Operation / mode 90 – Flowserve APEX A9000 Accord User Manual
Page 16
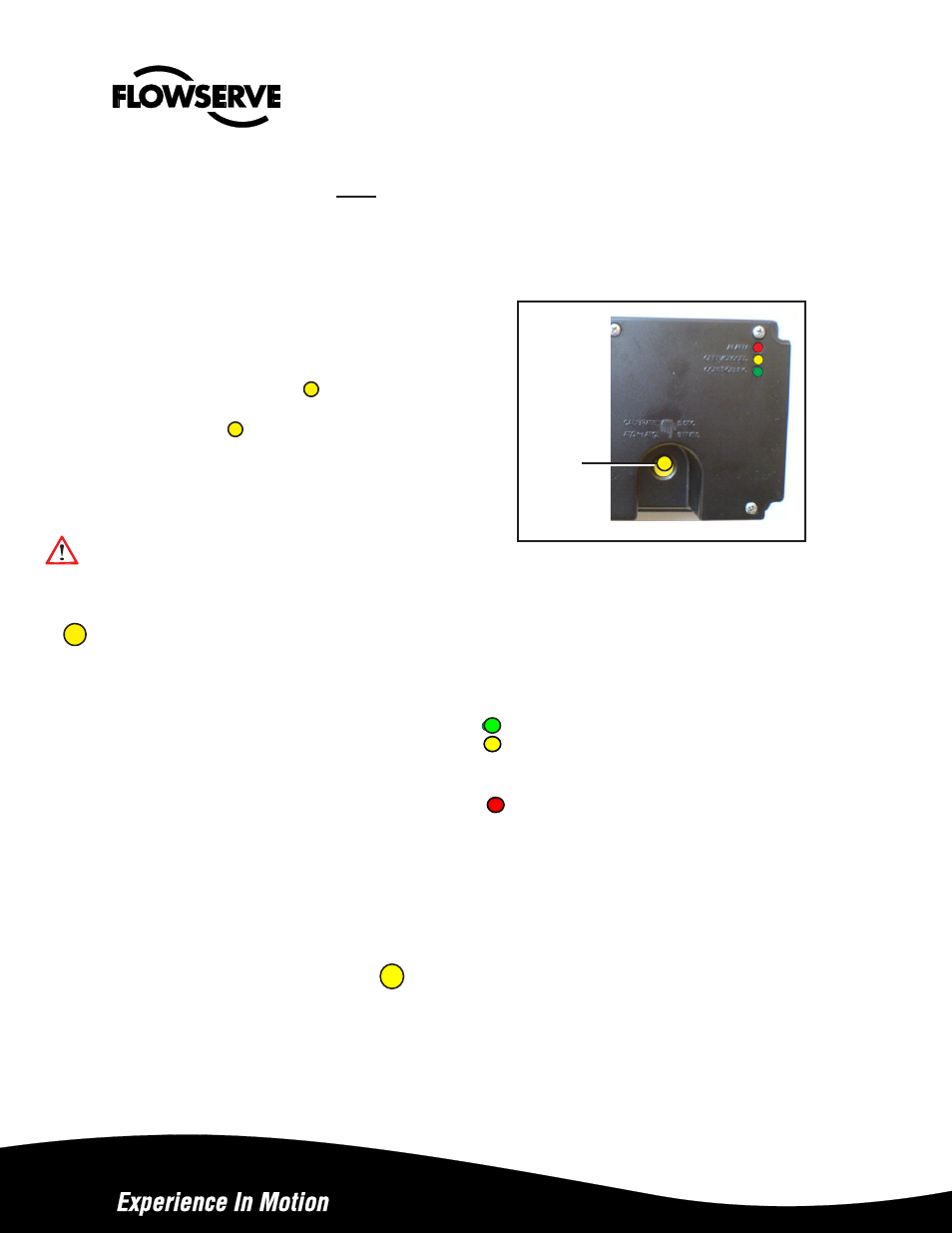
16
Example: DCS Compliance Voltage = 19 V, R
barrier
= 300Ω, R
wire
= 25Ω and Current
max
= 20mA
Voltage = 19V -
0.020A(300Ω + 25Ω) = 12.5V
This system will support the Apex A9000 , as the voltage 12.5 V is greater than the required 8 VDC for non-HART and 9.4 VDC for
HART.
10. Operation / Mode 90
10.1 General
The Apex A9000 is operated by the yellow button.
Alarm
Depending on desired action, press the button:
Open/Close
Controlling
- during a number of seconds (Ex 5 sec):
Or
- a number of times. (Ex
x3)
Calibration
10.2 Startup
button
Connect Air supply and a mA-simulator to the positioner.
Warning: During calibration, the actuator may stroke
unexpectedly.
5 sec.
Press the button for 5 sec. (Re- lease the button when the three LED:s start to flash alternately).
The calibration starts, the actuator goes go to max. and min. position and calculates the control parameters.
The Calibration procedure will take between 30 seconds and some minutes depending on actuator size.
The three LED
’s will flash alternately during calibration.
Afte
r calibration all the three LED’s are lit for a moment.
A successful calibration is indicated by yellow or green LED:
Green LED flashes = In service
Yellow LED flashes = In service.
The unit vents in max or min position.
An unsuccessful calibration by error codes:
Apex A9000 does not reach setpoint
For other indications, see error codes on page 30.
10.4 Set Direct or Reverse action
Note! For safety reason, this operation has to be done max 5 minutes after calibration. If time has run out, or if
power is disconnected during the five minutes, perform a new calibration, before changing the direction.
Apply 4 mA. If valve is in right position, then check the position over the whole range (8, 12, 16 and 20 mA)
If the direction needs to be changed, press the calibration button 3 times, and the direction will change.
X3
Check operation at 4
– 8 – 12 – 16 and 20 mA.