I/o functions, Power system measurement functions, Contact sensing inputs – Basler Electric BE1-CDS240 General Information User Manual
Page 4: Contact outputs, I/o functions -2
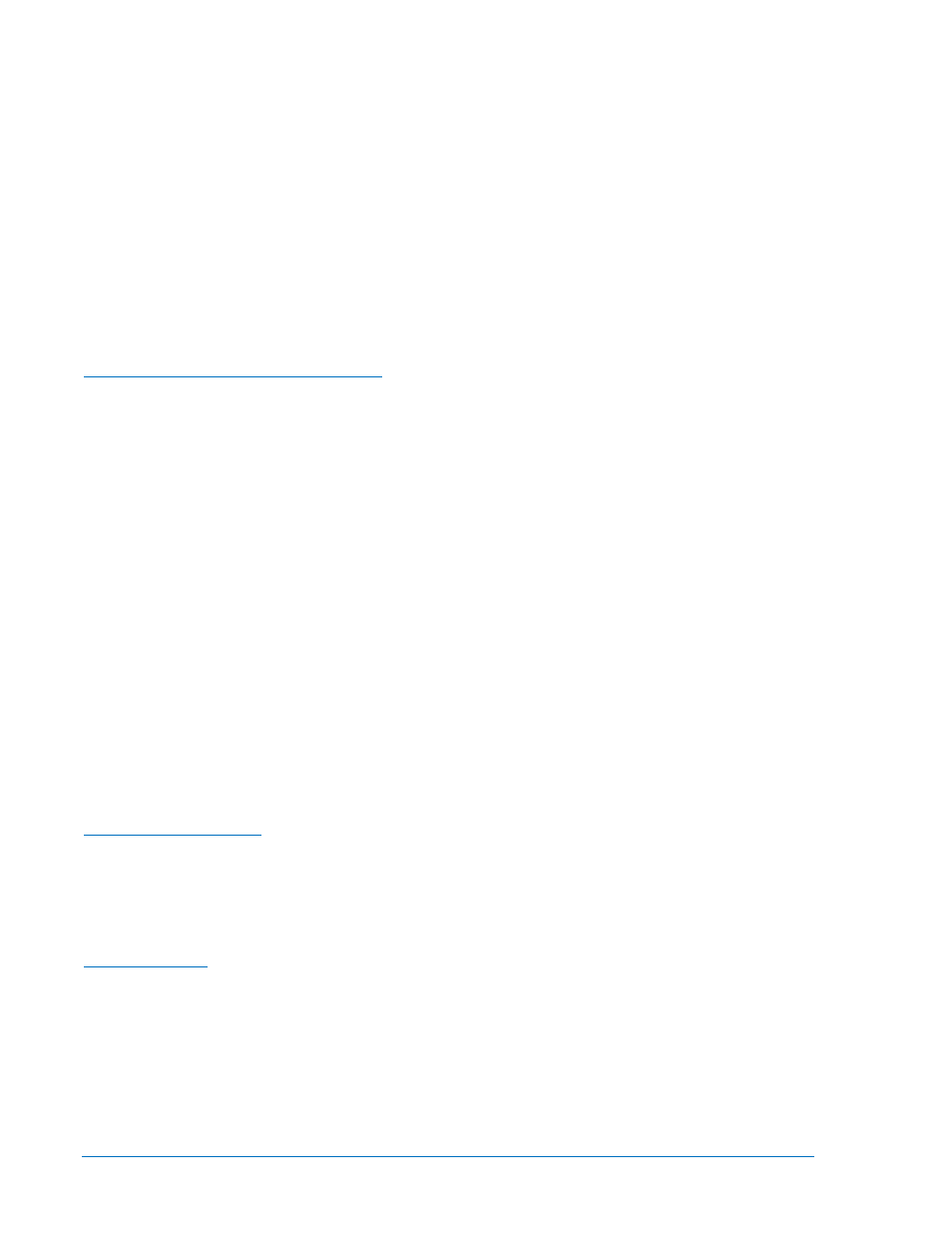
protection and control functions, metering functions, reporting and alarm functions, and various
communication options. A highly flexible programmable logic system called BESTlogic allows the user to
apply the available functions with complete flexibility and customize the system to meet the requirements
of the protected power system. Programmable I/O, extensive communications features, and an advanced
HMI (human machine interface) provide easy access to the features provided. Through BESTCOMS
software, BE1-CDS240 users with personal computers (PCs) have another easy-access means to
communicate, program, control, and monitor relay/system performance. BESTCOMS is a Windows®
(based software application that enhances communication between the PC user and the BE1-CDS240
relay. This software is provided free with every BE1-CDS240 relay. Another software application tool is
BESTWAVE. BESTWAVE is a utility program to view standard COMTRADE (Common Format for
Transient Data Exchange) files like those recorded by Basler Electric multifunction relays.
The following information summarizes the features included in this multifunction device. The organization
of this information outlines the organization for the rest of the manual. Each feature, along with how to set
it up and how to use the outputs is described in complete detail in the later sections of this manual.
I/O Functions
Power System Measurement Functions
•
The BE1-CDS240 has four sets of three-phase currents that are digitally sampled and digitally
filtered. The fundamental, second, and fifth harmonics are extracted using a Discrete Fourier
Transform (DFT) algorithm for use by all of the current based functions.
•
Neutral (residual) and negative-sequence current magnitudes are calculated from each set of
three-phase currents.
•
Each set of three-phase currents can be phase-shifted and tap compensated for use in
transformer differential applications.
•
Each three-phase current source can have its polarity reversed in the relay, which simplifies the
commissioning process in the event polarity of a CT circuit is rolled.
•
The digital sampling rate tracks the measured frequency to provide high accuracy at frequencies
other than nominal frequency to make this relay ideally suited for applications such as generator,
motor and generator step-up transformer differential protection.
•
An independent ground current input (IG) measures the current in a transformer neutral, tertiary
winding or a flux balancing CT and is used for providing ground differential protection.
•
Each current circuit is low burden and isolated to allow for more effective zoning with fewer costly
CTs.
•
Three-phase voltage inputs are digitally sampled and the fundamental frequency is extracted
using a Discrete Fourier Transform (DFT) algorithm. Voltage sensing circuits can be configured
for single-phase, three wire or four wire voltage transformer circuits.
Voltage sensing circuitry provides voltage protection, frequency protection, and watt/var
metering. Neutral (residual), positive, negative, and zero sequence voltage magnitudes are
calculated from the three-phase voltages.
Contact Sensing Inputs
•
Eight (I/O option E) or 12 (I/O option A) programmable contact sensing inputs with programmable
signal conditioning provide binary logic interface to the protection and control system.
•
The function of each input is programmable using BESTlogic and can be given a user meaningful
name for the variable and for each state (open and closed) for use in reporting functions.
•
The threshold voltage is adjustable. See Section 12, Installation, Contact Sensing Input Jumpers.
Contact Outputs
•
Fourteen (I/O option E) or 10 (I/O option A) programmable contact outputs provide a binary logic
interface to the protection and control system (OUT1 through 14). OUTA is dedicated to critical
alarms.
•
OUT1 and 2 are dedicated form “c” contacts. The remainders are “a” contacts. Outputs 7, 8, 9, 10
are dedicated to trip coil monitoring for up to 4 breakers. However, board level jumpers are
supplied so that the user can disable the TCM circuit and allocate the output contact to any virtual
output. Refer to Section 12, Installation, Trip Coil Monitor (TCM) Jumpers.
1-2
BE1-CDS240 General Information
9365200990 Rev M