Flowserve CPXM User Manual
Page 21
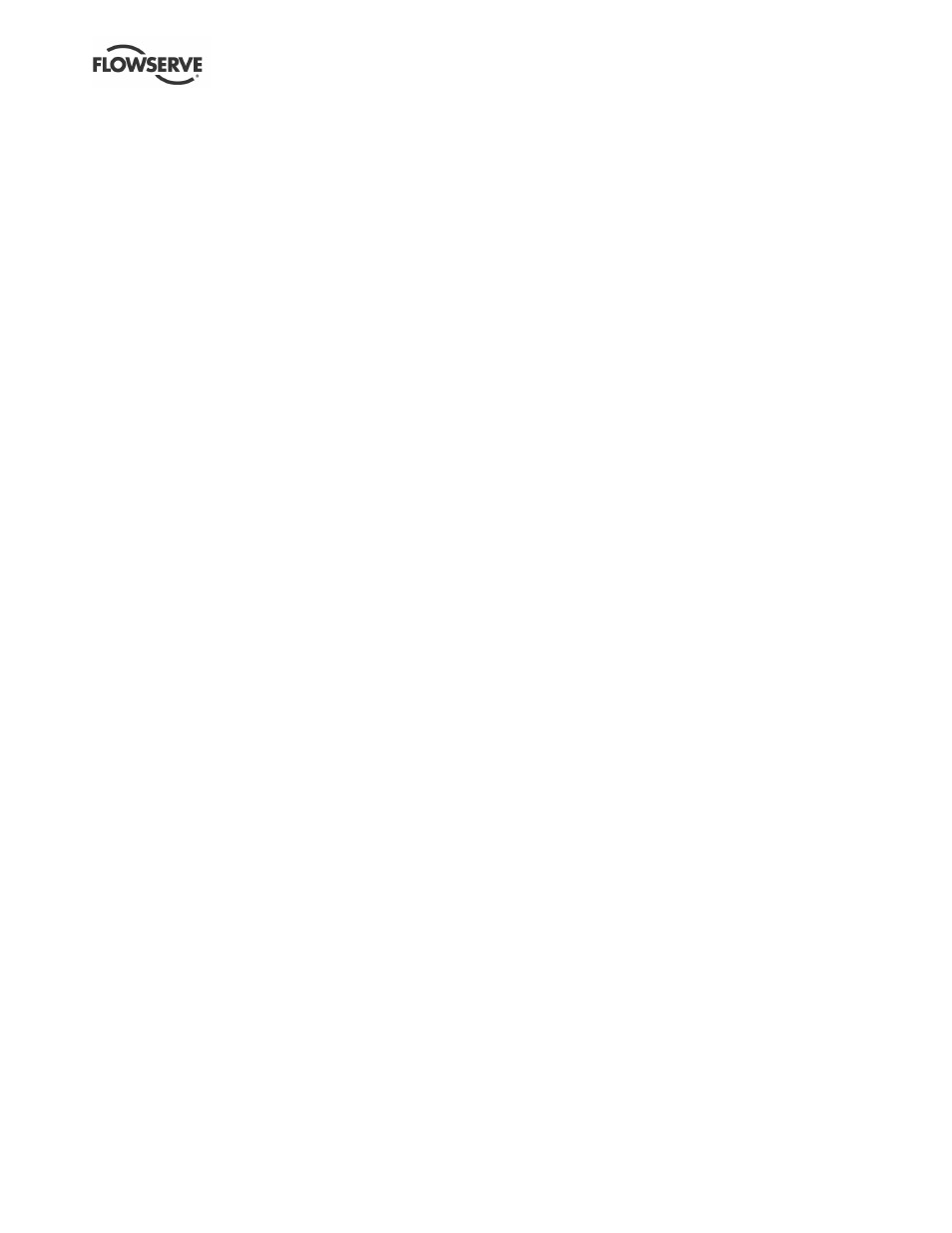
CPXM and CPXRM USER INSTRUCTIONS ENGLISH 71569101 10-08
Page 21 of 32
flowserve.com
6.10 Assembly
To assemble the pump consult the sectional
drawings. See section 8, Parts lists and drawings.
Ensure threads, gasket and O-ring mating faces are
clean. Apply thread sealant to non-face sealing pipe
thread fittings.
6.10.1 General
a) The motor shaft keyway is not used but remove
any burrs from the edge of the keyway, the motor
and pump shafts and the coupling.
b) Screw the adjustment stud into the motor shaft
and tighten with the two M 8 nuts or a stud box.
c) Locate the bracket on the motor spigot and
tighten the screws (or studs and nuts).
d) Whilst re-assembling, use new joints/gaskets and
ensure they are in their correct positions.
e) Small amounts of grease may be used to hold
the joints in position during assembly.
6.10.2 Seal housing and seal assembly
a) Extreme cleanliness is required.
b) The sealing faces and shaft surface must be free
from scratches or other damage.
c) Refer to Seal arrangement sections for seal
diagrams.
6.10.3 Impeller assembly and setting - single seal
a) Carefully press the stationary seat into the
mechanical seal housing cover, ensuring the
seating ring is not deformed.
b) Where an anti-rotation pin is fitted, ensure that
correct engagement with the slot is achieved.
c) Refer to seal manufacturer's instructions to
position the mechanical seal rotating elements.
Tighten any drive screws in the seal drive collar.
d) Fit the seal housing into the bracket and tighten
all fasteners.
e) Apply anti-seizing compound to the adjustment
stud. Carefully, fit the stubshaft (with seal in
position) through the centre of the seal housing
and locate on the adjustment stud.
f) Rotate the impeller until the back clearance is
approximately 1 mm (0.04 in.).
g) Fit the casing gasket and pump casing and
tighten all casing fasteners.
h) Refer to section 6.7, Setting impeller clearance
for setting dimensions and coupling fitting
instructions.
i)
Check that the shaft can turn freely without binding.
6.10.4 Impeller assembly and setting - double seal
For double seal arrangements, a sub assembly of the
integral impeller/stubshaft, seal housing, seal cover
and seals is required.
a) Fit the impeller shaft through the seal housing.
b) Refer to seal manufacturer's instructions to position
the mechanical seal rotating elements. The short
outboard seal is easier to assemble with a special
tapered tool fitted to the end of the shaft.
c) When the seals are in position, fit the seal cover
and tighten all fasteners.
d) Whilst supporting the seal housing, locate the
stubshaft on the adjustment stud to ensure
engagement. (Large pump sizes have a tapped
hole for fitting a lifting eye to assist with this
procedure.)
e) Rotate the impeller until the back clearance is
approximately 1 mm (0.04 in.).
f) Long studs may be used initially to locate the
seal housing and support the weight whilst the
impeller is rotated.
g) Ensure all flush connections are reconnected.
h) Refer to section 6.7, Setting impeller clearance
for setting dimensions and coupling fitting
instructions.
i)
Fit the casing gasket and pump casing and
tighten all casing fasteners.
j)
Check that the shaft can turn freely without binding.
6.10.5 Impeller assembly and setting - cartridge
seal
a) Loosely fit the cartridge seal to the seal housing,
then fit and tighten onto the bracket.
b) Apply anti-seizing compound to the adjustment
stud.
c) Insert the impeller shaft and screw on until the
gap between the impeller and seal housing is
approximately 1 mm (0.04 in.).
d) Fit the casing gasket and pump casing and
tighten all casing fasteners.
e) Refer to section 6.7, Setting impeller clearance for
setting dimensions and coupling fitting instructions.
f) To set, or reset, a cartridge seal having a PTFE
setting ring-throttle and no separate setting clips,
finger tighten the seal cover studs nuts, then fully
torque up the sleeve screws.
g) Torque up the seal cover studs nuts.