Control features cont – WaterFurnace Series NXW User Manual
Page 22
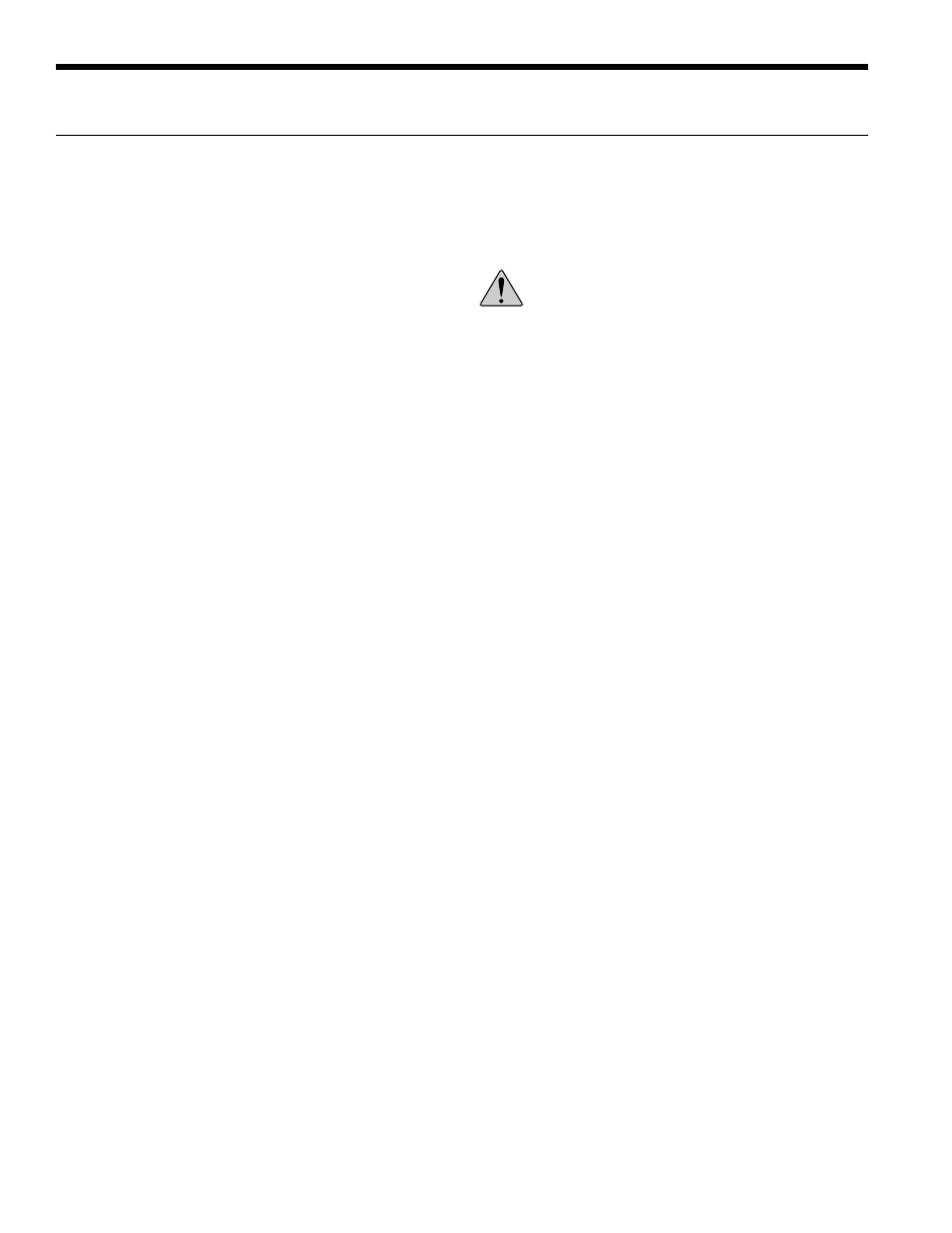
22
ENVISION
2
NKW 50Hz REVERSIBLE CHILLER INSTALLATION MANUAL
Control Features cont.
minimum on time does not apply if the high-pressure switch
trips. The compressor will not restart until the short cycle
time delay has been satisfied. If the high-pressure fault
occurs in one circuit the other compressor will continue to
operate based on the heating or cooling demand.
Low Pressure (DI-3 and DI-6)
The low-pressure switches shall be a normally closed (NC)
switch that monitors the systems compressor suction line
refrigerant pressure. The input shall be checked 15 seconds
before compressor start up to insure the pressure switch
is closed and then ignored for the first 2 minutes after the
compressor output (DO-1 or DO-2) is enabled. If the switch
is open continuously for (30) seconds the compressor
output for that circuit will be disabled. The compressor
will not restart until the short cycle time delay has been
satisfied. If a low-pressure fault occurs in one circuit the
other compressor will continue to operate based on the
heating or cooling demand.
Compressor 1 Alarm Output (DO-5)
The compressor 1 alarm output will be enabled when stage
1 is in the lockout mode and will be disabled when the
lockout is reset.
Compressor 2 Alarm Output (DO-6)
The compressor 2 alarm output will be enabled when stage
2 is in the lockout mode and will be disabled when the
lockout is reset.
Test Mode
The unit controls system can be put into test mode to
eliminate startup delays to aid in trouble shooting. To put
the unit into test mode hold the “ESC” and “Down Arrow”
keys until LED 8 begins to flash. The control will remain in
test mode until power is cycled or after 30 minutes.
Reversible Chiller Setpoint Control
This control software is by default set to operate in
‘Aquastat’ mode, which requires external setpoint logic to
generate the Y1 or Y2 call. The mode may be changed to
‘Setpoint’ by use of the ‘Settings’ menu in the MUI in the
‘Mode’ item which is on the 5th line from the top.
CAUTION! Setpoint mode is not recommended
on applications that have more than two
water-to-water heat pumps installed. Unique
temperature setting should be set for each unit
on a common load.
To operate in setpoint mode, consider the following:
•
The selected mode must be changed from Aquastat
to Setpoint
•
The ‘Y1’ input must be activated. This may be done
by connecting ‘R’ to ‘Y1’ on the terminal board, or by
commanding Y1 to ‘ON’ in the Maint menu of the MUI,
or by commanding the ComprEnable network variable
from the BAS.
•
The Heat/Cool mode is by default in the cooling mode,
and may be set to heating by connecting R to O/B on
the terminal board, or by commanding the ‘B’ item
in the Maint menu of the MUI, or by commanding the
reversing valve variable from the BAS network.
•
The setpoint mode temperature sensor can be selected
to either Load LW Temp (Leaving Water) or Load EW
Temp (Entering Water Temp). The default is set for
Entering Water Temp control.
•
The cooling setpoint and the heating setpoint are two
separate setpoints, and can be adjusted in the MUI
Settings menu.
•
When the controlling temperature sensor is set to
select the Load EW Temp, the setpoint control will
operate in a PID (Proportional-Integrating-Derivative)
mode. In this mode, the temperature rate of change
and direction of change will be part of deciding
whether or not to add or reduce capacity. Additionally
the amount of difference between setpoint and
temperature AND the length of time that the difference
existed are used to determine if adding or reducing
capacity is needed.
o
The tuning parameters for this mode should only
be adjusted if you know why you are choosing
the value that you plan to use. You should keep
a permanent record of the beginning values and
record any changes that you make. The parameters
used in PID operation and their (default values) are:
• D NegThrshld (-0.03)
• Int Rate (200)
• Stage Delay (30)
• Gain (2)
• D PosThrshld (0.04)
• PIDY1 Ref (7.2)
• PID Y1 Diff (7)
• PID Y2RefShift (5)
• PID Y2 Diff (6)