Ethernet communication module dvpen01-sl, 13 application of modbus tcp master – Delta DVPEN01-SL User Manual
Page 55
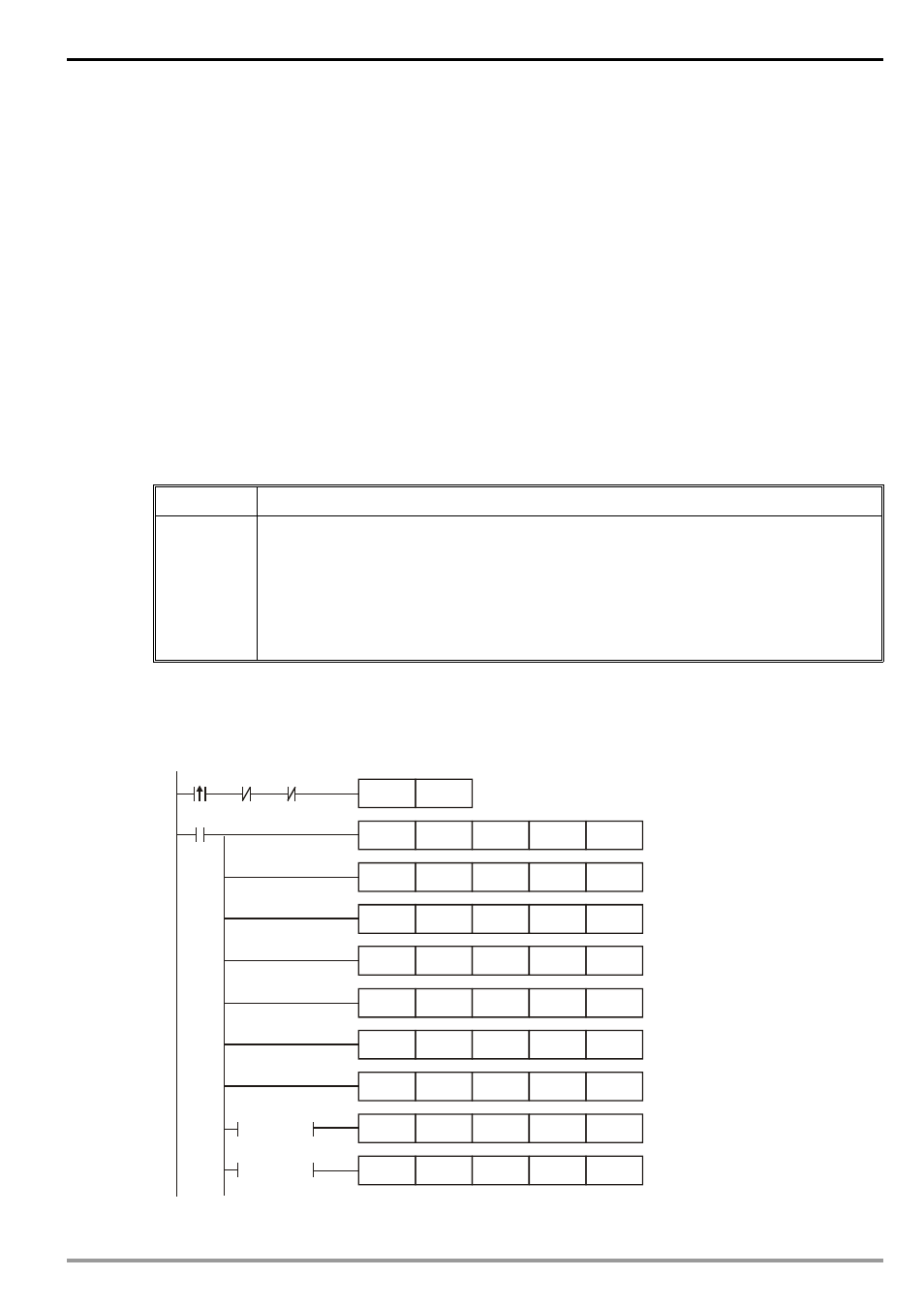
Ethernet Communication Module DVPEN01-SL
DVP-PLC Operation Manual
53
•
Write “0” into CR#28, and PLC_B will use CR#25 ~ CR#26 as the IP address of the destination
PLC.
•
Write the IP address of PLC_A into CR#25 and CR#26. The first two IP codes (192.168 =
H’C0A8) should be written into CR#26, and the last two IP codes (0.4 = H’0004) into CR#25.
•
Write the Modbus address of D0 (H’1000) in PLC_A into CR#81 and CR#84.
•
Write the Modbus address of D100 (register of RTC) (H’1064) into CR#86.
•
Write the number of registers K7 into CR#85.
•
Write “1” into CR#13 to start the data exchange.
•
CR#14 = 2 refers to successful execution. CR#14 = 3 refers to failed execution.
•
Once the data exchange is successful, the values in D1313 ~ D1318 in PLC_B will be written into
D0 ~ D6 of PLC_A.
6.13 Application of Modbus TCP Master
Application
Compiling Modbus instruction by PLC_B, making Y0 of PLC_A flashing
Network
requirement
(1) Adopt static IP.
(2) IP of PLC_A: 192.168.0.4
(3) IP of PLC_B: 192.168.0.5
(4) Update from PLC_B to PLC_A
(5) Use Modbus instruction 050500FF00 to set “On” Y0.
(6) Use Modbus instruction 0505000000 to set “Off” Y0.
(7) Y0 goes between On/Off once every one second.
1. See 6.1 for how to set up the communication.
2. Compile the ladder diagram in the MPU and download it to PLC_B. See below for the program design.
We do not need to write any corresponding ladder diagram into PLC_A.
M1013
K100
K1
K100
K100
K1
M2
M1
M1
SET
M1
TOP
TOP
TOP
K100
TOP
K1
H4
HC0A8
K1
H0
K100
K100
K1
TOP
TOP
K100
TOP
K1
K1
K1
H0
H5
H5
K100
TOP
K1
K100
TOP
K1
H0
HFF
K118
K117
K111
K120
K121
K122
K123
K124
K124
= D0 K0
= D0 K1