2 system overview – BECKHOFF CX9020 User Manual
Page 7
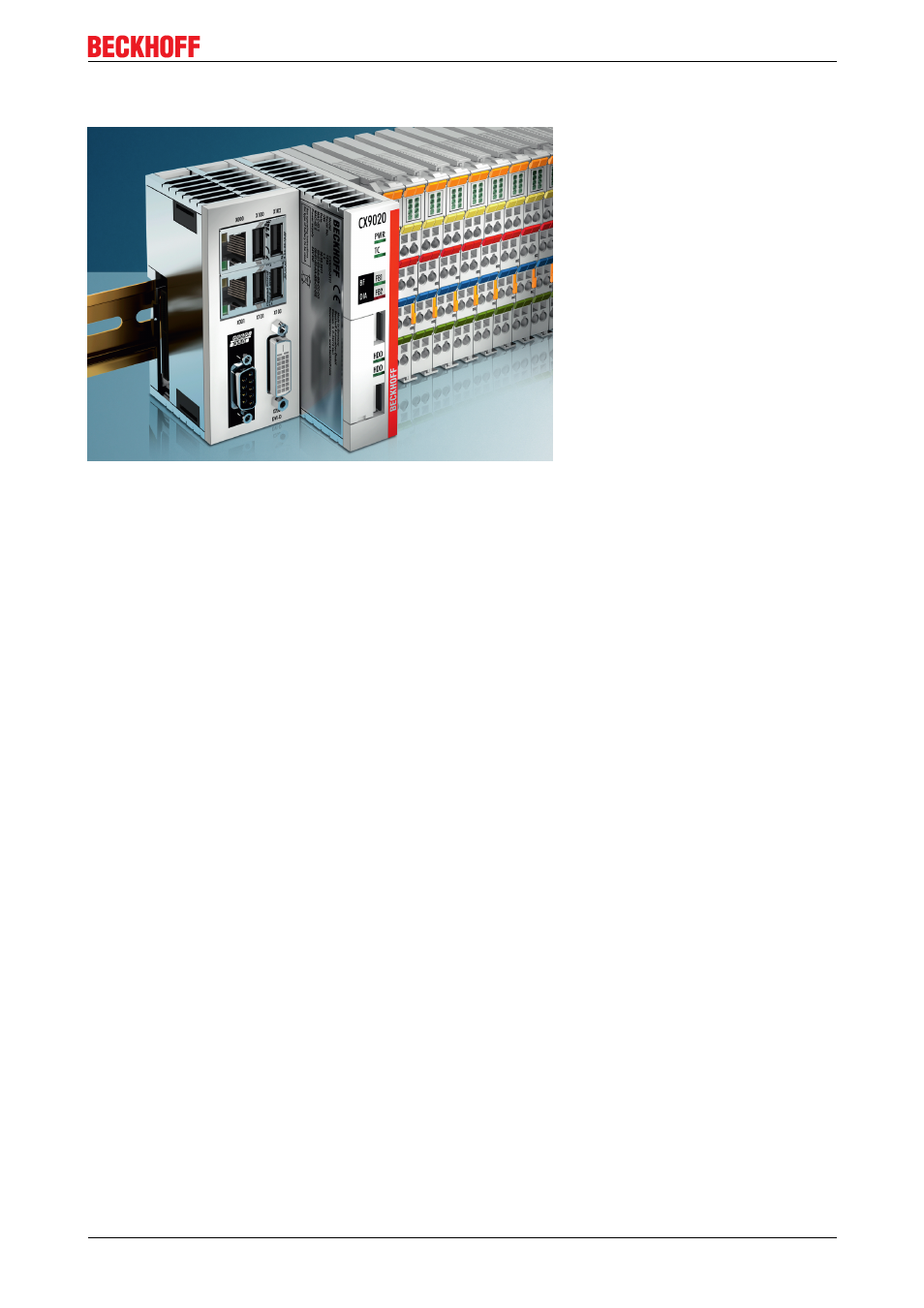
Product overview
2.2
System overview
The system
The CX9020 is a compact, DIN railmountable Ethernet control system with 1 GHz ARM Cortex™ A8 CPU.
The connection for the Beckhoff I/O systems is directly integrated into the CPU module. The unit offers
automatic bus system identifi cation (Kbus or Ebus) and independently switches in the corresponding
mode. The CX9020 comprises the CPU with two microSD card slots, the internal RAM and 128 kB NOVRAM
as nonvolatile memory. The basic configuration also includes two switched Ethernet RJ 45 interfaces, four
USB2.0 interfaces and a DVID interface. The RJ 45 interfaces are connected to an internal switch and offer
a simple option for creating a line topology without the need for additional Ethernet switches. The operating
system is Microsoft Windows Embedded Compact 7. TwinCAT 2 automation software transforms a CX9020
system into a powerful PLC and Motion Control system that can be operated with or without visualisation.
Optionally, the unit can be ordered with a fi eldbus, serial or audio interface.
The extended operating temperature range between 25 and +60 °C enables application in climatically
demanding situations.
EtherCAT as a fast I/O system
The CX9020 Embedded PC was developed for optimum interaction with EtherCAT.
Interestingly, EtherCAT offers several options for connecting conventional fieldbus systems to the CX9020:
As an EtherCAT device in terminal form. The PROFIBUS master is available either as a CX1500M310 or as
a EL6731 EtherCAT terminal. In practice, this means that the PROFIBUS master can be positioned exactly
where it is required within a machine. It no longer has to be implemented as a plugin card in the IPC or a
master controller in the control cabinet.
PLC, Motion Control, interpolation and visualisation
As a DIN rail IPC and in conjunction with the TwinCAT software from Beckhoff, the CX9020 offers the same
functionality as large Industrial PCs. In terms of PLC, up to four virtual IEC 61131 CPUs can be programmed
with up to four tasks each. All IEC 611313 languages can be used.
Moreover, all TwinCAT functionalities are available for Motion Control applications:
In theory, up to 256 axes can be controlled. In addition to simple pointtopoint movements, more complex
multiaxis functions such as “electronic gearbox”, “cam plates” and “flying saw” can be implemented.
In addition to realtime execution of control tasks, the TwinCAT realtime kernel ensures that enough time
remains for the user interface (HMI), to communicate with the realtime components via software interfaces
such as ADS or OPC.
CX9020
7
Version 1.1