Installation of direct gas piping, Direct gas nameplate, Supply gas line – Greenheck DGK (468695) User Manual
Page 6
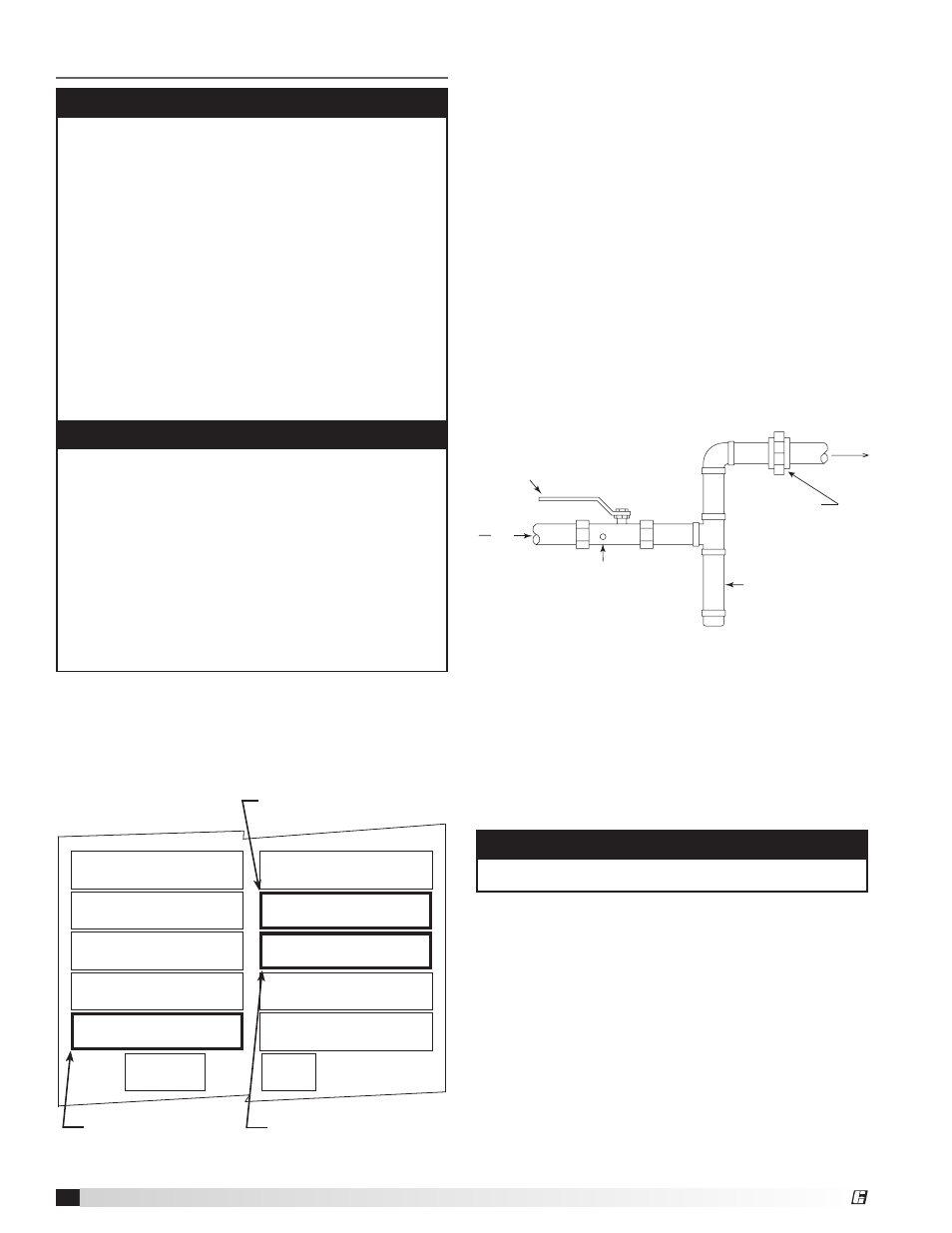
6
Installation of Direct Gas Piping
IMPORTANT
All gas piping must be installed in accordance
with the latest edition of the National Fuel Gas
Code ANSI/Z223.1 and any local codes that may
apply. In Canada, the equipment shall be installed
in accordance with the Installation Code for Gas
Burning Appliances and Equipment (CGA B149)
and Provincial Regulations for the class. Authorities
having jurisdiction should be consulted before
installations are made.
All piping should be clean and free of any foreign
matter. Foreign material entering the gas train can
damage the valves, regulators and burner.
Do NOT connect the unit to gas types other than
what is specified and do NOT connect the unit to
gas pressures that are outside of the pressure range
shown on the label.
WARNING
All components of this or any other gas fired heating
unit must be leak tested prior to placing the unit
into operation. A soap and water solution should be
used to perform this test. NEVER test for gas leaks
with an open flame.
If pressure testing in excess of 1/2 psig (3.5 kPa),
the heater and manual shutoff valve must be
disconnected from the supply gas line.
If pressure testing at or below 1/2 psig (3.5 kPa), the
heater must be isolated from the supply gas line by
closing its manual shutoff valve.
1. Determine the Supply Gas Requirements: The
unit’s direct gas nameplate states the requirements
for the gas being supplied to the unit. The direct gas
nameplate is located on the outside of the unit on
the control center side.
2. Install Additional Regulator if Required: When
the supply gas pressure exceeds the maximum gas
pressure shown on the direct gas nameplate, an
additional regulator (by others) is required to reduce
the pressure. The regulator must have a listed leak
limiting device or it must be vented to the outdoors.
NOTE: The regulator located inside the unit is used
to adjust the unit’s maximum output temperature.
3. Connect the Supply Gas Line: A manual shut off
valve (gas cock), 1/8 in. plugged test port and 6 in.
drip leg must be installed prior to the gas train. The
valve and the test port must be accessible for the
connection of a test gauge. Supply gas connections
must be made by a qualified installer and are not
furnished by manufacturer.
This assembly must be installed in the inlet of the
gas train. When installed, the manual shut off valve
(gas cock) will be outside of the unit and will shutoff
all gas to the unit.
4. Test the System for Leaks: Check both the supply
lines and the factory piping for leaks. Apply a soap
and water solution to all piping and watch for
bubbling which indicates a leak.
The factory piping has been checked for leaks
but should be rechecked due to shipping and
installation.
WARNING
Never test for a gas leak with an open flame.
Type of gas
“ W.C.
“ W.C.
“ W.C.
F
PSI
“ W.C.
“ W.C.
MAX BTU/HR
BTU/H MAX
NORMAL MANIFOLD
PRESSURE
PRESSION D’ADMISSION
NORMALE
MIN GAS
PRESSURE
PRESSION DE GAZ
MIN BURNER
PRESSURE DROP
PERTE MIN DE PRESSION
DANS LE BRULEUR
TYPE OF GAS
NATURE DU GAZ
MIN BTU/HR
BTU/H MIN
MIN GAS PRESSURE
FOR MAX OUTPUT
PRESSION DE GAZ MIN
POUR PUISSANCE MAX
MAX BURNER
PRESSURE DROP
PERTE MAX DE PRESSION
DANS LE BRULEUR
MAX GAS
PRESSURE
PRESSION DE GAZ
MAX
DESIGN ∆T
∆T NORMALE
EQUIPPED FOR
CONCU POUR
SCFM
“ W.C.
EXTERNAL STATIC PRESSURE
PRESSION STATIQUE EXTERIEURE
AGAINST
CONTE
Maximum gas pressure
Minimum gas pressure for
maximum output
Direct Gas Nameplate
To
Controls
Gas Cock
From
Gas
Supply
6 in. Trap
1/8 in. Plugged Tap
Ground Joint Union
Supply Gas Line
Model DGK Make-Up Air
®