4 performance and operating limits, 4 installation, 1 location – Flowserve WR User Manual
Page 11: 2 part assemblies, 3 foundation, 4 grouting, 5 piping
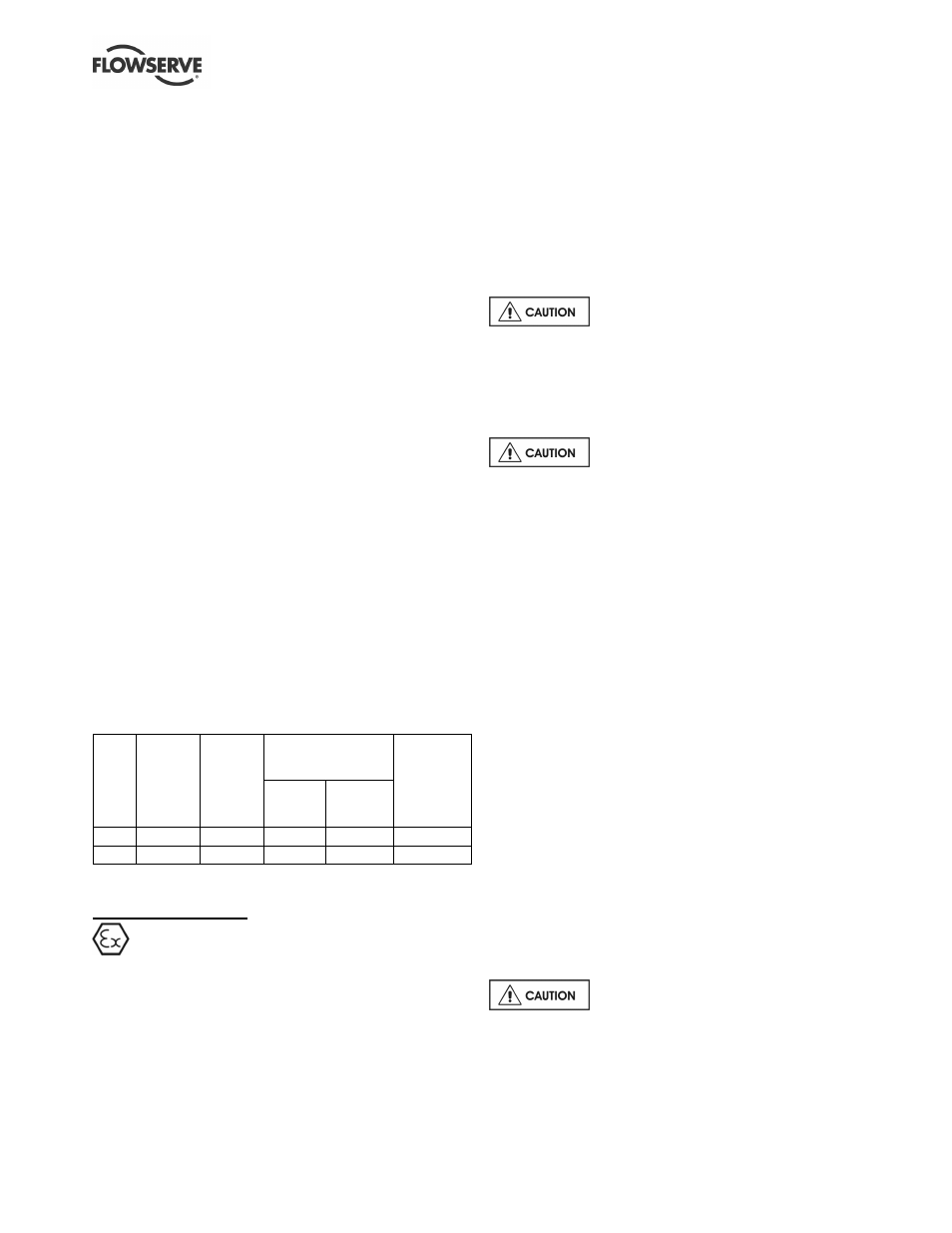
WR and CR USER INSTRUCTIONS ENGLISH 26999968 10-12
Page 11 of 28
flowserve.com
3.3.5 Seal housing
The seal housings designs provide improved
performance of mechanical seals
3.3.6 Shaft seal
The mechanical seal(s) attached to the pump shaft
seals the pumped liquid from the environment. Gland
packing may be fitted as an option.
3.3.7 Driver
The pump is driven by a close-coupled electric motor.
The position of the terminal box can be changed by
rotating the complete motor. To do this, remove the
fasteners from the motor flange, rotate the motor and
re-fit the fasteners.
3.3.8 Accessories
Accessories may be fitted when specified by the
customer.
3.4 Performance and operating limits
This product has been selected to meet the
specifications of the purchase order. (See section 1.5.)
These pumps are generally fitted with TEFC motors
with an ambient temperature limit of 40°C. Specifi c
pumps may be fitted with motors to suit client's
requirements with other ambient temperature limits -
see motor nameplate for details.
3.4.1 Pressure limits
The operating pressure has been selected to meet
your specified requirements. See paragraph 1.5,
Duty conditions, for details.
Pump
type
Max.
working
pressure
(bar)
Test
pressure
(bar)
Recommended
max. suction
pressure (bar)
Liquid
temperature
limits
(
°
C)*
1 450 &
1 750
rpm
2 900 &
3 500 rpm
WR
16
24
5.2
2.75
-20 to 110
CR
16
24
5.2
2.75
-20 to 110
* 140 ºC with internal water cooled box (not WS No.1 seal)
4 INSTALLATION
Equipment operated in hazardous locations
must comply with the relevant explosion protection
regulations. See section 1.6.4, Products used in
potentially explosive atmospheres.
4.1 Location
The pump should be located to allow room for access,
ventilation, maintenance and inspection with ample
headroom for lifting and should be as close as
practicable to the supply of liquid to be pumped. Refer
to the general arrangement drawing for the pump set.
4.2 Part assemblies
These pumps are not normally supplied in part
assemblies but special accessories such as loose
orifice plates are supplied loose. Ensure these are
incorporated in the final installation.
4.3 Foundation
There are many methods of installing
pump units to their foundations. The correct method
depends on the size of the pump unit, its location and
noise and vibration limitations. Non-compliance with
the provision of correct foundation and installation
may lead to failure of the pump and, as such, would
be outside the terms of the warranty.
Pumps should not be mounted with the
motor below the pump casing.
Pumps with motors up to D132 Frame size are bolted
to the foundations by the mounting bracket. Larger
sizes with D160 and larger motor frames are
mounted by the motor feet.
It is recommended that bolts (not studs) are used to
hold down the pump feet to permit easy removal from
the pipework.
These close coupled pumps feature a back pull-out
design. This means that when correctly installed, the
rotating element can be withdrawn from the casing
without disturbing the system pipework. The use of
grouted-in studs to secure the motor feet prevents
back pull-out and will make maintenance more
difficult and time consuming. The procedures in the
above paragraphs should be followed in order to
obtain the maximum benefit from the pump design.
4.4 Grouting
Where applicable, grout in the foundation bolts.
Foundation bolts should only be fully tightened when
the grout has cured.
4.5 Piping
Protective covers are fitted to the pipe
connections to prevent foreign bodies entering during
transportation and installation. Ensure that these
covers are removed from the pump before connecting
any pipes.