Worcester actuation systems – Flowserve DFC17 User Manual
Page 8
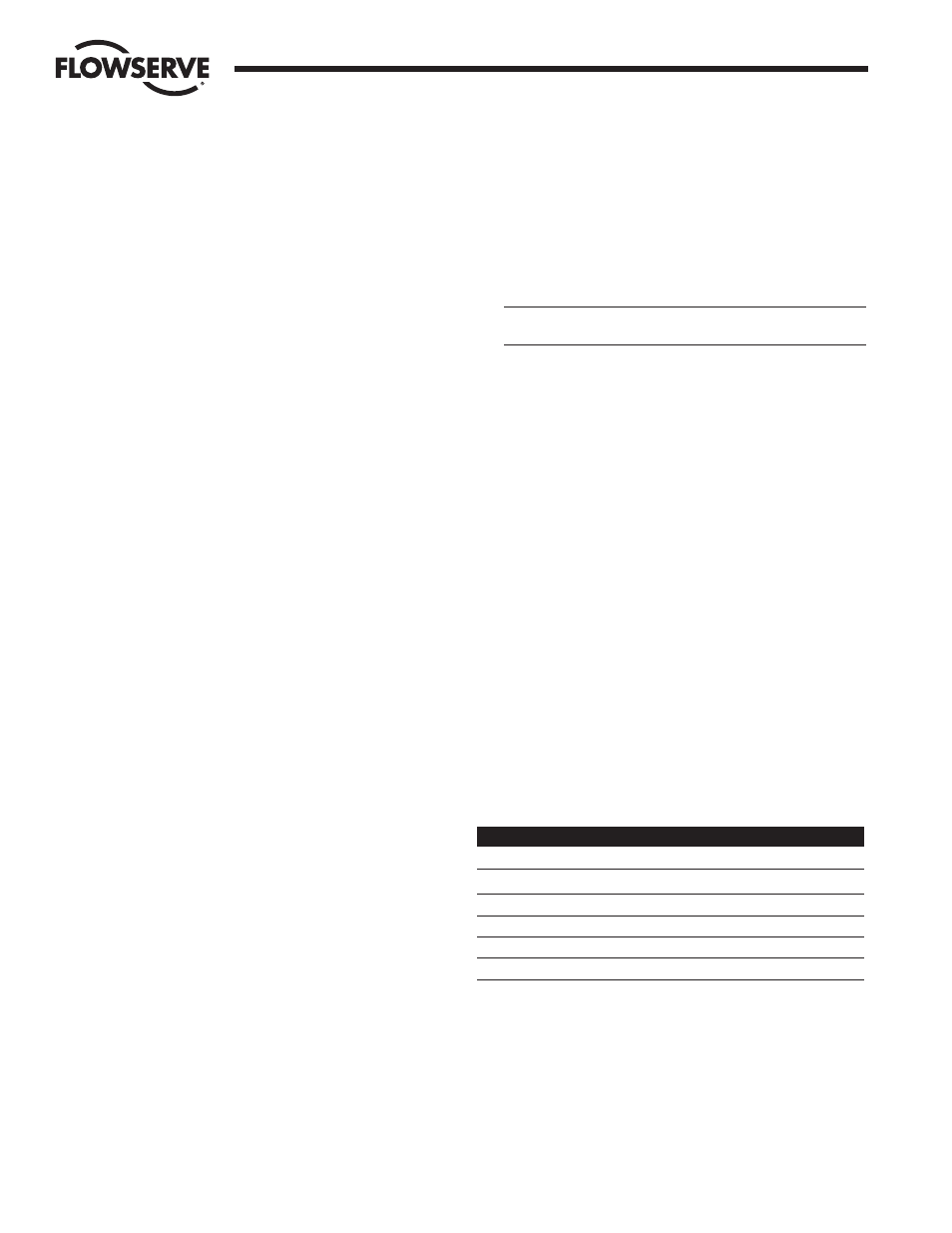
8
DataFlo Digital Electronic Controller DFC17 Installation, Operation and Maintenance Instructions
WCAIM2026
B.
The Controller circuit board will accept one of the
following process signal inputs, depending on the circuit
board ordered:
One of the following analog inputs:
4–20 mA
1–5 mA
10–50 mA
0–5 VDC
0–10 VDC
135 ohm pot
1000 ohm pot
One 100 ohm Platinum RTDs – NOTE: A single channel is
standard. A two channel is available as a custom product
and must be hard wired to the red and two black leads
from circuit board identified as signal 2.
A single J, K, T, or E type Thermocouple
NOTE: Field changes to the Controller board are not
advised. Consult Flowserve before attempting any
modification.
2.3 LED Indicators
Light emitting diodes (LED) marked LD1 (CW) and LD2 (CCW)
are in the output circuits and when lit indicate which direction
the actuator is trying to drive. A third LED, LD3, is used to
indicate when an alarm condition exists. If LD3 is lit, the alarm
that caused it to light must be determined by looking at the
liquid crystal display (LCD) and finding the alarm parameter with
the UP or DN switch.
2.4 Controls (Override)
There are no adjustable controls provided on the circuit board
because none are necessary. All parameters are set through the
programming switches (keys) or the RS485 interface. Local
pushbutton control is provided at the actuator by simultaneously
pressing the SEL and UP switches (keys) for three seconds. At
this point the UP and the DN switches (keys) can be used to
manually position the actuator shaft. Pressing the SEL switch for
three seconds will return the Controller to the run mode.
2.5 AC Power Control
The AC output circuits are controlled by solid state switches
(triacs Q3, Q4), which will provide trouble-free operation for the
life of the equipment they are used with,
AS LONG AS THEY ARE
OPERATED WITHIN THEIR RATINGS.
The ratings for the solid state switches used in the Worcester
DataFlo Digital Electronic Controller are listed in part 5.3.
3.0 WIRING OF DIGITAL CONTROLLER
AND SERIES 75 ELECTRIC
ACTUATOR
See wiring diagrams located under actuator cover and/or Figures 2
through 4 for customer connections.
3.1 Actuator Power
CAUTION: Wiring should be inserted only to mid-point of
terminal strip.
3.1.1 Wire
Size
Power to the Controller and from the Controller to the
actuator should be with wire no smaller than #18 gauge
and with insulation rated for the particular application.
The #18 gauge wire size is sufficient for all Worcester
Series 75 actuators. When using the Controller with other
makes of actuators, check the manufacturer’s current
rating to determine the correct wire size.
3.1.2 Termination and Voltage
Power connections are made to terminals 1 and 2 of the
terminal strip. The AC neutral or common, or DC
negative wire should be connected to terminal #1 and
the AC “Hot” or DC positive wire to terminal #2. Note
that the AC Controller requires a minimum of 110 VAC,
and a maximum of 130 VAC for the 120 VAC version and
a 220 VAC minimum, 250 VAC maximum for the
240 VAC version.
Grounding wires should be connected to green colored
grounding screw (if present) on actuator base or to any
base plate mounting screw in the actuator.
3.1.3 Minimum Fuse Ratings
See Minimum Fuse Rating table when overcurrent
protection is used in motor power circuit.
Minimum Fuse Rating for Overcurrent Protection
Actuator Size
Voltage
Fuse Rating
10-23
120 VAC
5 A
25/30
120 VAC
10 A
10-23
240 VAC
3 A
25/30
240 VAC
5 A
10-23
24 VDC
5 A
NOTE: This table shows the minimum rating to prevent inrush current
from blowing the fuse.
Flow Control Division
Worcester Actuation Systems