Flowserve WR User Manual
Page 18
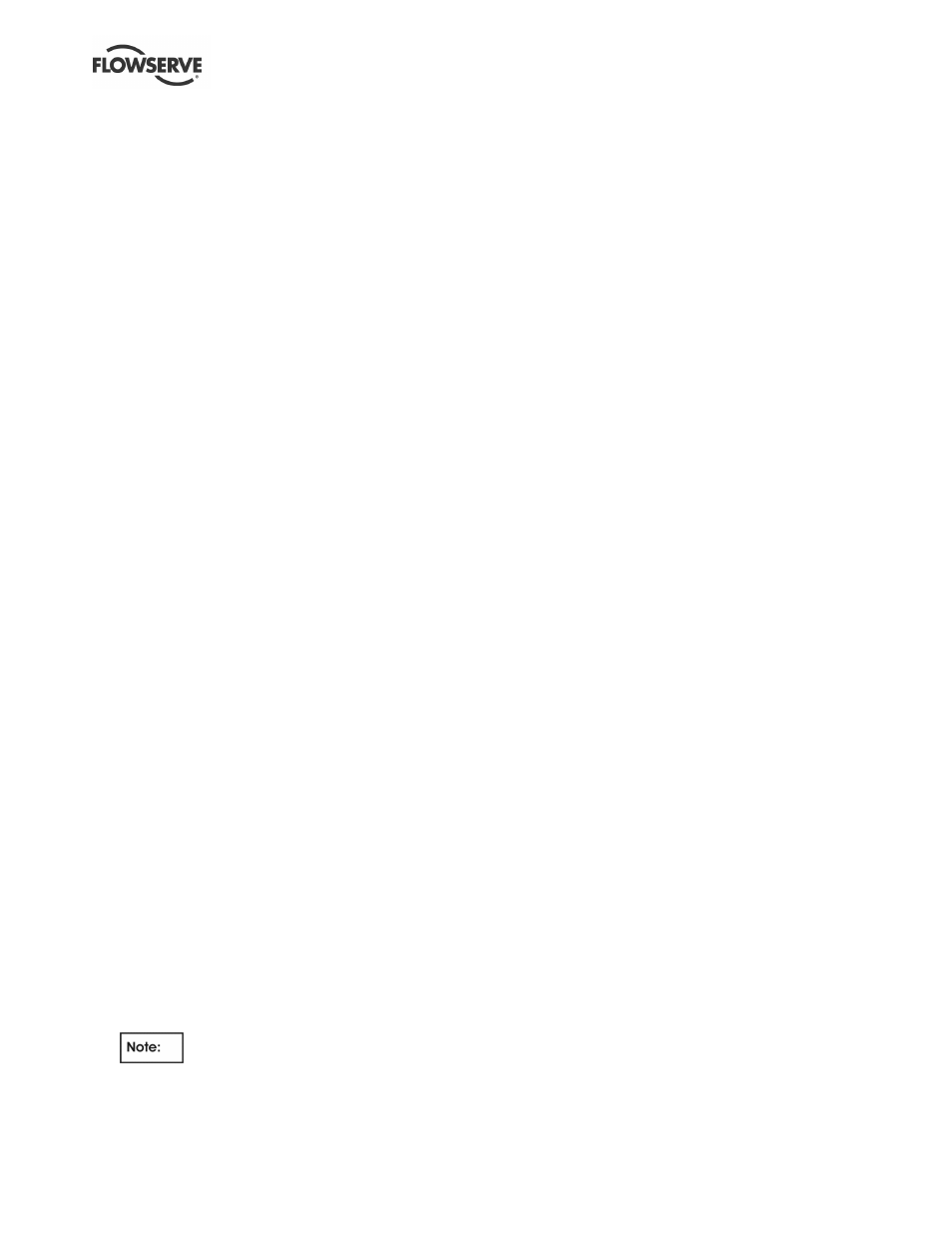
WR and CR USER INSTRUCTIONS ENGLISH 26999968 10-12
Page 18 of 28
flowserve.com
f)
These pumps can also be fitted with various
proprietary mechanical seals and the
manufacturer’s instructions should be followed
when dismantling and assembling.
g) It should not be necessary to remove the pump
shaft from the motor shaft during routine
maintenance. However, if this becomes absolutely
necessary, use either of the following procedures:
•
Insert a screw into the threaded hole in the end
of the pump shaft. The screw should have a
plain portion of length and diameter to engage
the bottom of the hole without damaging its
threads. The screw can then be tightened to
pull the pump shaft from the motor shaft.
•
By using two levers the pump shaft and using
the motor flange as a fulcrum the shaft can be
gently prised away from the motor shaft. It is
easier if this operation is carried out with the
motor stood vertically on its intake cover.
h) It is recommended that a new tolerance ring be
fitted once the pump shaft has been removed.
6.8 Examination of parts
Used parts must be inspected before assembly to
ensure the pump will subsequently run properly. In
particular, fault diagnosis is essential to enhance pump
and plant reliability.
6.8.1 Casing, seal housing and impeller
Inspect for excessive wear, pitting, corrosion, erosion or
damage and any sealing surface irregularities. Replace
as necessary.
6.8.2 Shaft and sleeve (if fitted)
Replace if grooved, pitted or worn.
6.8.3 Gasket, O-rings and lip seals
After dismantling, discard and replace.
6.9 Assembly
To assemble the pump, consult the sectional drawings.
(See section 8, Parts lists and drawings.)
Ensure threads, gasket and O-ring mating faces are
clean. Apply thread sealant to non-face sealing pipe
thread fittings.
a) To refit the pump shaft, screw a long stud into the
end of the motor shaft and pull the pump shaft on
by tightening a nut onto the stud. A washer
should be used between the nut and the shaft to
avoid damage to the shaft end.
b)
Make sure that the slot in the tolerance
ring is placed on the opposite side to the keyway
in the motor shaft.
c) Whilst re-assembling, use new gaskets and make
sure that they are in their correct positions -
grease can be used to help hold the gaskets in
place during assembly.
d) The stuffing box, if fitted, should be packed with
good quality packing, suitable for the liquid
handled. Packing should be renewed before it
becomes hard and if fresh packing is required do
not replace the outer rings only, but always all the
rings at the same time.
e) It is important to replace the lantern ring and the
packing seating ring in their correct positions to
ensure that the lantern ring is situated in line with
the gland seal connections. The correct
sequence is as follows: packing seating ring, two
rings of packing, lantern ring and finally two rings
of packing. (See sectional drawings.)
f) These pumps can also be fitted with various
proprietary mechanical seals and the
manufacturer’s instructions should be followed
when dismantling and assembling.
g) Impeller hub rings and casing renewable rings,
where fitted, should be checked for excessive
wear or damage. The diametrical clearance
should be measured, as a general guide, it is
recommended that replacement should be
carried out when the diametrical clearance
exceeds 1.20 mm. A fall off in performance may
necessitate earlier action. (See chart.)