Watson-Marlow 605Di User Manual
Page 6
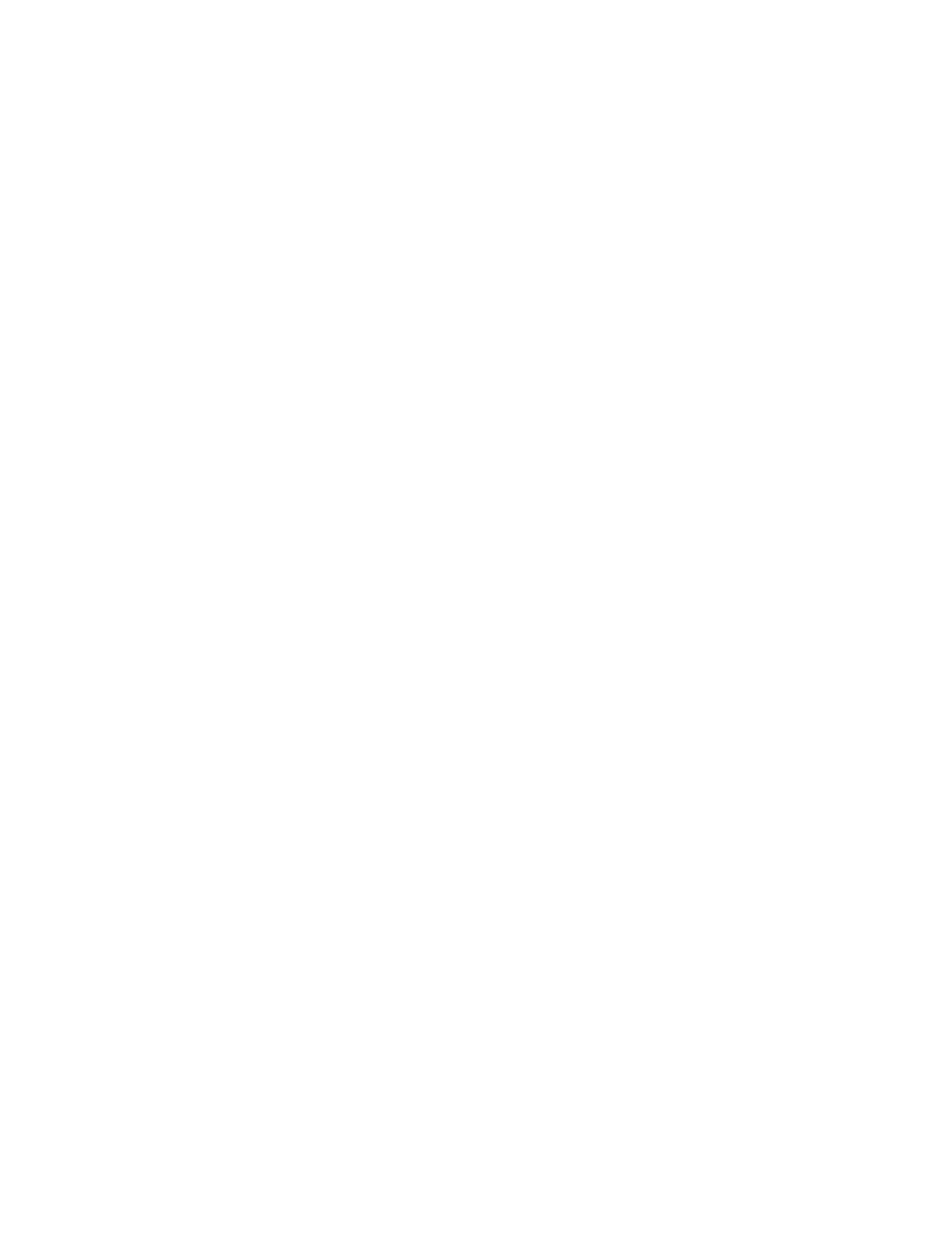
5
User interfacing
When powering up the pump the user will be taken into the main menu.
Use the Step key to move between menu options. Use the Enter key to confirm settings. Use the number keys to enter in
settings. Use the ¿ or À key to increase or decrease set values in the pump software i.e. ramp settings, date, rpm etc.
Dose permits the set-up of dose programs for dispensing. A dose can be initiated by using the Start button or external switching.
The pump will allow up to 26 dosing programs to be stored and recalled at any time. A printer can be connected to the pump for
recording of dispense runs. Batch and operator codes must be entered when using a printer.
Cal allows the pump to be calibrated for accurate dosing.
Manual allows continuous transfer/fluid metering via keypad control.
Auto enables analogue or RS232 control.
Setup displays and controls the user and factory settings for the correct operation of the pump.
The speed/volume flow rate of the drive is governed by the pumphead and tubing selected.
Dosing procedure
The Dosing program is outlined in the technical data section of the operating instruction in a flow chart format. Each step in the
procedure is described to provide full understanding of the procedure.
Within the technical data section are mean values for dose time guidelines and accuracy figures recorded using Silicone tubing at
zero suction and pressure. For the highest accuracy use small bore tubing and maximum roller passes. Always use a calibration
dose to ensure the highest accuracy possible.
Print audit routines
If a printer is connected, the completion of a dose run will automatically call the print routine. The first request will be to enter the
operator ID.
Up to 16 characters can be entered. Digits and the decimal point are entered directly from the keypad. Alpha characters are entered
by pressing ¿ or À which call A to Z and Z to A respectively in circular rotation.
An alpha character is embedded by pressing Step. A numeric character is entered by pressing Step, any other numeric
character, the decimal point or ¿ or À.
On pressing Enter, the pump will request the input of a batch number.
Again, up to 16 characters can be entered as for the operator ID. When Enter is again pressed, the following information is printed
out: date, time, dose size, specific gravity, dose interval, number of doses, initial ml/rev, recalibration data, operator ID, batch
number and number of doses delivered.
Following the print out a repeat dose option will be given.
Single dose command
Single doses can be dispensed on demand, with a count of the number of doses being kept.
Set the interval time to 0 SECONDS and the number of doses to 1.
To start single dosing, press Start or use an external start dose switch. The display will indicate the total number of completed
doses up to a maximum of 99,999 after which the counter will restart at 0, so that dose 100,001 would be shown as 1.
Calibration procedure
Calibration of the 605Di is based on informing the pump under Cal of the pumphead and tubing which are to be used. Alternatively
a calibration dose can be used. The calibration dose will run for a maximum of 4 minutes, but can be stopped at any time up to 4
minutes. The longer the calibration dose the more accurate the calibration. Entering into the pump the physical volume or mass to
complete the procedure and will allow the pump to take into account ambient conditions and also the viscosity of the fluid.
Manual operation
•
Switch power on.
•
Change the set speed by pressing the ¿ or À key. The minimum speed of the 605Di is 4 rpm.
•
Change direction by pressing the CW/CCW key. Indication of direction of rotation is provided via the LCD display.
•
Select the maximum speed: press the ¿ key and the Max key together. Select the minimum speed: press the À key and the
Max key together.
•
Press Start to start the pump. Press Stop to stop the pump.
Auto
The pump will accept external control signals through the 25 pin cage clamp connector on the back panel. Remove the cover plate
ensuring that the gasket is not damaged. Feed the control wires through the cable glands and connect via the sprung cage clamps.
Analogue
This function enables the pump speed to be controlled via an external analogue process signal. Pressing Enter at analogue will call
a confirmation of the analogue control signal settings. These can be reset under Setup (see section covering pump setup).
RS232