1. power switch, 2. inductance control, 3. overload protection – Miller Electric MR-5 User Manual
Page 19: 4. voltmeter, 5. wire speed meter, 6. ammeter, 7. indicator lights, 4 - sequence of operation, 1. input signal from welding power source, Sequence of operation
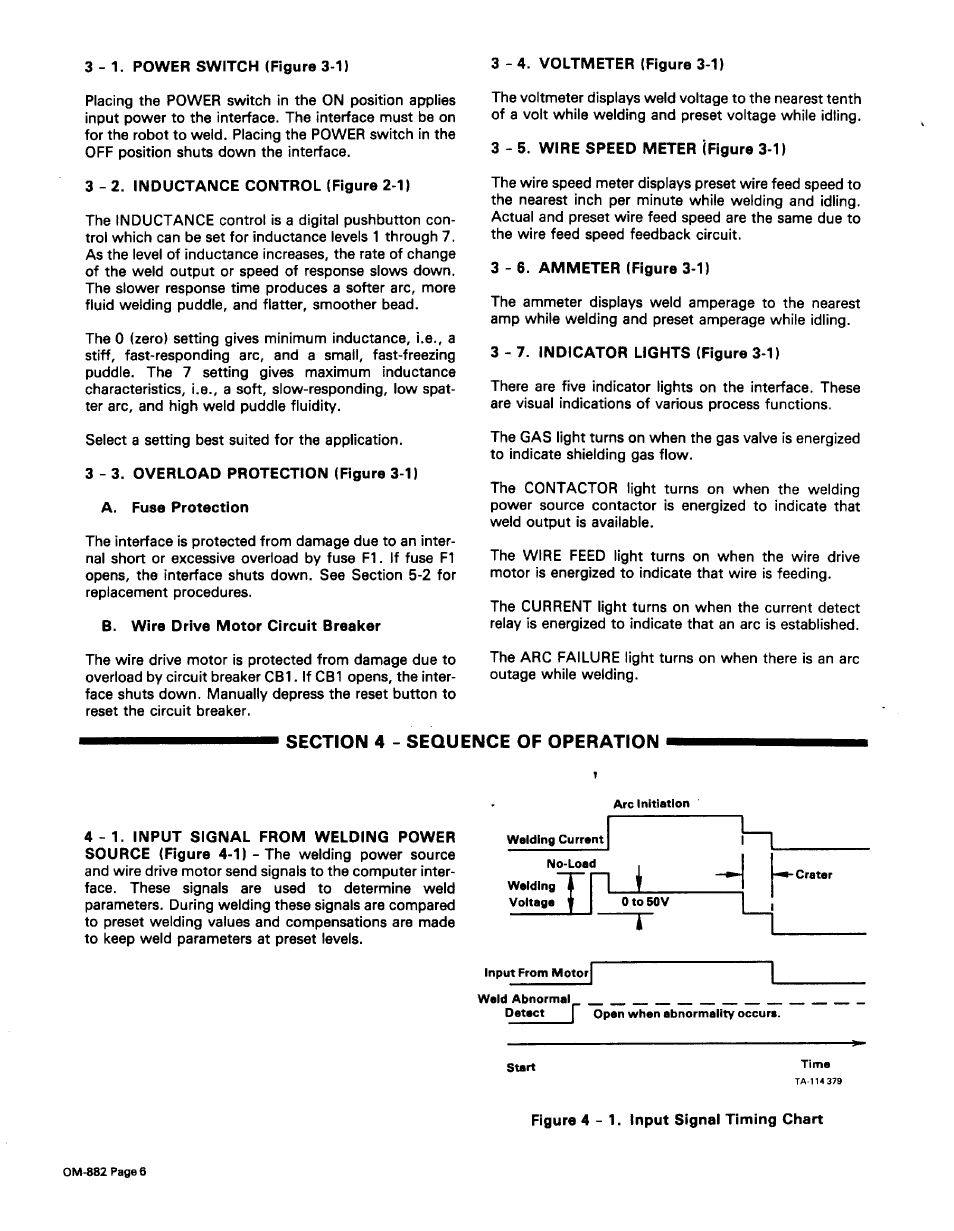
3
-
1. POWER SWITCH (Figure 3-1)
3
-
4. VOLTMETER (Figure 3-1)
Placing the POWER switch in the ON position applies
input power to the interface. The interface must be on
for the robot to weld. Placing the POWER switch in the
OFF position shuts down the interface.
3 -2. INDUCTANCE CONTROL (Figure 2-1)
The INDUCTANCE control is a digital pushbutton con-
trol which can be set for inductance levels 1 through 7.
As the level of inductance increases, the rate of change
of the weld output or speed of response slows down.
The slower response time produces a softer arc, more
fluid welding puddle, and flatter, smoother bead.
The 0 (zero) setting gives minimum inductance, i.e., a
stiff, fast-responding arc, and a small, fast-freezing
puddle. The 7 setting gives maximum inductance
characteristics, i.e., a soft, slow-responding, low spat-
ter arc, and high weld puddle fluidity.
Select a setting best suited for the application.
3
-
3. OVERLOAD PROTECTION (Figure 3-1)
A.
Fuse Protection
The interface is protected from damage due to an inter-
nal short or excessive overload by fuse Fl. If fuse Fl
opens, the interface shuts down. See Section 5-2
for
replacement procedures.
B.
Wire Drive Motor Circuit Breaker
The wire drive motor is protected from damage due to
overload by circuit breaker CB1. If CB1 opens, the inter-
face shuts down. Manually depress the reset button to
reset the circuit breaker.
The voltmeter displays weld voltage to the nearest tenth
of a volt while welding and preset voltage while idling.
3 -5. WIRE SPEED METER (Figure 3-1)
The wire speed meter displays preset wire feed speed to
the nearest inch per minute while welding and idling.
Actual and preset wire feed speed are the same due to
the wire feed speed feedback circuit.
3
-
6. AMMETER (Figure 3-1)
The ammeter displays weld amperage to the nearest
amp while welding and preset amperage while idling.
3
-
7. INDICATOR LIGHTS (Figure 3-1)
There are five indicator lights on the interface. These
are visual indications of various process functions.
The GAS light turns on when the gas valve is energized
to indicate shielding gas flow.
The CONTACTOR light turns on when the welding
power source contactor is energized to indicate that
weld output is available.
The WIRE FEED light turns on when the wire drive
motor is energized to indicate that wire is feeding.
The CURRENT light turns on when the current detect
relay is energized to indicate that an arc is established.
The ARC FAILURE light turns on when there is an arc
outage while welding.
SECTION 4
-
SEQUENCE OF OPERATION
Arc Initiation
4 -1. INPUT SIGNAL FROM WELDING POWER
SOURCE (Figure 4-1)
-
The welding power source
and wire drive motor send signals to the computer inter-
face. These signals are used to determine weld
parameters. During welding these signals are compared
to preset welding values and compensations are made
to keep weld parameters at preset levels.
Welding Current
No-Load
WeldingT~
Voltage
0 to 50V
—F
WeldAbnormal
—
D~LY
Open when abnormality occurs.
Start
Time
TA-i 14 379
Figure 4
-
1. Input Signal Timing Chart
H-
Crater
OM-882 Page6