Flowserve MF User Manual
Page 38
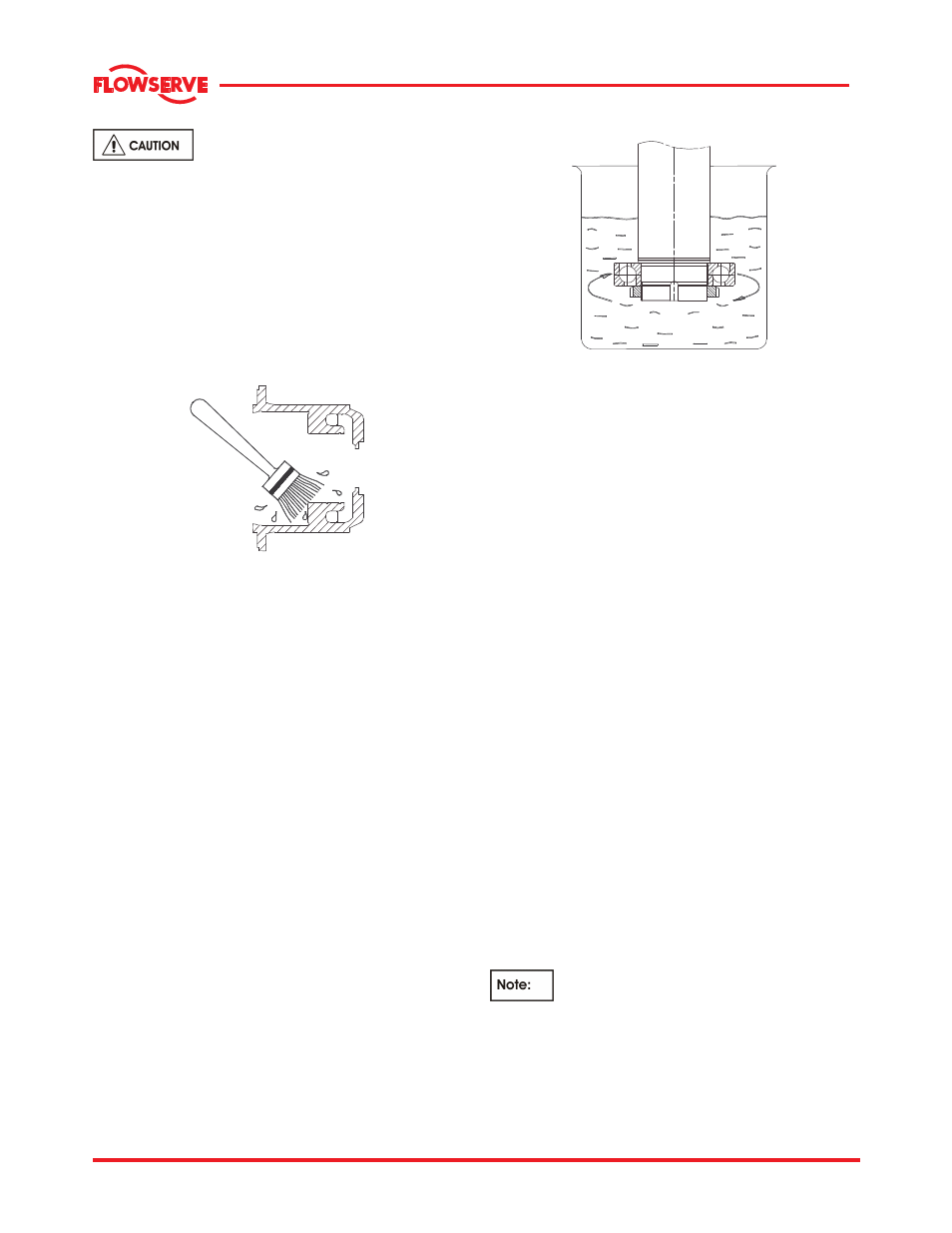
MF USER INSTRUCTIONS ENGLISH 71569191 12/04
Page 38 of 50
®
6.1.10.3 Grease change
if Kerosene is used to clean the
bearings make sure that the required safety
measures are to be in place while handling this liquid
fuel for cleaning (See Fuel supplier/ manufacturer’s
Material Safety Data Sheets for provided flash and
flame temperatures).
a) Remove the bearing housing from the rotor
assembly.
b) Brush the bearing housing with hot oil 94 to 115
o
C (200
o
to 240
o
F) or other non-toxic solvent.
c) Clean and flush out the housing with a light
mineral oil.
d) Do not use waste oil to clean the housing.
6.1.10.4 To clean the bearings
a) Wipe off as much grease as possible with a clean
lint-free cloth.
b) Brush bearings with hot oil or non-toxic solvent
80 to 95
o
C (180 to 200
o
F ) while gently spinning
the outer bearing ring.
c) Spin each roller to ensure that it is clean.
6.1.10.5 To remove badly oxidized grease
a) Support the rotor in a vertical position and
immerse the bearing in hot oil 80 to 90 °C (175 to
195 °F) or a mixture of alcohol and light mineral
solvent.
b) Dry and re-flush the bearing with clean light oil.
c) It is important not to under or over grease the
bearings as this will lead to over heating and
premature failure. It is recommended that the
bearings be filled with grease using a suitable
spatula. In addition the housings should be no
more than half filled.
6.1.11 Mechanical seals
No adjustment is possible. When leakage reaches
an unacceptable level the seal will need replacement.
6.1.12 Gland packing
The stuffing box split gland can be completely
removed for re-packing or to enable the addition of
extra rings of packing.
The stuffing box is normally supplied with a lantern
ring to enable a clean or pressurized flush to the
center of the packing. If not required, this can be
replaced by an extra 2 rings of packing.
There must always be a small leakage, normally a
minimum of 30~60 drops per minute is required
depending upon the sleeve diameter.
6.2 Spare parts
6.2.1 Ordering of spares
Flowserve keep records of all pumps that have been
supplied. When ordering spares the following
information should be quoted:
a) Pump serial number.
b) Pump size.
c) Part name –
Refer to section 8.
d) Part number –
Refer to Section 8.
e) Number of parts required-Quantity.
The pump size and serial number are shown on the
pump nameplate.
To ensure continued satisfactory operation,
replacement parts to the original design specification
should be obtained from Flowserve. Any change to
the original design specification (modification or use
of a non-standard part) will invalidate the pump’s
safety certification.