Engine, Propel system, Rotor drive system – Milton CAT PM 201 User Manual
Page 11: Rotor housing, Rotor options, Pm-201 specifications
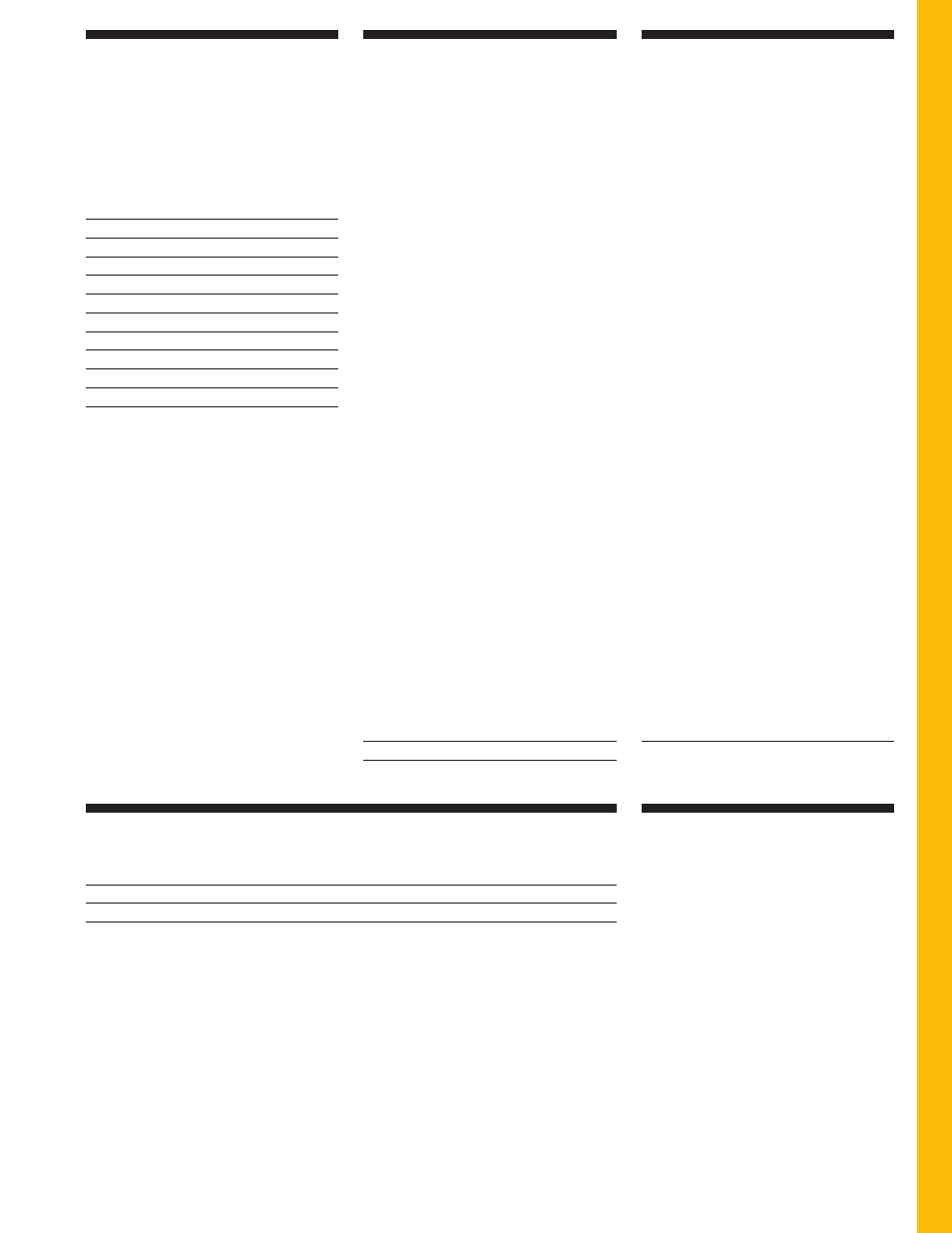
11
Engine
The Caterpillar
®
C18 engine with
ACERT
®
Technology is a six cylinder,
turbocharged air-to-air after-cooled
diesel engine. The engine meets U.S.
EPA Tier 3 and European EU Stage IIIa
engine emission regulations.
Engine
Cat
®
C18
Gross Power
kW
hp
485
650
SAE J1995
483
648
Net Power
kW
hp
ISO 9249
466
625
EEC 80/1269
466
625
SAE J1349
461
618
Specifications
Bore
145 mm
5.7"
Stroke
183 mm
7.2"
Displacement
18.1 liters 1105 in
3
■
The power ratings apply at a rated
speed of 2100 RPM when tested
under the reference conditions for the
specific standard.
■
The net power advertised is the
power available at the flywheel when
the engine is equipped with an
alternator, air cleaner, muffler and fan
at minimum speed.
■
The net power at the flywheel when
the fan is at maximum speed is 445
kW (597 hp) per the SAE J1349
reference standards.
■
Derating is not required up to an
altitude of 2134 m (7000').
■
Dual fuel filters with water separator
and air compressor are standard.
Propel System
Hydrostatic drive with hydraulic flow
provided by a variable displacement
piston-type pump. Drive motors with
planetary gear reduction on each track
provides balanced tractive effort.
Features
■
A variable displacement, piston-type
pump with electronic displacement
control supplies pressurized flow.
■
Positive traction control valve
provides equal hydraulic oil flow to
each drive motor to increase tractive
effort in hard or deep cuts. Operator
can activate by a switch on the
operator’s console.
■
Drive motors have two swashplate
positions allowing operation at either
maximum torque for work or greater
speed for moving around the job site.
■
Gear selection controlled electrically
by a two-position switch on the
operator’s console.
■
Infinitely variable machine speed and
direction of travel controlled by
propel lever.
■
Load sensing system, controlled by
Electronic Control Module (ECM),
matches propel speed to load on the
engine.
■
Tracks are 2045 mm (80.5") long,
348 mm (14") wide and feature
replaceable, steel reinforced
polyurethane track pads for long life.
Max. Speeds (forward and reverse):
Operating
40 mpm - 132 fpm
Travel
6.0 km/h - 3.7 mph
Rotor Drive System
Operates direct through a hydraulically
actuated, Caterpillar wet clutch driving
a Caterpillar planetary gear reducer
located inside the rotor mandrel.
Features
■
Heavy-duty wet clutch mounts
directly to the engine. Hydraulically
actuated by a ON/OFF switch on the
operator’s console.
■
The rotor clutch system has a separate
oil sump, pump, filter, clutch control
valve and oil cooler to provide
continuous cooling and lubrication.
■
Upper and lower sheave bearings are
continuously lubricated with oil from
the clutch sump to provide long life.
■
One eleven-rib high tensile strength
drive belt drives the rotor through a
drum drive gear reducer located
inside the rotor mandrel.
■
The Caterpillar D8 Track-type-Tractor
drum drive gear reducer provides
reliability and long service life.
■
The rotor mandrel is partially liquid-
filled to dissipate heat and cools the
drum drive gear reducer.
■
Input shear shaft protects rotor drive
components from severe shock loads.
■
Hydraulically powered automatic
drive belt tensioner prevents slipping
and reduces maintenance.
■
Single caliper with dual disc brake
installed on PTO output drive shaft.
Rotor Speed:
@ 2100 engine rpm
98 rpm
Rotor Options
Three rotor styles are available. All mount to the standard rotor chamber.
Rotor
Width
Diameter
Tools
Max. Depth
Conical
2100 mm (83")
1168 mm (46")
190
305 mm (12")
Breakaway
2100 mm (83")
1168 mm (46")
170
305 mm (12")
Weld-on
2100 mm (83")
1168 mm (46")
147
305 mm (12")
Rotor Housing
■
Large discharge opening clears out
the rotor housing fast for increased
production and reduced tool wear.
■
Side plates have replaceable bolt-on
carbide wear strips front and rear and
features wear-resistant skis for
reduced wear and longer service life.
■
Floating moldboard with adjustable
down pressure is standard and
features a carbide replaceable cutting
edge.
■
A panel on the rear door can be
removed to windrow the milled
material directly behind the machine.
■
Height control for rotor door located
at operator’s station and at two
ground level control stations.
PM-201 specifications