HEIDENHAIN TNC 620 (81760x-01) ISO programming User Manual
Page 388
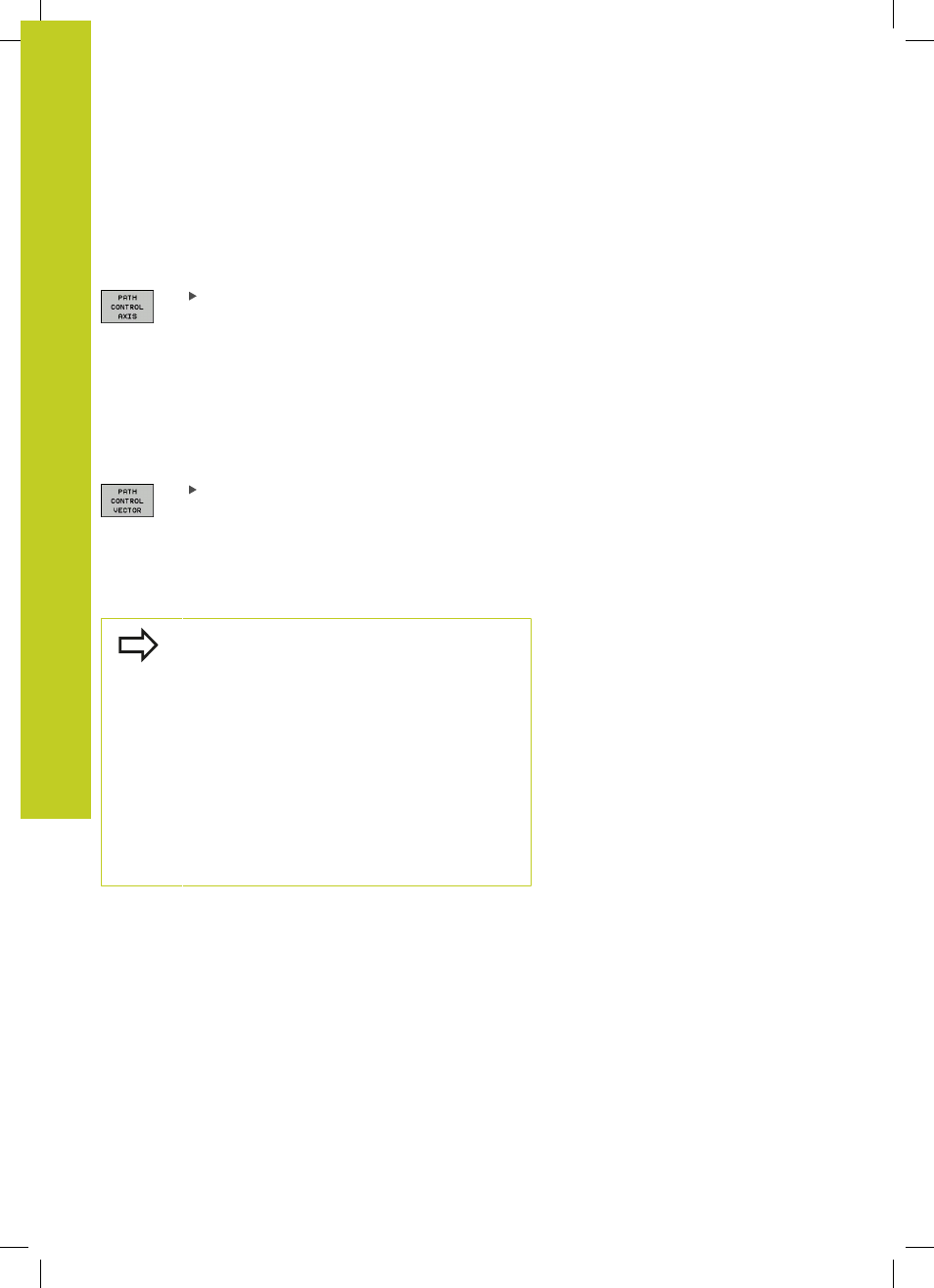
Programming: Multiple Axis Machining
12.5 FUNCTION TCPM (software option 2)
12
388
TNC 620 | User's Manual for DIN/ISO Programming | 3/2014
Type of interpolation between the starting and end
position
The TNC provides two functions for defining the type of
interpolation between the starting and end position:
PATHCTRL AXIS determines that the tool point
between the starting and end position of the
respective NC block moves on a straight line
(Face Milling).
The direction of the tool axis
at the starting and end positions corresponds
to the respective programmed values, but the
tool circumference does not describe a defined
path between the starting and end positions.
The surface produced by milling with the tool
circumference (
Peripheral Milling
) depends on
the machine geometry
PATHCTRL VECTOR determines that the tool
tip between the starting and end position of
the respective NC block moves on a straight
line and also that the direction of the tool axis
between starting and end position is interpolated
so that a plane results from machining at the tool
circumference (
Peripheral Milling
)
With PATHCTRL VECTOR, remember:
Any defined tool orientation is generally accessible
through two different tilting angle positions. The TNC
uses the solution over the shortest available path—
starting from the current position.
To attain the most continuous multiaxis movement
possible, define Cycle 32 with a
tolerance for rotary
axes (see Touch Probe Cycles User's Manual, Cycle
32 TOLERANCE). The tolerance of the rotary axes
should be about the same as the tolerance of the
contouring deviation that is also defined in Cycle
32. The greater the tolerance for the rotary axes is
defined, the greater are the contour deviations during
peripheral milling.