Blade structure, Types of blades, Teeth shape – Wilton FK350-4 User Manual
Page 16
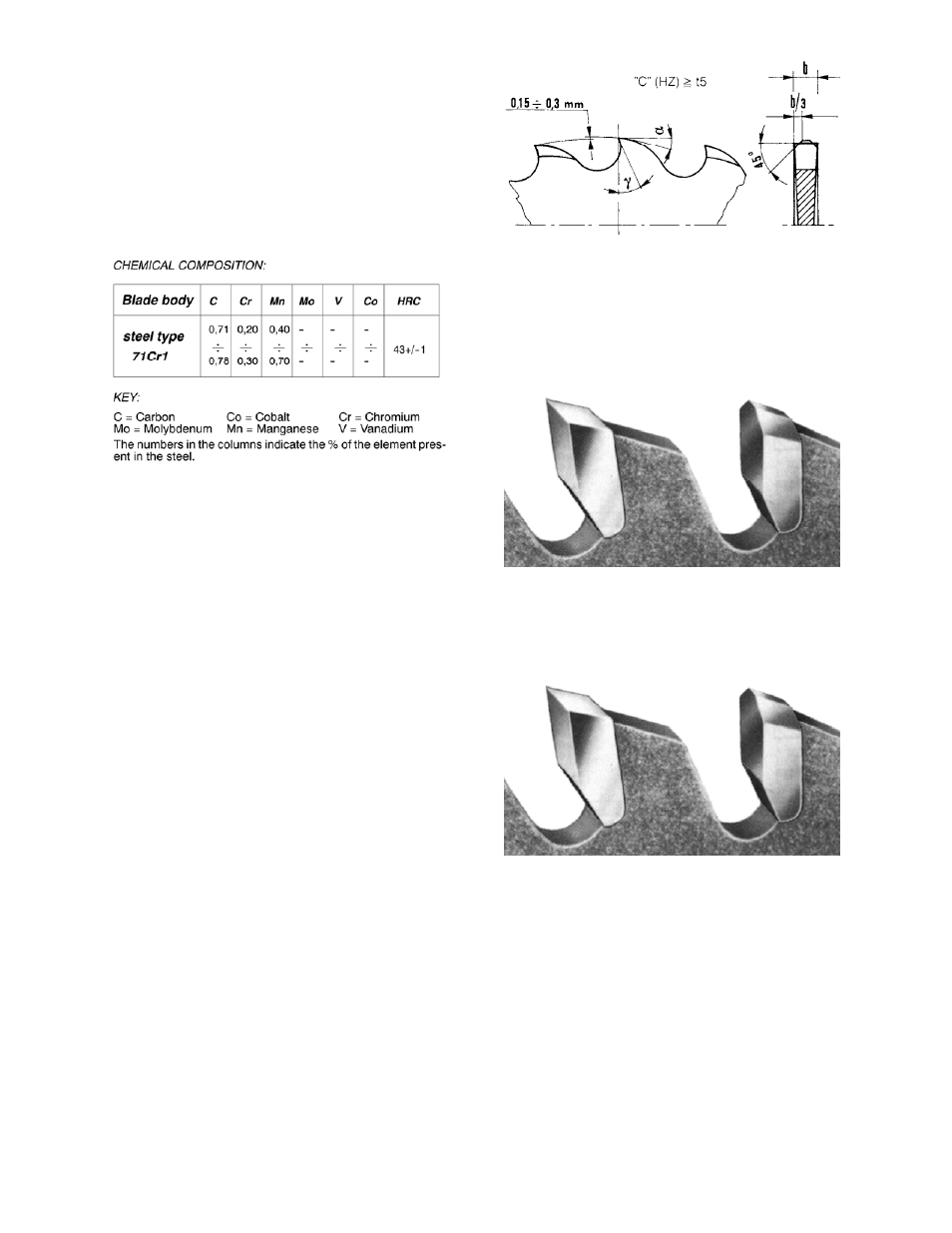
16
Blade Structure
For non--ferrous metals, it is common to use
circular saws with brazed hard metal HM cutting
edge, consisting of a disc made of alloy tool
steel (71Cr1) on which the shape of the teeth
and the seats for the cutting edges are made of
Widia K10. These saws have shown excellent
wear resistance but low resistance to impact,
which is in any case a minor problem with non-
ferrous materials.
Table 2
Types of Blades
The blades fitted to the FK350 and FK350-2SX
have dimensions 350 x 32 x 2.5 mm and are of
HM hard steel type since the machine is to be
used for cutting non-ferrous materials. In
addition to the size and pitch of the teeth,
however, the blades also have different
geometric characteristics in accordance with
their particular use:
tooth cutting angle – may be negative or
positive
tooth sharpening –may be BW
with an
alternate raked tooth or C with a roughing tooth
raked on both sides and a non--raked finishing
tooth
tooth pitch – the distance between the crest of
one tooth and the crest of the next tooth (tooth
pitch = T)
Teeth Shape
”C” TYPE SHARPENING (HZ)
Coarse toothing with roughing tooth raked on
both sides and non--raked finishing tooth. The
roughing tooth is about 0.3 mm higher.
Coarse toothing with roughing tooth and
finishing tooth. Used in saws with pitch greater
than or equal to 5 mm for cutting ferrous and
non-ferrous materials with solid or solid-profiled
sections.
Figure 14
”BW” TYPE SHARPENING DIN 1838--UNI 4014
Coarse toothing with teeth alternately raked to
the right and left.
Toothing generally used on cutting-off machines
for cutting ferrous and alloy materials with
tubular and profiled sections.
Figure 15
POSITIVE AND NEGATIVE CUTTING ANGLES
The cutting angle
may vary from positive to
negative depending on the cutting speed, the
profile and the type of material to be cut.
Figure 16
A positive angle determines better penetration of
the tool and hence lower shear stress and
greater ease of sliding for the swarf over the
cutting edge. On the other hand, the cutting
edge has lower mechanical resistance, so as the
breaking load of the material to be cut increases,
the cutting angle decreases from positive until it
becomes negative so as to offer a cutting edge
with a larger resistant section.