Installation rotary actuators – Greenheck El-O-Matic E and P Series User Manual
Page 5
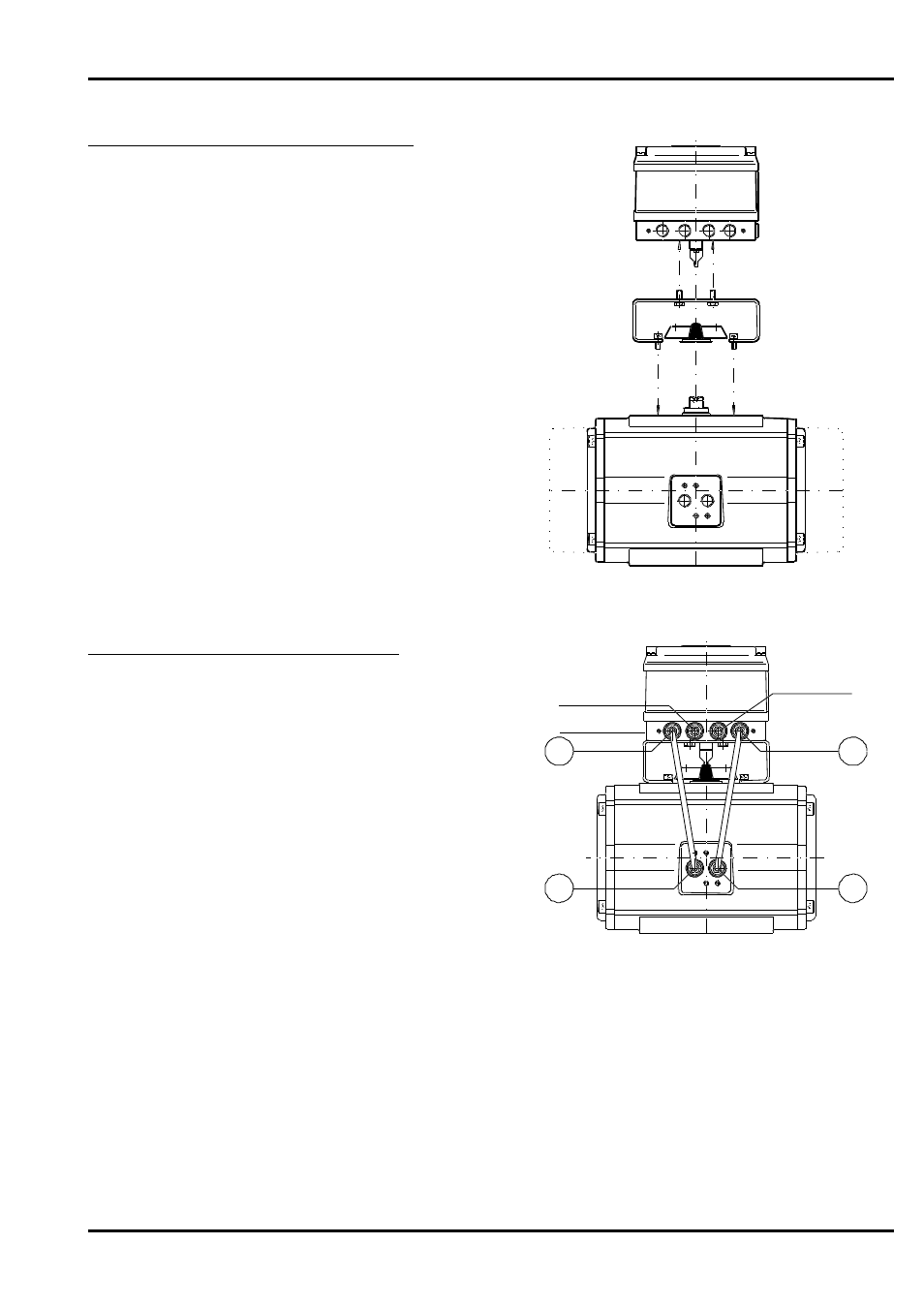
Pneumatic connections
Double acting
Mechanical Installation
3.
Installation Rotary Actuators
Mechanical installation - Rotary actuators
The positioner is mounted on to the top surface of the
pneumatic actuator using an appropriate mounting kit.
The positioner’s mounting configuration is to the VDE/
VDI 3845 standard, if the actuator is to the same
standard, a standard NAMUR mounting kit can be
used, otherwise a special mounting kit will have to be
obtained.
Assuming the installation will use the standard NAMUR
mounting kit, proceed as follows:
1. Fix the bracket to the top surface of the actuator
using the 4 screws provided.
2. Check that the spring clip is securely in place on the
bottom of the positioner shaft.
3. Locate the positioner in place on top of the bracket,
making sure that the 4 mm. tongue locates properly
into it’s slot in the actuator spindle and the centring
screw is in position.
4. Fix the positioner to the bracket using the 4 screws
provided.
Pneumatic Connections - Double acting
This assumes a standard (direct acting) installation
with an increasing signal to open the valve in a CCW
(counter clockwise) direction.
Before connecting any air supply make sure that
the air available is clean dry instrument air filtered
to at least 25 microns - see page 4.
1. Connect an appropriate piece of air tubing between
the port 1. on the positioner to the “A” port on the
actuator. (The “A” port is the one that when air is
applied to it, rotates the actuator in a counter clock-
wise direction).
2. Connect an appropriate piece of air tubing between
the port 2. on the positioner to the “B” port on the
actuator. (The “B” port is the one that when air is
applied to it, rotates the actuator in a clockwise
direction).
3. Connect an air supply to the positioner port Marked
“Supply”.
4. If the positioner is required to meet enclosure rating
IP54, be sure that the "Exhaust" port is connected
with elements which prevent the input of water and
give no pressure rising inside the housing because
of throttling of exhaust flow (no sintered filters, but a
piece of tube or a special IP65 Exhaust plug with
diaphragm
5. Connect the instrument air to the port marked
"INSTR".
Note: For a reverse acting assembly, both the air
connections and the cam plate must be
reversed - see page 7.
Supply
Exhaust
Instrument
A
1
2
B