15 inner loop status, 16 main board status, 17 electronic board status – Flowserve Logix 520MD+ DD User Manual
Page 11: 18 stroke/friction status, 19 main board status, 20 electrical components status, 21 software status, 22 pressure calibration status, 5 stroke tests, 1 partial stroke test
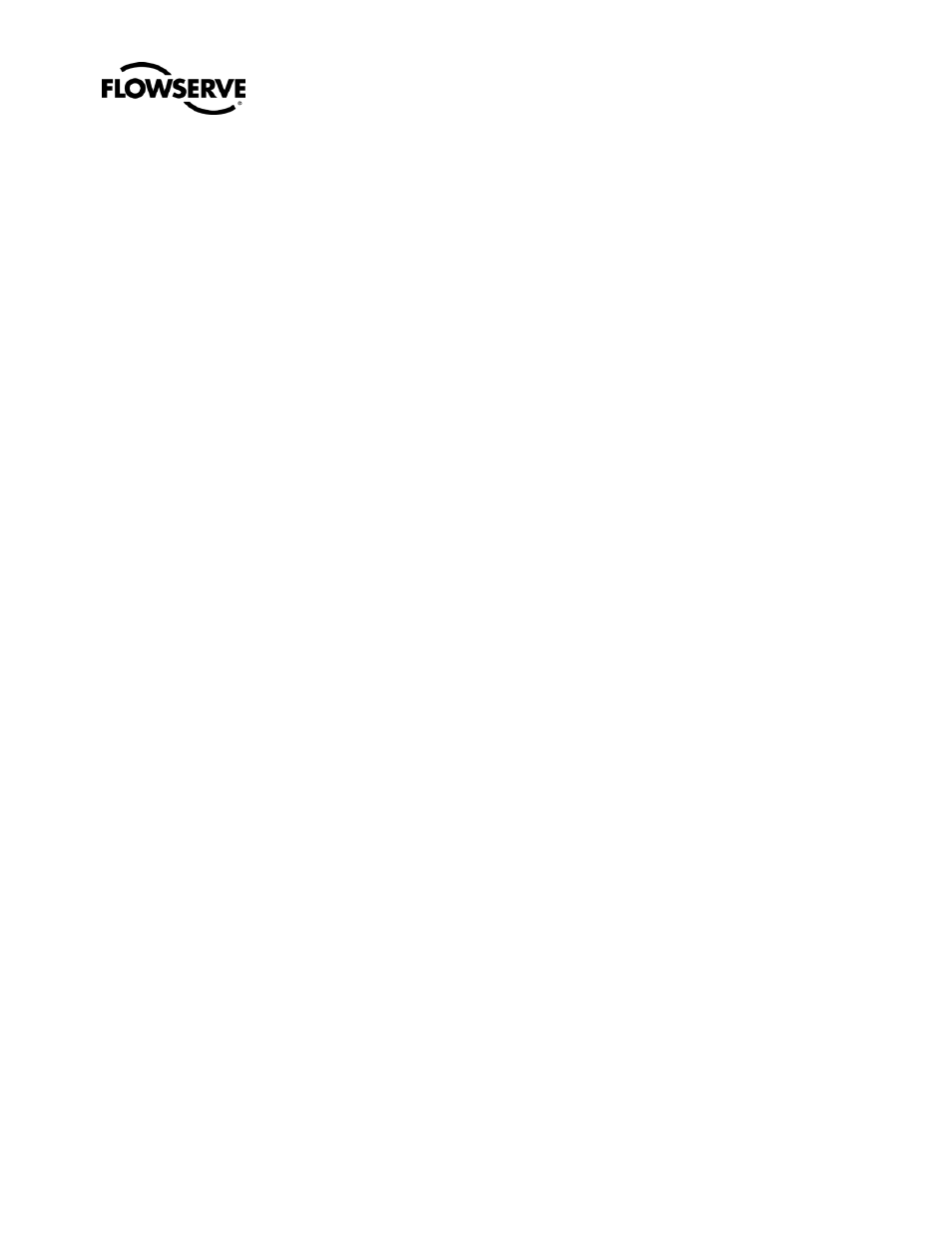
DD User Manual - Logix® 520MD+ Series Digital Positioner FCD-LGENSF0013-01
© Flowserve Corporation
11
Mask Command Frequency Warning, Command Frequency
Alarm, Command Amplitude Warning, Command Amplitude
Alarm, Position Frequency Warning, Position Frequency
Alarm, Position Amplitude Warning, and Position Amplitude
Alarm.
4.3.2.15
Inner Loop Status
Mask Pilot Relay Response Warning, Pilot Relay Response
Alarm, Piezo Voltage High Warning, Piezo Voltage High
Alarm, Piezo Voltage Low Warning, Piezo Voltage Low
Alarm, and Driver Module Alarm.
4.3.2.16
Main Board Status
Mask Main Board Electronic Failure Warning, Software Error
Warning, Memory Error Warning, Temperature High
Warning, and Temperature Low Warning.
4.3.2.17
Electronic Board Status
Mask Aux Card 1 Failure Warning, Aux Card 2 Failure
Warning, Aux Card 1 No Loop Power, Aux Card 2 No Loop
Power, Aux Card 1 Error, Aux Card 2 Error, Pressure Sensor
Board Failure Warning, and Low Battery Warning.
4.3.2.18
Stroke/Friction status
Mask Reversed Spring, Insufficient Spring, and No Spring.
4.3.2.19
Main Board Status
Mask Humidity Sensor Failure, Oscillator Fault, Position
Sensor ADC Failure, Supply Voltage Error, Reference
Voltage Error, Shunt Voltage Error, and Piezo Voltage Error.
4.3.2.20
Electrical Components Status
Mask Pilot Can't Open, Pilot Can't Shut, Hall Sensor Failure,
and ILO Out Of Range.
4.3.2.21
Software Status
Mask NVMEM CRC Error, RAM Error, RAM CRC Error,
FLASH CRC Error, Watch Dog Time Out, Stack Overflow
Warning, CPU Usage Warning, and Firmware Update
Applied.
4.3.2.22
Pressure Calibration Status
Mask Port S Out Of Range, Port A Out Of Range, Port B Out
Of Range, Port S Range too Small, Port A Range too Small,
Port B Range too Small, and Pressure Sensor Failure.
5 STROKE TESTS
Run a partial stroke tests and view results. Configure the
continuous stroke test.
DANGER: Using this feature will result in valve movement
and the inability to operate the valve until the operation is
complete. Notify proper personnel that the valve may
stroke, and make sure the valve is properly isolated before
proceeding.
5.1
Partial Stroke Test
Run a partial stroke tests and view results.
5.1.1
Run Partial Stroke Test
Start a partial stroke test. Warning: The PST will cause valve
movement.
5.1.2
PST Time To Breakaway
View the time required for the valve to begin movement.
5.1.3
PST Force at Breakaway
View the force recorded when the valve began to move. This
force is valid for slow ramps only.
5.1.4
PST Time to Target
View the time taken for the position to come within 2% of the
final command after the initial change in command.
5.1.5
PST Result
View the pass/fail result of the last partial stroke test.
5.2
Continuous Stroke Test
Configure the continuous stroke test (CST). This feature is
NOT recommended for processes requiring highly accurate
positioning, or for valves that are frequently adjusting
position. The CST function superimposes a small,
continuous bi-directional ramp over the input command. By
constantly moving the valve, additional diagnostic data can
be gathered that would otherwise be unavailable with a
constant input command. The superimposed ramp reverses
when the valve moves.
5.2.1
CST Ramp Rate
Set the rate of the superimposed ramp in percent/second.
5.2.2
CST Max Amplitude
Set the maximum ramp amplitude. The valve position will not
always follow the full ramp amplitude. If the valve moves
before the full ramp amplitude is reached, the superimposed
ramp command will be reversed, edging the valve the other
way. This way the actual movement of the valve is
minimized.
5.2.3
CST Interval
Set the amount of time (in seconds) the positioner should
wait between ramping attempts.
5.2.4
CST Failure Count