Thermocouple measurement accuracy, Cold-junction temperature measurement accuracy, Minimizing thermal gradients – Measurement Computing USB-2001-TC User Manual
Page 11: Data linearization, Mechanical drawings
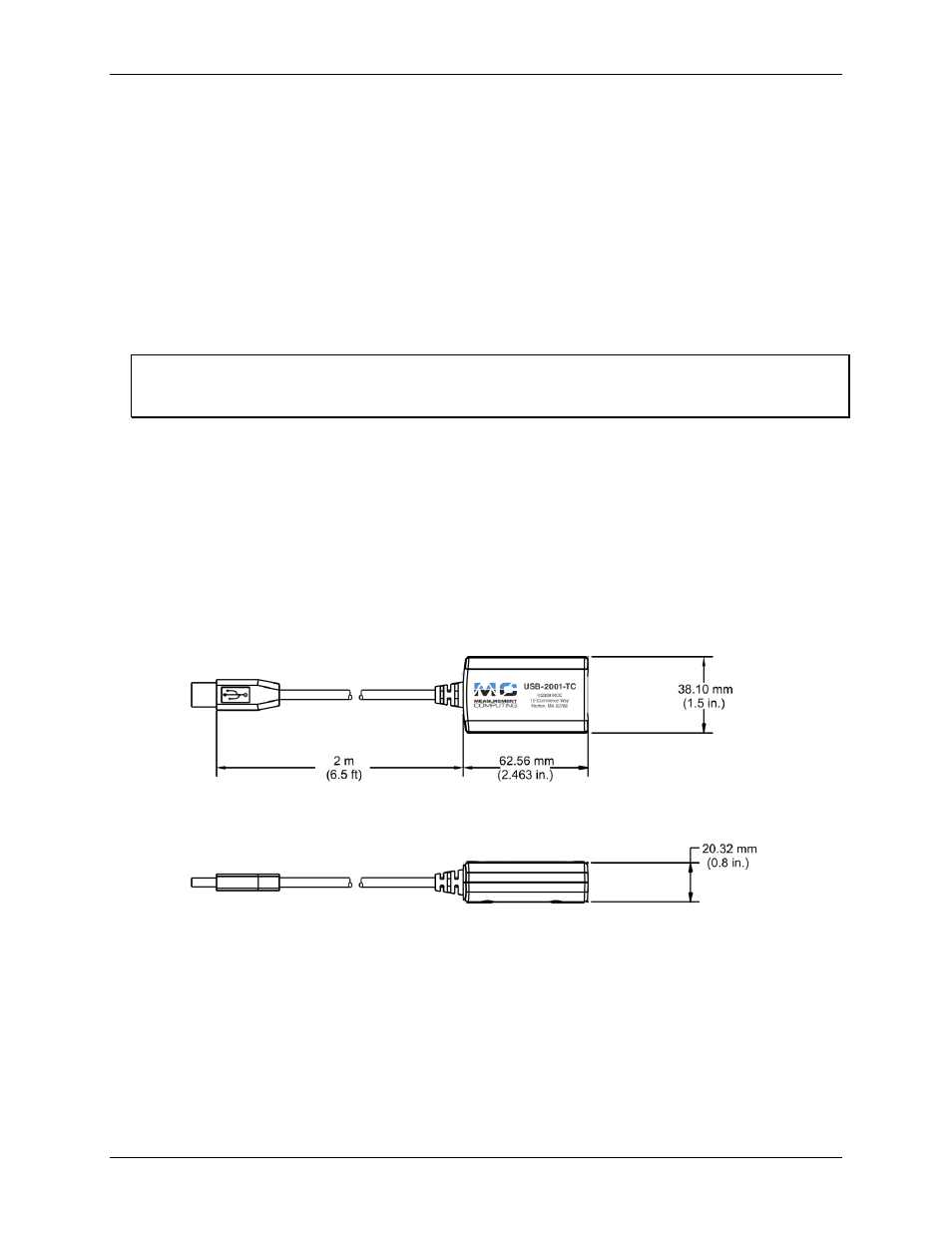
USB-2001-TC User's Guide
Functional Details
11
Thermocouple measurement accuracy
Cold-junction temperature measurement accuracy
Heat from other nearby heat sources can cause errors in thermocouple measurements by heating up the
terminals so that they are at a different temperature than the cold-junction compensation sensor used to measure
the cold junction.
Minimizing thermal gradients
Thermocouple wire can be a significant source of thermal gradients if it conducts heat or cold directly to
terminal junctions. To minimize these errors, follow these guidelines:
Use small-gauge thermocouple wire. Smaller wire transfers less heat to or from the measuring junction.
Avoid running thermocouple wires near hot or cold objects.
Increasing the thermocouple length
If you need to increase the length of your thermocouple, use wires made of the same conductive material to
minimize the error introduced by thermal EMFs.
Data linearization
To convert data acquired from the USB-2001-TC to temperature values, the following calculations need to be
performed:
A/D calibration
CJC correction
Thermocouple linearization
These calculations are performed by the DAQFlex API. Refer to the DAQFlex API source code for an example
of how to perform these calculations.
Mechanical drawings
Figure 7. USB-2001-TC dimensions