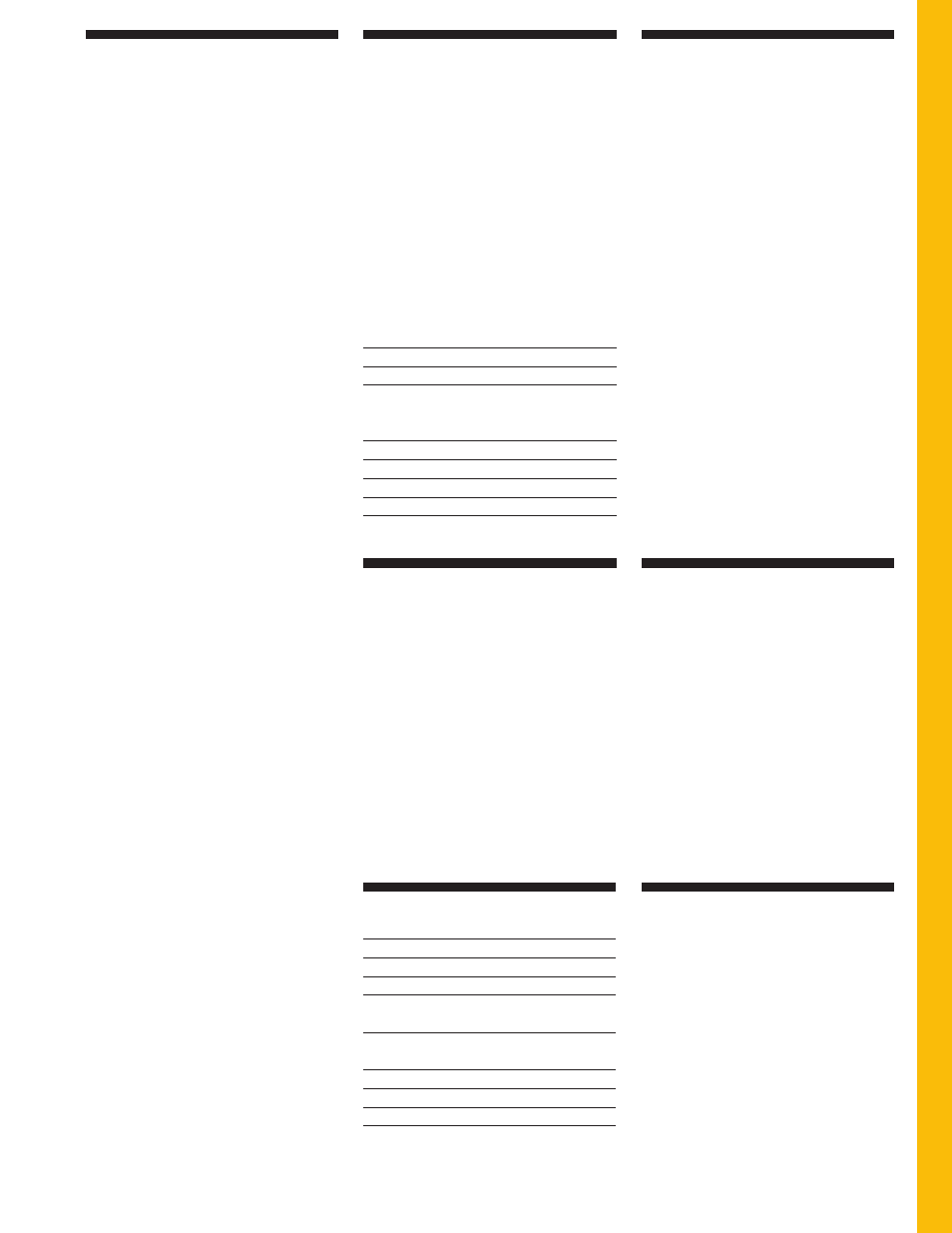
13
PM-201 specifications
Service Refill Capacities
Liters
Gallons
Fuel tank (useable)
946
250
Cooling system
80
21.1
Engine oil w/filter
64
17
Propel planetary
gear reducer (each)
4.2
1.1
Rotor planetary
gear reducer
14
3.7
Rotor mandrel coolant
307
81
Hydraulic tank
180
47.5
Rotor clutch sump
45
11.9
Water spray system
3787
1000
Grade and Slope Control
Machine elevation – rotor depth and
cross slope controlled manually by
operator is standard. Automatic rotor
depth and slope control is optional and
features electronic over hydraulic
control. System can be configured with
contacting or non-contacting grade
sensors. Slope sensor adds versatility.
Features
■
Machine elevation controls located on
the operator’s console and at ground
level allows rotor depth and cross slope
to be controlled manually. Visual depth
gauge displays depth of cut.
■
The optional AUTOMATIC grade
and slope control automatically
controls rotor depth and cross slope to
a preset cutting depth. Setting cutting
depth is easily accomplished first in
manual mode by using the adjustment
knob on the controller.
■
Remote mounted control boxes allow
manual or automatic operation from
either the operator’s station or at
ground level. A cross communication
function allows the operator to view
and change settings of control boxes
located on the opposite side of the
machine. This allows operators a
means to control both sides of a job
from a single location. Constant read-
out for rotor depth and cross slope
are easily visible in direct sunlight.
■
Sonic grade control sensors can be
positioned on each side are easy to
position and provides a consistent
accuracy to ± 3 mm (1/8").
■
Wire rope contacting grade sensor
measures side plate movement that
enables the entire length of the side
plate to become a mini averaging ski
for optimum grade matching.
■
Sonic Averaging System features
three non-contacting grade sensors or
a combination of one contacting and
two non-contacting sensors that
mount on the side of the machine.
Enables the entire length of the
machine to become an averaging
device. Eliminates the need for a
contact type ski for greater machine
maneuverability.
■
Remote mounted control boxes and
sonic grade sensors can be easily
removed and securely stowed to
prevent damage or theft.
Hydraulic System
■
Pumps for propel, rotor drive,
collecting and upper conveyors,
auxiliary hydraulics and cooling fan
are installed on the engine mounting
pad.
■
Hydraulic oil cooler located at the
rear of the machine and arranged in a
modular stacked design for efficient
cooling and easy access for cleaning.
■
Three-micron filtration on pressure
side of auxiliary flow, seven-micron
filtration on return side.
■
Quick-connect hydraulic test ports
simplify system diagnostics.
Water Spray System
■
Hydraulically-driven centrifugal
pump supplies water to spray nozzles
for dust control and collecting belt
lubrication.
■
Centrifugal pump is rated at 206
L/min (55 gpm) at 276 kPa (40 psi).
■
Water spray nozzles focuses the
water spray in a flat fan pattern to the
rotor for better cooling of cutting
tools.
■
Nozzles are easily removed for
inspection and replacement without
the need for tools.
■
Automatic water spray system
operates only when the rotor is
engaged and machine is moving
forward to conserve water.
■
System includes gauges to monitor
water pressure, replaceable filters, a
low water level indicator and water
control valves to conserve water
usage.
■
Water tank can be filled from the top
of the machine or at ground level.
Conveyor System
■
Collecting conveyor is driven by two
high torque hydraulic motors to
ensure even belt tracking and clears
out the rotor housing effectively.
■
Variable belt speed for front loading
conveyor controls loading of milled
materials to closely match material
type and amount.
■
Boost function increases material
handling to load long tractor trailers.
■
Raise, lower and swing controlled
from the operator’s station and at two
ground level control stations.
Collecting Conveyor
Length
3.74 m
12' 3"
Width
1020 mm
40"
Speed
189 mpm
620 fpm
Upper Conveyor
Length
8.31 m
27' 3"
Width
915 mm
36"
Max. speed
231 mpm
760 fpm
Speed w/boost
293 mpm
960 fpm
Swing (from center)
45 degrees
Electrical
The 24-volt electrical system consists
of two maintenance-free Cat batteries.
Electrical wiring is color-coded,
numbered, wrapped in vinyl-coated
nylon braid and labeled with
component identifiers. The starting
system provides 1365 cold cranking
amps (cca). The system includes a
100-amp alternator.
Frame
Fabricated from heavy gauge steel
plates and structural steel tubing. Track
assembly features track frame stops to
limit track angles to provide machine’s
ability to propel up inclines and out of
deep cuts. Top of deck and steps
features non-skid treads for sure
footing.