Worcester actuation systems – Flowserve DFC17 User Manual
Page 19
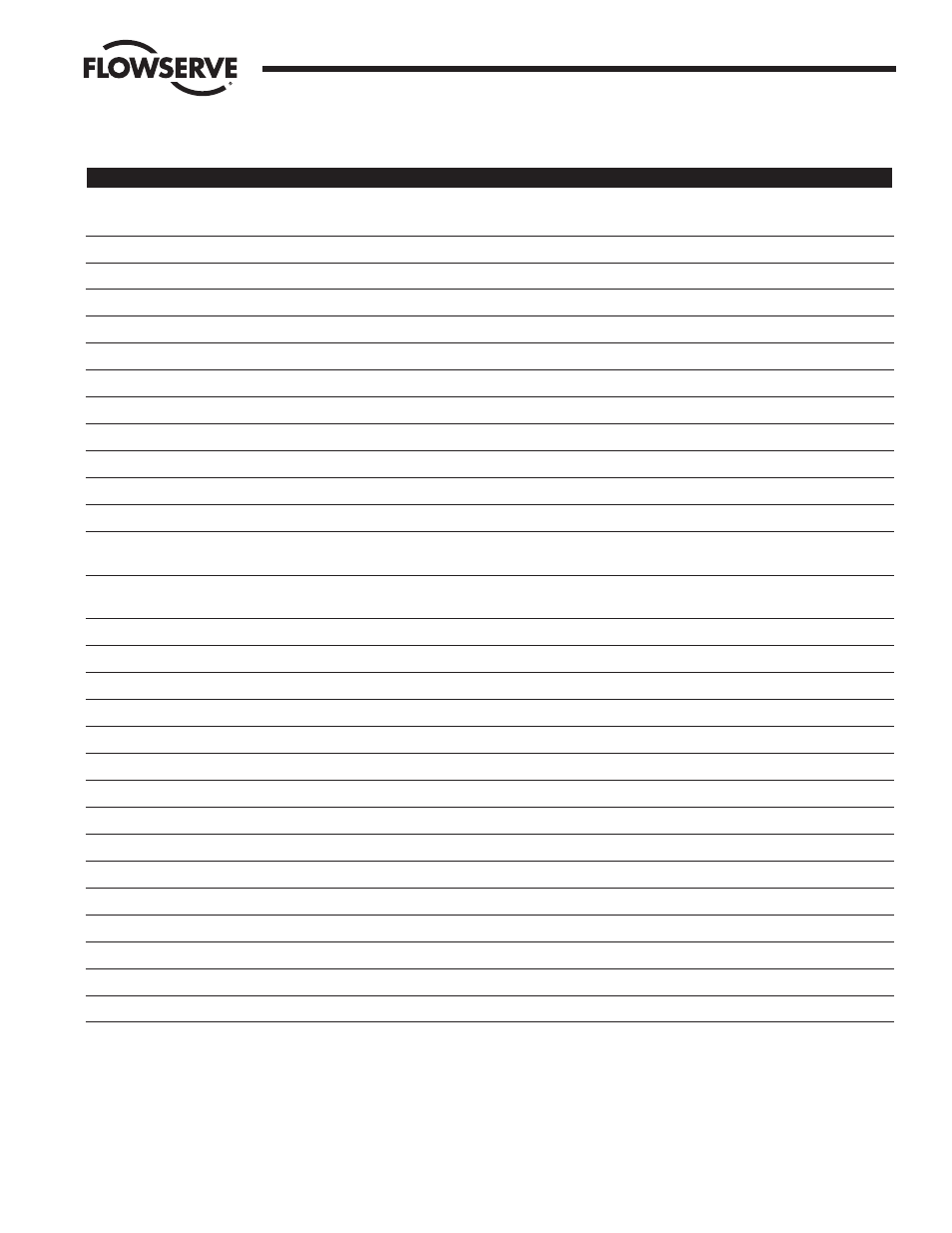
WCAIM2026
DataFlo Digital Electronic Controller DFC17 Installation, Operation and Maintenance Instructions
19
Program Mode Menu
Display
Description
Mininum Value
Maximum Value
CodE
Security code for access to Program, Calibration
0000
9999
and Manual Setpoint modes.
Addr
Communications unit address
1
255
PtEr
Proportional Control Term
0000
9999
itEr
Integral Control Term
000
999
dtEr
Derivative Control Term
0000
8000
onH
Motor Cycle Interval
1.0 sec
999.9 sec
FiLT
Process Signal Filter Time
0.8 sec
60.0 sec
bLt
Gearbox Backlash Time
0 ms
9999 ms
tort
Gear Torque Time
0 ms
9999 ms
dEbA
Controller Dead Band
0.1
20.0
ACt
Controller Action – RISE or FALL
CyCr
Cycle Interval Reset – ON or OFF
FPOS
Process or Setpoint invalid reading action –
0.0%
100.0%
HOLD, NONE, or a position value.
SAct
Invalid feedback pot reading action – GOC (go clockwise),
GOCC (go counter-clockwise), HOLD, or NONE.
yA
Lower shaft position limit
0.0%
100.0%
yE
Upper shaft position limit
0.0%
100.0%
br
Brake ON time.
0.10 sec
0.99 sec
CyCn
Run Time Cycle Count (reading represents thousands of cycles).
AHi
Over-travel Alarm
0.0%
100.0%
ALo
Under-travel Alarm
0.0%
100.0%
PrLo
Process Low Alarm Value
PENL
PENU
PrHi
Process High Alarm Value
PENL
PENU
bAUD
Communications Baud Rate
1200 bps
38.4 Kbps
PrS9
Process Signal Selection – PR1, PR2, or BOTH
PEnL
Process Engineering Units Range (Lower)
-999
999
PEnU
Process Engineering Units Range (Upper)
-999
999
SEnL
Setpoint Engineering Units Range (Lower)
-999
999
SEnU
Setpoint Engineering Units Range (Upper)
-999
999
PrSt
Restore Default Parameters (YES or NO)
Note: A decimal point may be entered when entering PEnL and PEnU values, if the controlled range falls between -99.9 and 99.9. This has the
effect of improving resolution for small process ranges (i.e., 0.0 to 10.0 GPM). See Controller Specification on floppy disk for more detail.
Flow Control Division
Worcester Actuation Systems