GE AV-300i User Manual
Page 20
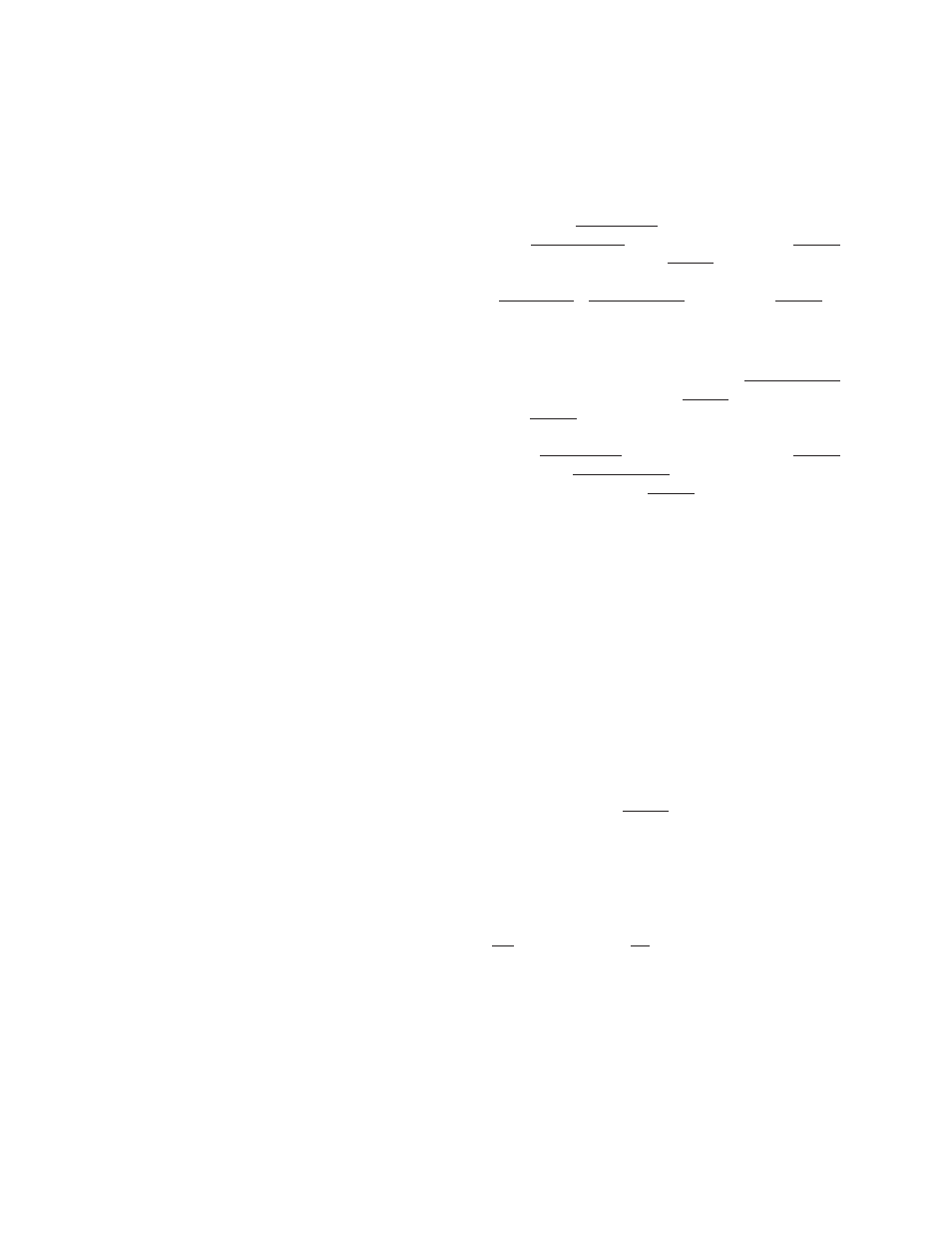
20
NOTE:
“xxx range error” or “timeout” messages may also occur in
some extreme parameter ranges. Repeat the tune in this
case. If error messages are persistent see troubleshooting
section.
If there was some reason you did not want to keep these
values permanently, but only wanted to try to run the drive
with them, there is no need to save them to permanent
memory. If power is cycled however, these values will be
lost unless the “Save Parameter” function is used.
14. Self tune part 3:
The third part of self tuning (Speed regulator tuning)
identifies the total inertia at the motor shaft, the friction
value and computes the proportional and integral gains
of the speed regulator. The motor needs to be free to
turn with load attached to the shaft.
NOTE:
When regulation mode = field-oriented, the encoder needs
to be verified before running Self Tune 3. Refer to page 22
“Encoder Verification”. After this verification procedure, put
the regulation mode back to field oriented.
WARNING !
This procedure requires free rotation of the motor shaft
coupled to the load. The Start/Stop command is
ignored, therefore it can not be used on drives with
limited travel, or when free rotation presen ts a safety
problem.
CAUTION !
The test is performed using the torque limit value set
in Test T curr lim parameter. The torque is applied in a
step fashion, with no ramp profile. Therefore, the
mechanical transmission must not have significant
backlash, and it must be compatible with operation at
the torque limit set in the Test T curr lim parameter.
The user can reduce the torque limit to a suitable value
via the Test T curr lim parameter.
Note !
• Application where the system inertia coupled to the
motor shaft is much higher than the motor inertia value
, increase the Test T curr lim parameter to avoid “Time
out” error.
• This procedure is not suitable for use with “hoist”
or “elevator” drives.
• Encoder feedback is required when Field oriented mode
is selected.
• Set the current limit (BASIC MENU\ T Current lim +/-)
to a value compatible with the motor size and load.
(Example when motor is 1/3 of the Drive power, the
limit should be reduced compared to the default value).
• Select the torque current value to be used during the
test via the Test T curr lim parameter
•
Now press [Left arrow] to see “self tune 2a or 2b”
then [Down arrow] to “self tune 3” and press [Enter]
to Fwd-Rev spd tune, then [Enter]. Set the motor shaft
direction for this test: Forward or Reverse by using
[Up arrow] / [Down arrow] keys. Press [Enter] to
set the selection.
•
Enable the drive using a switch on terminal 12 [and
close terminal 13 to terminal 19 if Speed control
function is enabled (default)]. Press [Down arrow]
to “Start part 3” then press [Enter], “start part 3 ?”
then [Enter] and see “measure speed” will appear and
the motor will turn. Wait until the display says “end”,
press [Left arrow] to see “self tune 3” then [Enter]
and press [Down arrow] to see “take val part 3”.
Disable the drive, then [Enter]. You are now finished
with the initial set up and tuning with values stored in
only in the “working memory”.
NOTE:
“xxx range error” or “timeout” messages may also occur
in some extreme parameter ranges. Repeat the tune in
this case. If error messages are persistent see
troubleshooting section.
NOTE:
If there was some reason you did not want to keep these
values permanently, but only wanted to try to run the drive
with them, there is no need to save to permanent memory.
If power is cycled however, these values will be lost unless
the next step is taken.
To save all values to permanent memory, select Save
parameters and press [Enter] .
15.Set up for Running:
First, before saving, let’s put the drive into the
configuration you want to run it in.
The drive is factory setting to run through the Increase
[+] and Decrease [-] keys (Enable motor pot
parameter = Enabled), see the following instruction to
run.