MK Products CobraMig 260 PS/Feeder User Manual
Page 9
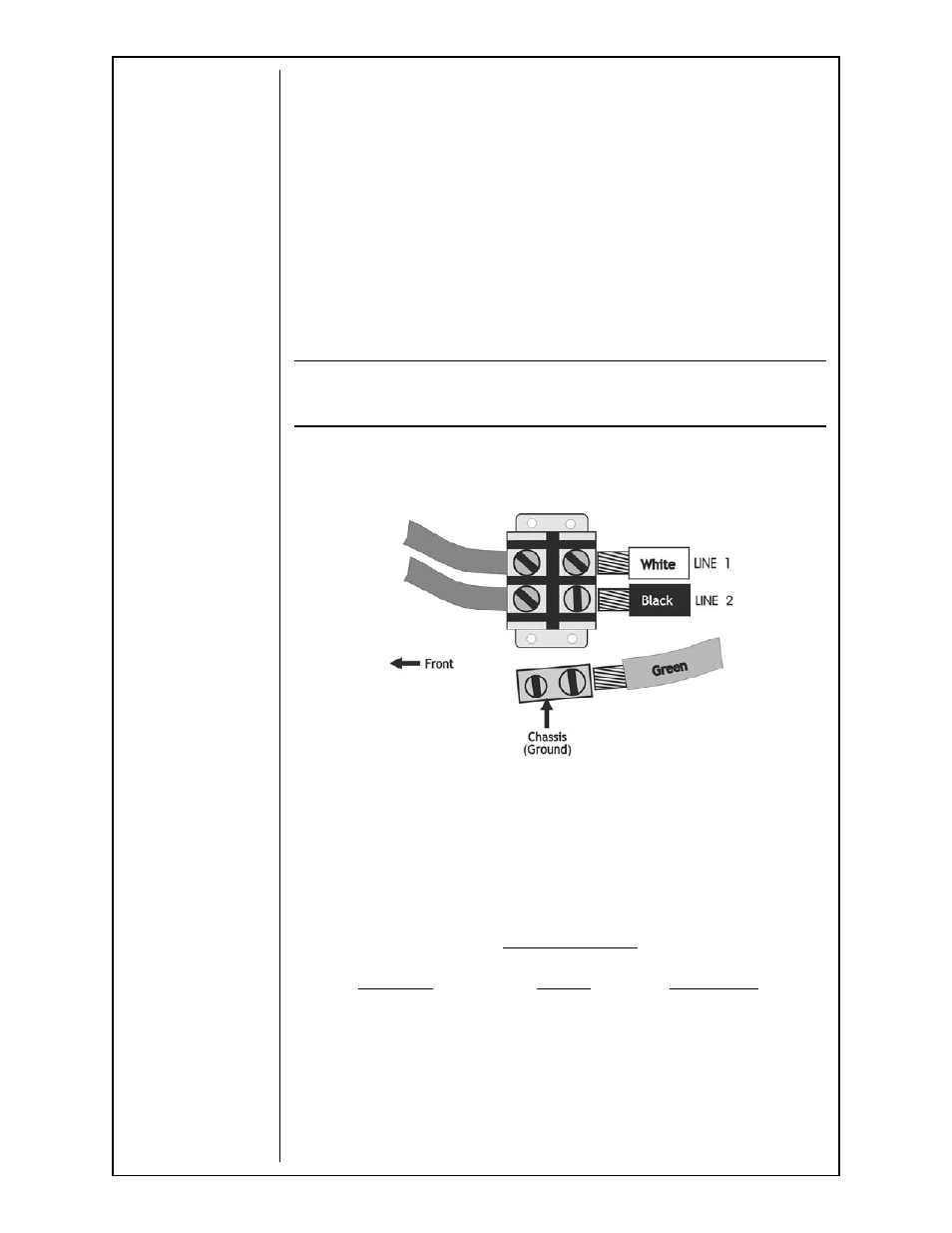
CobraMig 260 Owner's Manual - Page 3
Route input cable through strain relief and connect to power block as shown
in the diagram following. Tighten strain relief and replace side panel with all
hardware removed.
Machine Grounding
Before starting the installation, check with the local power company if there
is any question about whether your power supply is adequate for the voltage,
amperes, phase, and frequency specifi ed on the welder nameplate. Also, be
sure the plannted installation will meet the U.S. National Electrical Code and
local code requirements. This welder may be operated from a single phase
line or from one phase of a two or three phase line.
The CobraMig 260 is supplied connected for 480 Volt input. If the welder
is to be operated on another voltage, it must be reconnected according to
the instrucitons.
WARNING:
Make certain that the input power is electrically disconnected before removing the
screw on the reconnect panel access cover.
A green wire in the input cable connects this contact to the frame of the
welder. This ensures proper grounding of the welder frame when the welder
plug is inserted into the receptacle.
Welding Torch Connections
Work Cable
Connect a work lead of suffi cient size and length (see table below) between
the proper output stud on the power source and the work. Be sure the
connection to the work makes tight metal to metal electrical contact. Poor
work lead connections can result in poor arc initiation, poor weld results and
activation of the ground lead protector.
Work Lead Lengths
Current 60%
Up to 50ft.
10-100ft.
Duty
Cycle
(15.2m)
(15.2-30.4m)
300A
0 (53mm)
0 (67mm)
400A
00 (67mm)
00 (85mm)
500A
00 (67mm)
00 (85mm)
600A
000 (85mm)
000 (107mm)
Control Cable
The 7-Pin “W” Clocked connector screws onto the mating receptacle on the
front panel of the wire feeder. This provides all electrical signals (motor
voltage, potentiometer control & trigger) to and from the feeder to the torch.