MK Products CobraMig 260 PS/Feeder User Manual
Page 12
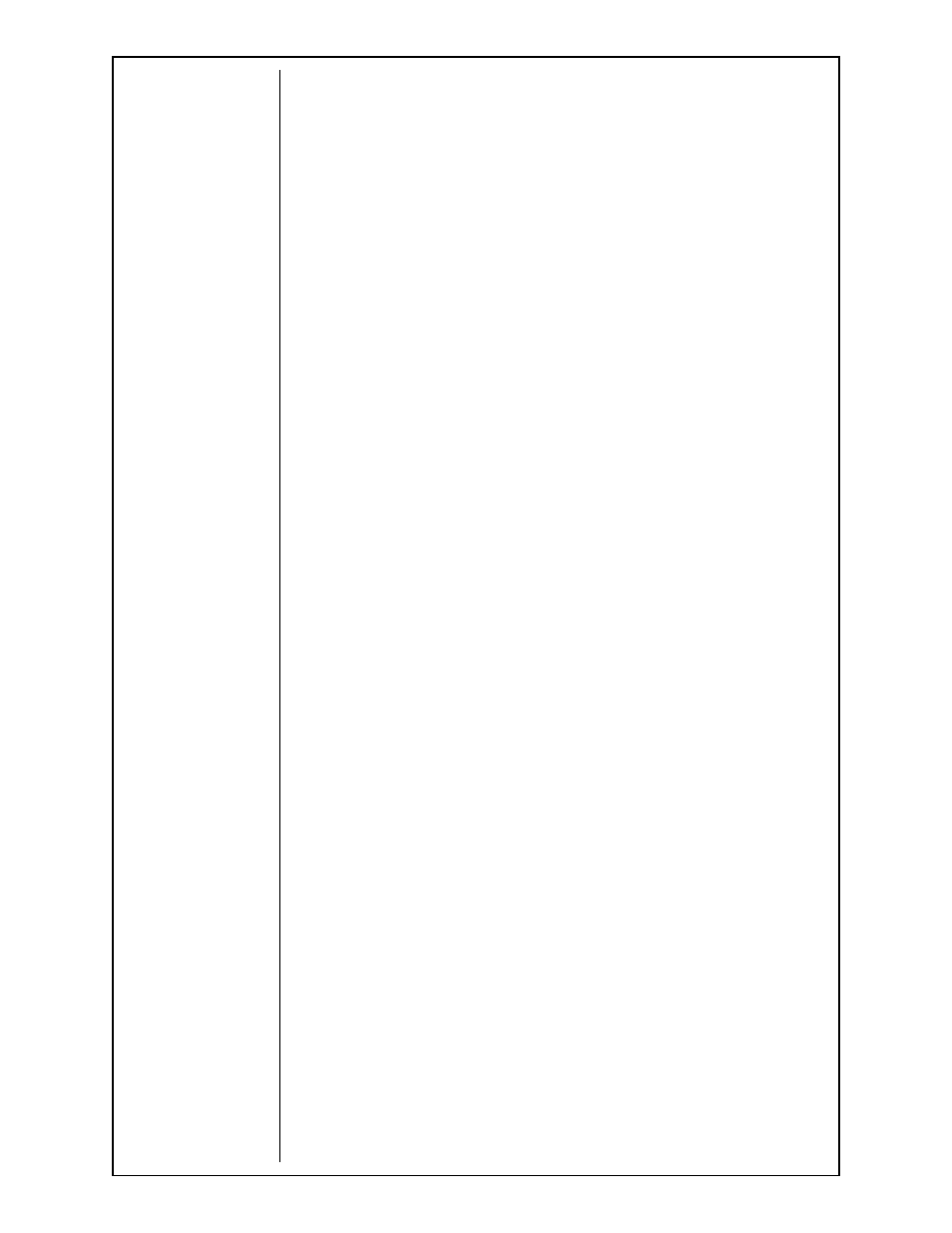
CobraMig 260 Owner's Manual - Page 6
Lower the wire retainer bar onto the spool.
Threading Procedure
Place wire size selector switch on front panel to the correct position for the
wire being used.
Loosen end of wire from spool and cut off any kinked or bent portions.
Unreel and straighten out fi rst 6” to 8” of wire.
Raise wire type lever to center position.
Route wire into inlet guide, along drive roll groove, and into wire conduit.
Flip wire type lever to show type of wire being used: ALUM or STEEL.
Tighten the torch pressure adjusting knob so the wire will be picked up and
fed through the contact tip. Proper tension is achieved when wire does not
slip if a small amount of pressure is added to the wire as it exits the tip.
Wire Retainer Bar
The design of the patented Cobramatic® Wire Retainer Bar performs two
very important and very basic functions of the wire feeder: a) spool drag
tension, and b) wire maintenance on the spool.
The spool drag tension is set by lowering the wire retainer bar onto the wire
inside of the spool. The spring tension of the wire retainer bar applies enough
pressure on the spool so that when the torch trigger is released, engaging the
brake pall, the spool does not overrun kicking wire off the spool.
Wire maintenance on the spool is performed by the applied pressure of the
wire retainer bar spread across the coiled wire on the spool. The replaceable
pad (P/N 437-0255) of the wire retainer bar is designed to hold the wire on
the spool, maintaining the smooth layering of the wire and keeping it from
jumping off, and possibly, electrically shorting to the cabinet chassis.
Section B
Operation
General Description
The CobraMig 260 is a constant voltage (CV) DC welding power supply with
a built-in Cobramatic wire feeder which operates on the same basic principles
as all other Cobramatics. The 115VAC slave motor in the feeder side runs
at a fast, constant speed, but has very low torque. It is always trying to
feed more wire than the torch motor wants, and when the torch motor gets
all it wants, it slows the slave motor to the speed that the torch is running.
Because of the low torque produced by the slave motor, a brake system is
used to prevent wire overrun rather than tension. The drag adjustment in
the spindle is used to keep the wire slightly taut, so it will not unspool while
feeding wire. The high torque 24VDC torch pull motor is controlled by a
solid state speed control, located on the main board, and the potentiometer
located on the torch.
The lower portion of the unit houses the power supply components. Power
supply controls include a range switch and a variable voltage control.
Controls and Settings
ON/OFF SWITCH
Placing the switch in the “ON” position energizes the power supply and places
the unit in the ready-to-weld status. The power indicator light should be on
at this time.