0 operation of the digital controller, Worcester actuation systems – Flowserve DFC17 User Manual
Page 12
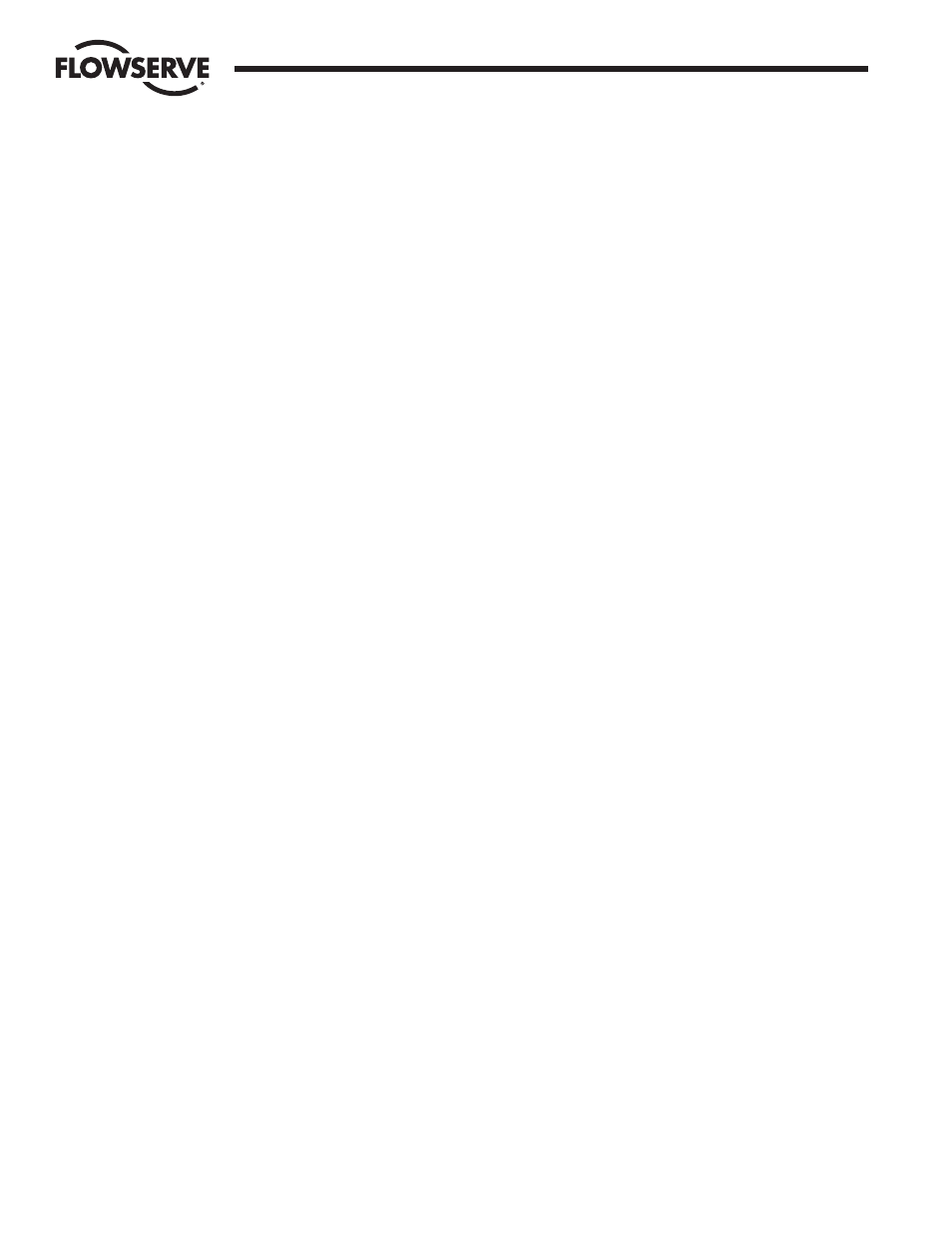
12
DataFlo Digital Electronic Controller DFC17 Installation, Operation and Maintenance Instructions
WCAIM2026
4.0 OPERATION OF THE DIGITAL
CONTROLLER
Refer to RS485 Communications software diskette included with
controller for more information.
The DFC17 Controller is capable of being operated in several modes.
The normal mode of operation is the RUN mode. Following is a list of
the various modes and the key sequences necessary to enter each of
them and the function of each of the parameters within that mode:
4.1 Run Mode “run”
This is the normal operating mode.
While in the Run Mode momentarily pressing:
SEL Toggles between alternating name/value and continuous
value display.
UP Shows the next parameter.
DN Shows the previous parameter.
4.1.1 Run Mode Menu
Pressing SEL while the alarm condition is alternating on
the display will freeze the display with the highest priority
alarm showing. At that point, pressing SEL again will
attempt to reset the alarm display. If the alarm
condition(s) still exist after pressing SEL, the display will
continue to show the alarm(s).
See table on page 13.
4.1.2 Mode Change Key Sequence
See table on page 13.
4.1.3 Alarm Displays
See table on page 13.
4.2 Calibration
Mode
Press SEL + DN keys for three seconds to enter Calibration Mode
CAL from Run Mode. A security code may be required for entry
to the Calibration Mode. If one is required, it is checked and
entered using the instructions below and for editing a numeric
value as described in paragraph 4.3.2.
Simultaneously press and hold the SEL and DN keys for three
seconds. CAL will be displayed for two seconds and the security
code will be checked. If the required security code is not zero
(“0000”), the display will begin alternating between “CodE” and
“0000”. If the required security code is zero, it will not need to be
entered, i.e., it will be bypassed and display will automatically
flash “SEtL”. Skip to paragraph 4.2.2.
Enter the security code, if necessary, as follows. (If the code is
forgotten, the special number 4800 can be used to gain entry).
Quick tap SEL key once. First 0 will flash. Quick tap UP key until
you reach code number. Quick tap the DN key once. The second
0 will flash Quick tap the UP key until the next code number is
reached. Continue this procedure as needed for the remaining
code numbers. Quick tap SEL to accept code.
Display now flashes between “SEtL” and a value.
Press SEL key for two seconds to return to the Run Mode.
For the Calibration Mode Menu table, press:
SEL
To sequence through the calibration parameters.
SEL + UP To enable/start calibration of the selected parameter.
4.2.1 Calibration Mode Menu
See table on Page 14.
4.2.2 Key Sequences for Calibrating Setpoint Lower Limit
The lower setpoint parameter SEtL should be displayed.
Press SEL + UP to begin calibrating the parameter.
Attach an accurate current source to the setpoint signal
input and adjust the source to produce a 4 mA signal. The
voltage reading on the display should be less than 1 volt.
Press SEL to accept the value shown and return to the
calibration menu.
4.2.3 Key Sequences for Calibrating Setpoint Upper Limit
Press DN to select the upper setpoint parameter SEtU
Press SEL + UP to begin calibrating the parameter.
Attach an accurate current source to the setpoint signal
input and adjust the source to produce a 20 mA signal.
The voltage reading on the display should be between
3.800 and 5.000 volts.
Press SEL to accept the value shown and return to the
calibration menu.
4.2.4 Key Sequences for Calibrating Clockwise Position
Press DN to select the clockwise setpoint parameter PoC
Press SEL + UP to begin calibrating the parameter.
1) Use either the UP or DN switches to manually rotate
the actuator to its full clockwise (CW) position.
2) With the actuator in the full CW position, adjust the
feedback potentiometer by rotating the face gear
located on the actuator shaft with your fingers, for a
reading between .200 and .400 volts.
NOTE: It is not necessary to loosen or remove face gear
snap ring(s) (if present) to rotate gear, it is a friction fit.
For gears that do have snap rings, and if for any reason
the snap ring(s) must be removed, do not overstretch
them. Use the minimum opening to allow the rings to slip
over the gear.
Press SEL to accept the value shown and return to the
calibration menu.
Flow Control Division
Worcester Actuation Systems