Fig.1 fig.2 – Sealey MS100 User Manual
Page 2
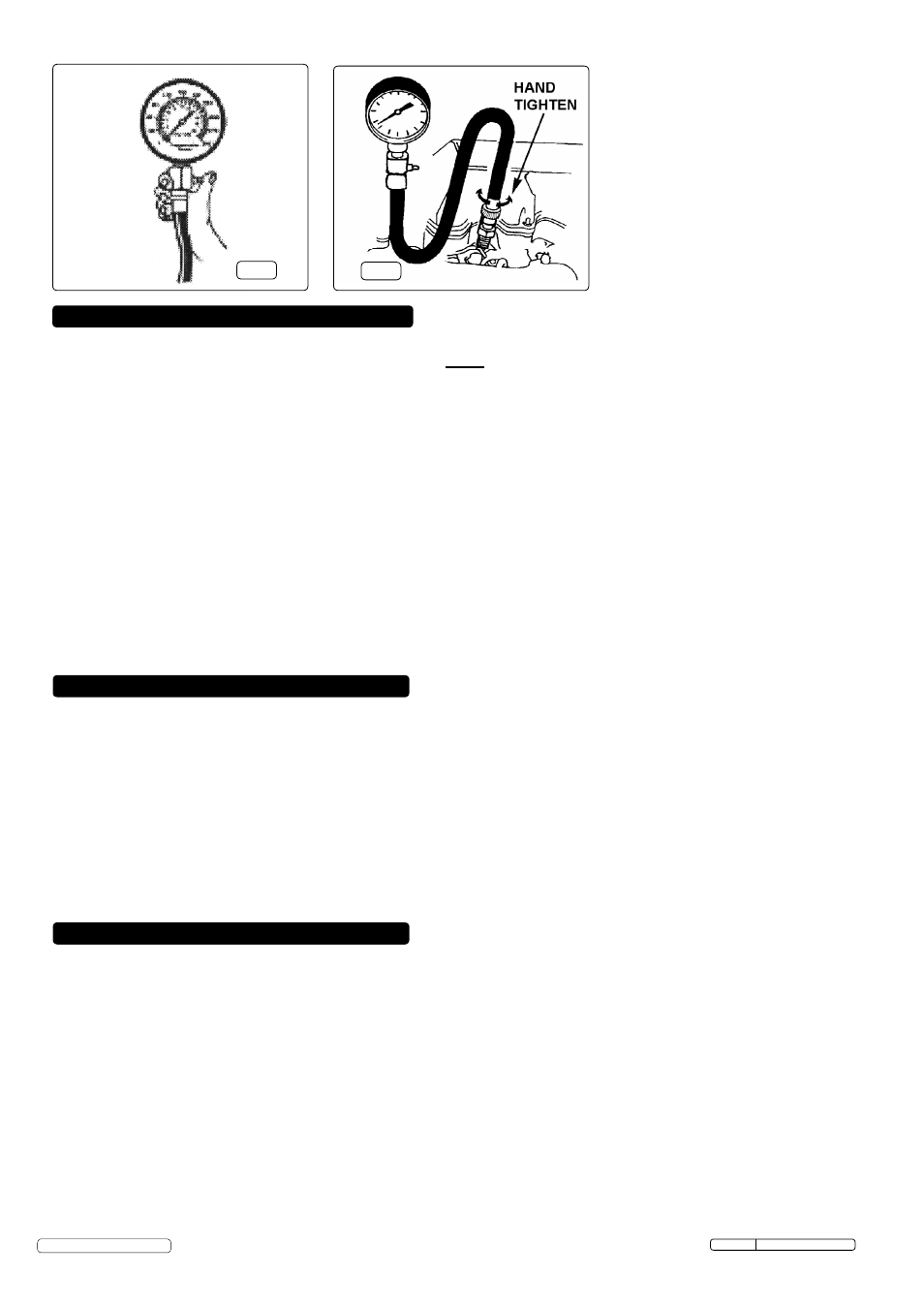
3. OPERATION
3.1
Procedure for Compression Test
WARNING! Always release the pressure via the Release Valve before disconnecting the tester.
Press the release valve slowly to release the pressure gradually. Refer to Fig.1.
NOTE! A variation in compression readings between cylinders is often a better indication of engine problems than the absolute
values of compression.
3.2
Run the engine until it reaches the normal operating temperature.
3.3
Stop the engine and disconnect all spark plug wires, numbering them according to the cylinder to which they were
connected.
3.4
Loosen all spark plugs by about half a turn, but do not remove them.
3.5
Using an air hose or wire brush, remove all the dirt and debris from the spark plug wells.
3.6
Remove the spark plugs and place them on a clean, flat surface in the cylinder order in which they were removed.
3.7
Remove the air filter.
3.8
Disconnect the ignition system, following the manufacturer’s recommendations in the vehicle servicing manual.
3.9
Select the spark plug adaptor required for the vehicle. Screw the adaptor to the hose. Screw the spark plug adaptor and hose assembly into
a spark plug well. Hand tighten only.
DO NOT use a wrench. Refer to Fig.2.
3.10 Connect the coupling on the gauge to the hose. Ensure the coupling is fully engaged.
3.11 Crank the engine for at least five compression strokes, or until the pressure reading on the gauge stops rising, with the throttle in the wide
open position.
3.12 Record the compression reading, then push the side release valve to relieve the pressure.
3.13 Repeat the test and record the reading. Relieve the pressure and remove the hose and adaptor from the spark plug well.
3.14 Repeat for the remainder of the cylinders.
4.1
Compression Gauge Readings
4.2
On a normal cylinder, the gauge needle should travel up the scale on each compression stroke until it reaches peak value. All cylinders
should indicate a pressure that is within the vehicle manufacturer’s specifications, and the reading should not vary by more than 10% from
cylinder to cylinder.
4.3
If the gauge needle does not travel up the scale or if it remains at the same value for several strokes and then starts to climb, the problem
could be a valve sticking.
4.4
If the compression reading is considerably higher than the vehicle manufacturer’s specification, the problem may be carbon build-up in the
cylinder. It may also indicate that either the piston, or the cylinder head, has been modified.
4.5
If a reading on two adjacent cylinders is 20psi (or more) lower than the other cylinders, the problem may be a cracked cylinder head or
defective main gasket. Under these conditions, both coolant and oil may be found in both cylinders.
4.6
If the readings are low, or vary widely between cylinders, pour a teaspoon of SAE 30 oil into each cylinder and retest them. If the readings
increase considerably, the problem may be poorly seated, or worn, piston rings. If the readings remain about the same, the valves and/or
associated components may be the problem. A burned or damaged piston may also cause the same results.
5.
COMPLETION OF TEST
4.
TEST RESULTS
5.1
Clean, re-gap and reinstall the spark plugs in the same order in which they were removed, or install new spark plugs.
5.2
Reconnect each spark plug wire to the plug it was connected to prior to removal.
5.3
Return the throttle plates to the closed position.
IMPORTANT: After test, failure to return the throttle plates to the closed position before
starting the engine can cause serious damage to the engine.
5.4
Reconnect the ignition system wiring disconnected in paragraph 3.8.
Fig.1
Fig.2
Original Language Version
© Jack Sealey Limited
MS100 Issue 2 (P) - 17/07/13