Impeller clearance, Direction of rotation, Guarding – Flowserve Durco Mark 3 ISO Frame Mounted User Manual
Page 22: Priming and auxiliary supplies, Direction of rotation (5.4), Guarding (5.5), Lubrication schedule (see 6.2.3), Priming and auxiliary supplies (5.6), Recommended grease lubricants (5.2.3), 3 impeller clearance
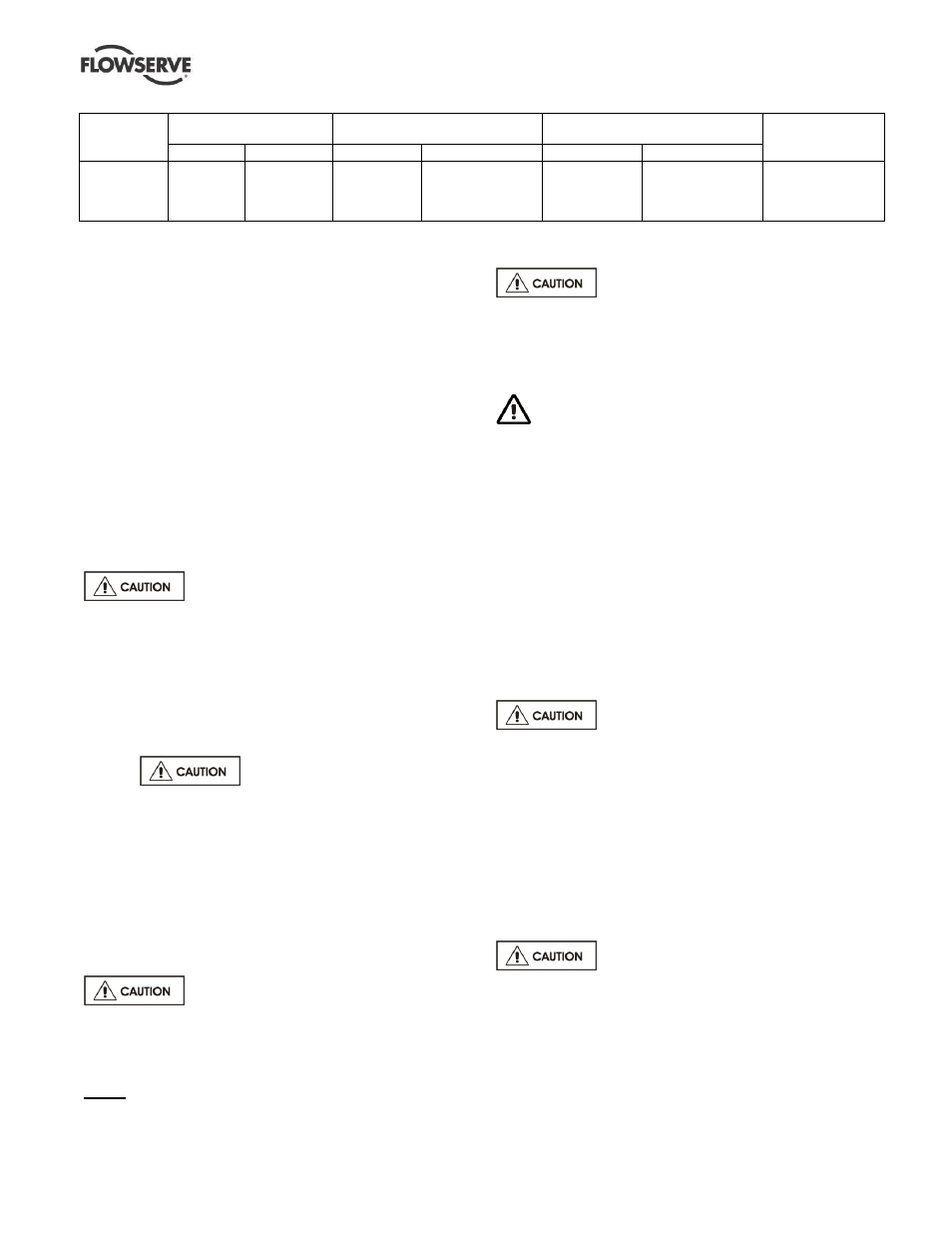
DURCO MARK 3 ISO FRAME MOUNTED ENGLISH 85392719 12-14
Page 22 of 52
flowserve.com
Frame size
Oil lubricated
medium duty bearings
Oil lubricated
heavy duty bearings
Oil lubricated optional
heavy duty bearings
Frame oil capacity
(approx.) *
litre (fl.oz)
Pump end
Drive end
Pump end
Drive end
Pump end
Drive end
1
2
3
4
6207 C3
6309 C3
6311 C3
6313 C3
3306 C3
3309 C3
3311 C3
3313 C3
6207 C3
6309 C3
6311 C3
6313 C3
7306 back-to-back
7309 back-to-back
7311 back-to-back
7313 back-to-back
NUP 207 C3
NUP 309 C3
NUP 311 C3
NUP 313 C3
7306 back-to-back
7309 back-to-back
7311 back-to-back
7313 back-to-back
0.5 (17)
1.0 (34)
0.8 (27)
1.6 (54)
Note: the bearing sizes do not constitute a purchasing specification.
* Sump volume only, does not include the oil in the constant level oiler.
5.2.3
Recommended grease lubricants
NLGI grade 2 is generally advised for horizontal bearing
housings and NLGI 3 where the bearing housing is used
vertically. The bearings are pre-greased. The NLGI 2
grade fitted in the factory with grease nipples is Mobil
Polyrex EM grease which has a Polyurea soap
incorporating a mineral oil. NLGI 3 grade is
recommended for vertical applications, if vertical
orientation was specified with order, then the NLGI 3
grease fitted in the factory for vertical application is Mobil
Polyrex EM103 grease or equivalent which has a
Polyurea soap incorporating a mineral oil. These greases
are suitable for high bearing and ambient temperatures
and ambient down to at least -20 °C. Below this ambient,
specialist greases may be required and Shell Aeroshell 22
is normally required for the minimum ambient down to
nitrile limitation of -45 °C.
Different types or grades of greases must
never be mixed.
Food grade grease, when applicable
5.2.3.1
NSF H1 Klubersynth UH1 64-62 is the food grade
grease option and it is NLGI grade 2.
5.2.4
Recommended fill quantities
Refer to section
5.2.2, Bearing sizes and capacities.
5.2.5
Lubrication schedule
Refer to section 6.2.3.
5.3
Impeller clearance
The impeller clearance is set in the factory. The
clearance may require adjustment because of high
liquid temperature. If piping attachment alters the
impeller clearance then correct piping. For setting
instructions see section 6.7, Setting impeller clearance.
5.4
Direction of rotation
Serious damage can result if the pump is
started or run in the wrong direction of rotation.
The pump is shipped with the coupling element removed.
Ensure the direction of rotation of the motor is correct
before fitting the coupling element. Direction of rotation
must correspond to the direction arrow.
If maintenance work has been carried
out to the site's electricity supply, the direction of
rotation should be re-checked as above in case the
supply phasing has been altered.
5.5
Guarding
Guarding is supplied fitted to the pump set.
In member countries of the EU and EFTA, it is a legal
requirement that fasteners for guards must remain
captive in the guard to comply with the Machinery
Directive 2006/42/EC. When releasing such guards,
the fasteners must be unscrewed in an appropriate way
to ensure that the fasteners remain captive.
Whenever guarding is removed or disturbed ensure that
all the protective guards are securely refitted prior to
start-up.
5.6
Priming and auxiliary supplies
5.6.1
Filling and priming, non self-primer casing
Ensure inlet pipe and pump casing is
completely full of liquid before starting continuous duty
operation.
Priming may be carried out with an ejector, vacuum
pump, interceptor or other equipment, or by flooding
from the inlet source.
When in service, pumps using inlet pipes with foot
valves may be primed by passing liquid back from the
outlet pipe through the pump.
5.6.2
Filling and priming, self-priming casing
Fill the pump with liquid to be pumped, or
compatible liquid, via the filling hole, before starting
continuous duty operation. The pump has self-priming
action for which a separate air pump is not normally
required.